Preventing internal pores and defects in cast aluminum bronze involves a combination of careful material selection, proper casting techniques, and effective process control. Here are some strategies:
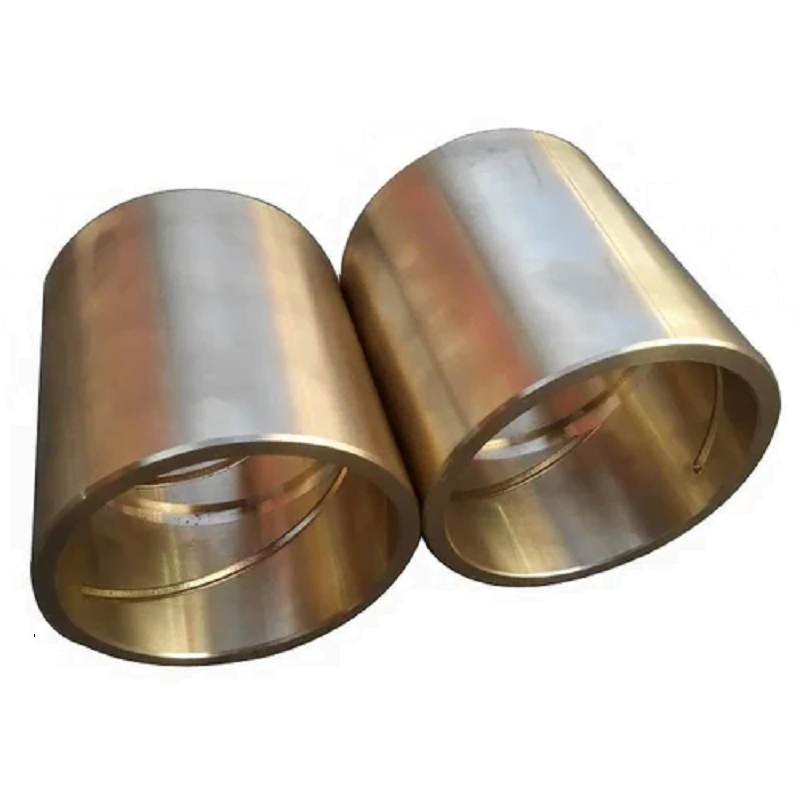
- Material Selection:
- Use high-quality aluminum bronze alloys with low impurity levels.
- Ensure that the alloy composition is well within the specified range to promote optimal casting properties.
- Melting Process:
- Use a controlled melting environment to minimize oxidation and contamination.
- Maintain proper temperatures to avoid overheating, which can lead to gas absorption.
- Degassing:
- Implement degassing techniques, such as using inert gases (e.g., argon) or chemical degassers, to remove dissolved gases from the molten metal.
- Mold Design:
- Design molds with proper venting to allow gases to escape during pouring.
- Ensure molds are free of moisture and contaminants, which can lead to gas generation.
- Pouring Techniques:
- Control pouring temperature and speed to reduce turbulence, which can introduce air entrapment.
- Use a ladle with a design that minimizes splashing.
- Tốc độ làm mát:
- Control the cooling rate to prevent rapid solidification, which can lead to the formation of micro-porosity.
- Post-Casting Treatments:
- Consider heat treatments or aging processes that can help relieve internal stresses and reduce porosity.
- Kiểm soát chất lượng:
- Implement non-destructive testing methods (e.g., X-ray or ultrasonic testing) to identify internal defects early in the process.
By combining these practices, you can significantly reduce the risk of internal pores and defects in cast aluminum bronze.