Incoloy 800 และ Inconel 600 เป็นโลหะผสมนิกเกิล-เหล็ก-โครเมียม แต่มีองค์ประกอบและการใช้งานแตกต่างกัน นี่คือการเปรียบเทียบประสิทธิภาพและราคา:
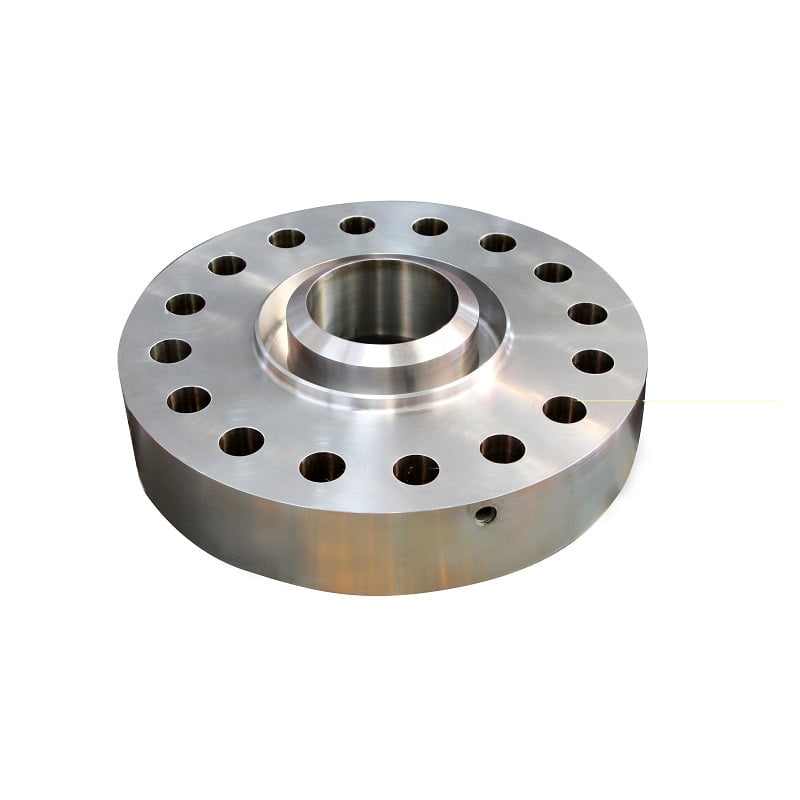
องค์ประกอบ:
อินคอลอยย์ 800 (อัลลอย 800):
- ส่วนประกอบ: ส่วนใหญ่เป็นนิกเกิล โดยมีโครเมียมและเหล็กในปริมาณมาก มีการเติมอะลูมิเนียมและไทเทเนียมเล็กน้อยเพื่อปรับปรุงคุณสมบัติที่อุณหภูมิสูง
- ลักษณะหลัก: ออกแบบมาสำหรับการใช้งานที่อุณหภูมิสูง ทนต่อการเกิดออกซิเดชัน และต้านทานการเกิดคาร์บูไรเซชัน
อินโคเนล 600 (อัลลอย 600):
- ส่วนประกอบ: โลหะผสมนิกเกิล-โครเมียมที่มีความต้านทานการเกิดออกซิเดชันที่ดีที่อุณหภูมิสูงขึ้น ประกอบด้วยเหล็กเป็นโลหะฐานและโครเมียมเพื่อต้านทานการเกิดออกซิเดชัน
- ลักษณะหลัก: เป็นที่รู้จักในด้านคุณสมบัติทางกลที่ดีเยี่ยมและมีความแข็งแรงสูง พร้อมด้วยความต้านทานต่อการแตกร้าวจากการกัดกร่อนจากความเค้นและการเชื่อมที่ดี
ผลงาน:
- อินคอลอยย์ 800:
- ประสิทธิภาพที่อุณหภูมิสูง: ทนทานต่อการเกิดออกซิเดชัน คาร์บูไรเซชัน และไนไตรเดชันได้ดีเยี่ยมในสภาพแวดล้อมที่มีอุณหภูมิสูง
- ความต้านทานการกัดกร่อน: ทนทานต่อสภาพแวดล้อมที่มีฤทธิ์กัดกร่อนต่างๆ ได้ดี รวมถึงบรรยากาศที่มีกำมะถัน
- ความแรงของการคืบคลานและการแตกร้าว: คงความแข็งแรงและทนทานต่อการเสียรูปของการคืบคลานที่อุณหภูมิสูงได้ดี
- อินโคเนล 600:
- ประสิทธิภาพที่อุณหภูมิสูง: ทนทานต่อการเกิดออกซิเดชันและขยายตัวได้สูงถึงประมาณ 2000°F (1093°C)
- ความต้านทานการกัดกร่อน: ดีเยี่ยมในสารกัดกร่อนหลากหลายชนิด รวมถึงสภาวะออกซิไดซ์และรีดิวซ์
- คุณสมบัติทางกล: มีความแข็งแรงสูงและมีความสามารถในการผลิตที่ดี ทำให้เหมาะกับงานอุตสาหกรรมต่างๆ
ราคา:
- อินคอลอยย์ 800 โดยทั่วไปมีแนวโน้มที่จะมีราคาแพงกว่า Inconel 600 เนื่องจากมีองค์ประกอบและคุณสมบัติพิเศษที่ออกแบบมาสำหรับการใช้งานที่อุณหภูมิสูง
- อินโคเนล 600 ค่อนข้างประหยัดกว่า แม้ว่าราคาอาจแตกต่างกันไปตามสภาวะตลาดและรูปแบบเฉพาะ (แผ่น แผ่น ท่อ ฯลฯ)
การใช้งาน:
- อินคอลอยย์ 800: ใช้ในส่วนประกอบเตาเผา อุปกรณ์กระบวนการปิโตรเคมี อุปกรณ์รักษาความร้อน และโรงไฟฟ้านิวเคลียร์ที่ความต้านทานความร้อนและการกัดกร่อนเป็นสิ่งสำคัญ
- อินโคเนล 600: ใช้กันอย่างแพร่หลายในการแปรรูปทางเคมีและอาหาร วิศวกรรมนิวเคลียร์ ส่วนประกอบเตาหลอม และสำหรับการใช้งานที่ต้องการคุณสมบัติทางกลสูงและทนต่อการกัดกร่อน
สรุป:
- อินคอลอยย์ 800 เป็นที่ต้องการโดยความแข็งแรงที่อุณหภูมิสูงและความต้านทานต่อการเกิดออกซิเดชันเป็นสิ่งสำคัญยิ่ง
- อินโคเนล 600 ถูกเลือกเนื่องจากคุณสมบัติทางกลที่ยอดเยี่ยมและความต้านทานการกัดกร่อนที่ดีในสภาพแวดล้อมที่หลากหลาย
การเลือกระหว่าง Incoloy 800 และ Inconel 600 ขึ้นอยู่กับข้อกำหนดการใช้งานเฉพาะเป็นส่วนใหญ่ โดยเฉพาะอย่างยิ่งเกี่ยวกับอุณหภูมิ สภาพแวดล้อมการกัดกร่อน ความเค้นเชิงกล และข้อจำกัดด้านงบประมาณ