The choice between 8620 steel and 1045 steel depends on the specific application and requirements. Here’s a comparison to help you decide:
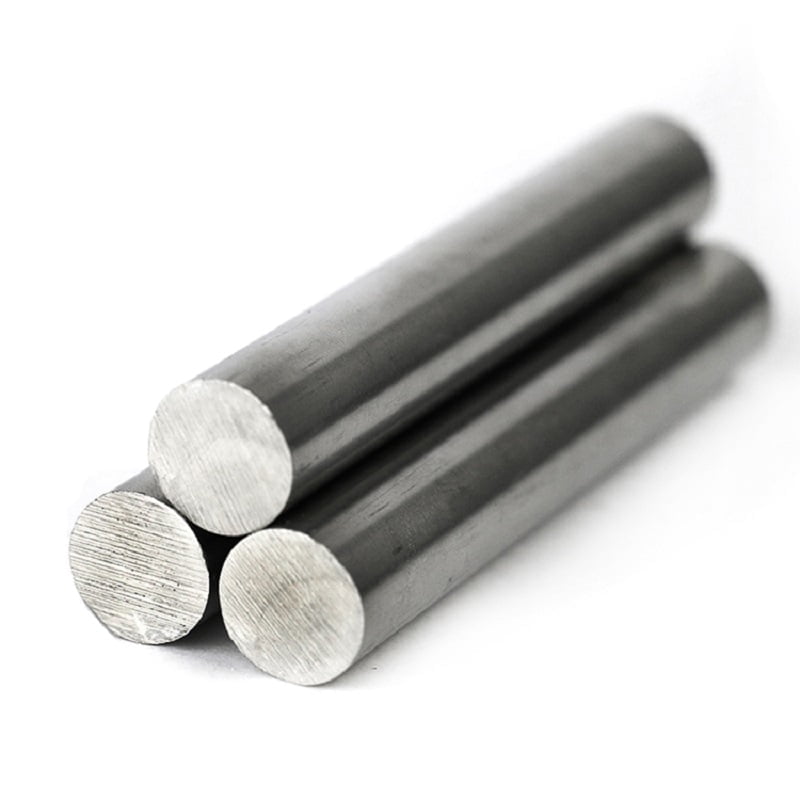
- 8620 Steel:
- Strengths: Known for its toughness and high strength, especially after heat treatment.
- Uses: Commonly used in gears, crankshafts, and other machinery components that require good core strength and toughness.
- Properties: Contains nickel, chromium, and molybdenum, which contribute to its hardenability and toughness.
- 1045 Steel:
- Strengths: Offers good strength and impact properties at a lower cost compared to other steel alloys.
- Uses: Widely used for axles, bolts, studs, and hydraulic shafts where higher strength and good machinability are required.
- Properties: Medium carbon steel, easy to machine, and can be heat treated to reach a wide range of mechanical properties.
Considerations:
- Strength and Toughness: If your application requires high strength and toughness, especially after heat treatment, 8620 steel might be preferable.
- Machinability: 1045 steel is easier to machine due to its lower carbon content, which might be advantageous depending on your manufacturing processes.
- Cost: 1045 steel is generally more cost-effective than 8620 steel, which could influence your decision if cost is a significant factor.
- Specific Requirements: Consider any specific requirements for hardness, wear resistance, or other mechanical properties that might favor one steel over the other.
In summary, if you need higher strength and toughness, especially for components subjected to high stresses, 8620 steel could be the better choice. If ease of machining and cost-effectiveness are priorities, then 1045 steel might be more suitable. Always verify with your specific application and consult with materials engineers or suppliers to ensure the chosen steel meets all requirements.