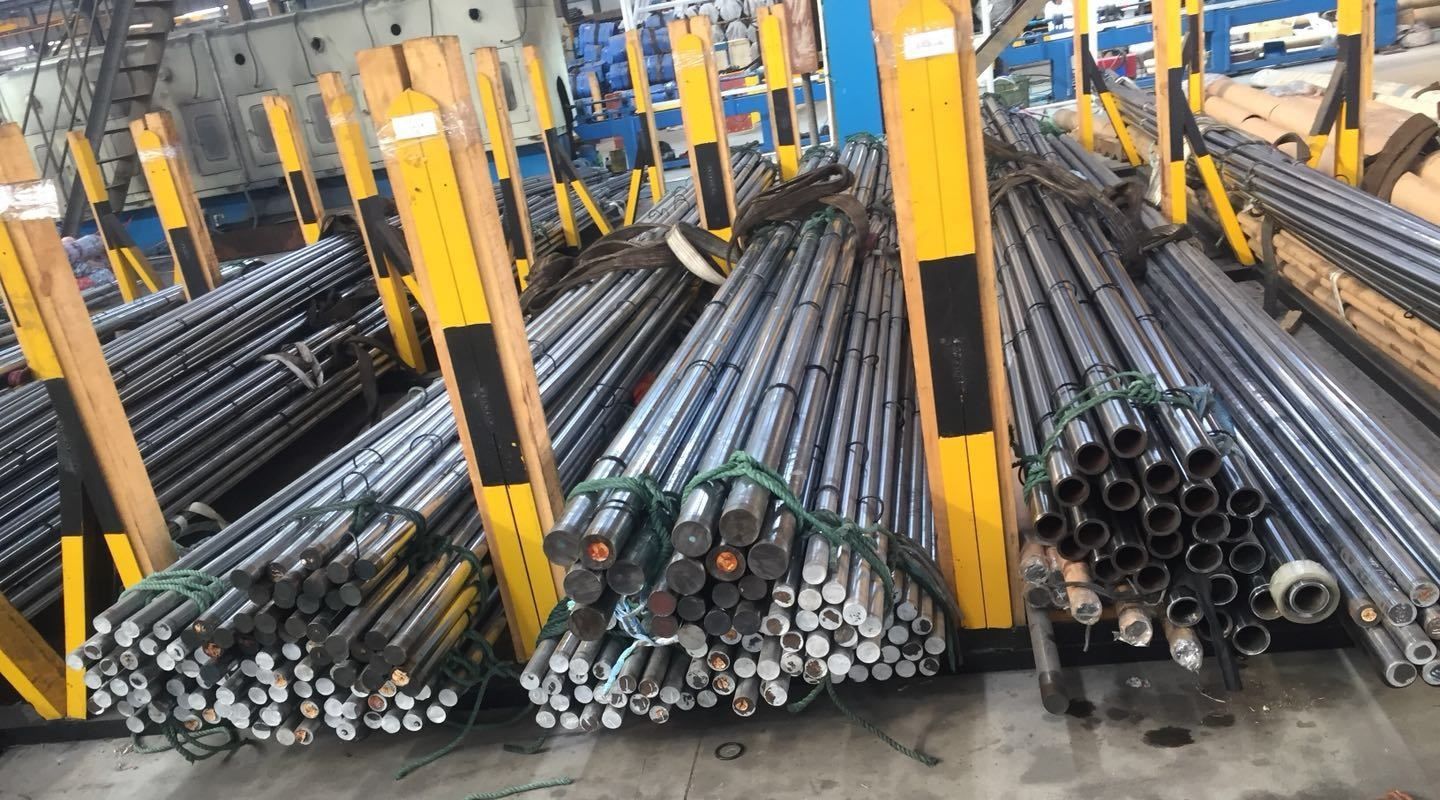
Содержание этой страницы получено из Iqsdirectory.com
Введение
Это наиболее полное руководство по холодной ковке, доступное в Интернете.
В этой статье рассматриваются следующие темы:
- Что такое холодная ковка и как она работает
- Cold forging benefits & disadvantages
- Горячая ковка против холодной ковки
- Используемые металлы и оборудование/машины
- Применение холодной ковки
- И более…
Глава первая – Что такое холодная ковка и как она работает?
Cold forging is a metal shaping & manufacturing process in which bar stock is inserted into a die and squeezed into a second closed die. The process, completed is at room temperature or below the metal‘s recrystallization temperature to form a metal into a desired shape or configuration.
Холодная ковка — это эффективный и экономичный процесс деформации металла для производства больших объемов деталей по низкой цене. Существует три метода ковки, которые различаются в зависимости от температуры, они могут быть холодными, теплыми или горячими и включают использование молотков, штампов или прессов для придания формы, сжатия, деформации и прокатки металлов. Холодную ковку не следует путать с механической обработкой или литьем, поскольку конечным результатом является более прочный и качественный продукт.
В отличие от горячей или горячей ковки, холодная ковка формирует и деформирует прутковый прокат при комнатной температуре с использованием локализованной сжимающей силы. В зависимости от требований конструкции детали, заготовка может проходить через несколько штампов или ударяться несколько раз подряд для достижения нужной формы.
Глава вторая – Как работает холодная ковка
Низкая стоимость холодной ковки обусловлена снижением трудозатрат и устранением вторичной обработки. Детали производятся быстро и эффективно со скоростью до 1000 штук в час, что снижает себестоимость единицы продукции. Производство заключается в том, чтобы просто вставить металлическую деталь и позволить машинам быстро и эффективно выполнять работу.
Готовые изделия из холодной ковки имеют идеальное качество поверхности и повышенную стабильность размеров, что видно на изображении ниже. Различные процессы повышают прочность и долговечность заготовки, производя долговечные изделия или детали.
Процесс холодной ковки
Шаг 1: Смазка
– Перед ковкой заготовку обрабатывают смазкой, чтобы предотвратить ее прилипание к штампу и сохранить ее прохладной в процессе формовки, так как деформация может производить температуры от 250° до 450°.
Шаг 2: Вставка металлической детали
– Металлическая деталь помещается на матрицу, имеющую форму конечной детали. Матрица может иметь две секции, одна из которых прикреплена к молотку, а другая находится под заготовкой. Молоток — это верхняя часть и ударный механизм, создающий усилие для деформации металлической детали.
Шаг 3: Инсульт
– Удар заготовки, или ход, может производиться тремя механизмами – гидравлическим, пневматическим или механическим. Каждый из методов приводит в действие вал с молотком на нем с большим усилием вниз на заготовку, чтобы создать желаемую форму. Это происходит в пределах миллисекунд. В некоторых случаях молоток приходится бросать несколько раз подряд, чтобы получить точный контур и форму.
Шаг 4: Вспышка
– Заусенец – это лишний металл вокруг штампа или комплекта штампов. Он выступает из тела поковки в виде тонкой пластины, где встречаются штампы, и удаляется во время обрезки. Вспышка ограничивает поток металла, обеспечивая идеальный оттиск. Наличие облоя необходимо для того, чтобы металл полностью заполнил форму.
Шаг 5: Удаление детали
– Метод удаления детали зависит от типа процесса. Большинство современных производителей используют автоматику для удаления детали конвейером или роботизированной рукой. Это еще одна мера экономии, которая устраняет необходимость в обработке материалов.
Шаг 6: После формирования
– Как и в других частях процесса, это может принимать разные формы. Для деталей, требующих одного штампа и одного хода, деталь обрезается и отправляется на отгрузку. В случае деталей, которые имеют несколько граней, они перемещаются в другие процессы штамповки для добавления функций. Перемещение штампа от станции к станции обычно автоматизировано. Для более крупных деталей используются другие механизированные методы, которые могут включать хай-лоу, вилочный погрузчик или кран.
ВНЕСИТЕ ВАШУ КОМПАНИЮ В СПИСОК НИЖЕ
Глава третья – Преимущества холодной ковки
В этой главе подробно обсуждаются шесть основных преимуществ холодного граничения. Они включают:
- Экономически эффективным
- Более быстрое производство
- Экологически чистый
- Превосходная производительность продукта
- Высокая производительность
- Широкий выбор металлов
Информация ниже описывает некоторые преимущества холодной ковки и почему она так широко используется. Глава третья представляет собой сравнение холодной ковки с горячей ковкой и преимущества каждой из них.
Экономически эффективным:
Холодная ковка имеет низкую себестоимость за счет 3-х факторов – предварительной обработки, температуры и отделки. В других методах формообразования металла заготовка должна пройти некоторую предварительную обработку, например, нагрев. Печи, обжиговые печи или электричество обычно используются для повышения температуры металла выше точки его рекристаллизации. Они дороги в обслуживании, производят загрязняющие вещества и отнимают много времени.
При холодной ковке после обработки заготовка считается завершенной и требует минимальной доводки, что позволяет снизить трудозатраты.
Холодная ковка дает экономию материала до 70% от производственных затрат, поскольку отходов и брака очень мало.
Более быстрое производство:
Холодная ковка — это простой процесс, при котором заготовка помещается непосредственно в кузнечный станок для мгновенного изготовления готовой детали. Современные производители используют автоматику для загрузки заготовки и снятия ее с пресса. Как вы можете видеть на этой схеме, металл подается в станок, обрабатывается и движется дальше. Время между входом и финишем меньше секунды.
Экологически чистый:
Основной причиной того, что холодная ковка является экологически чистой, является устранение потребности в тепле, поскольку пары и дым из печей производят значительные выбросы углерода. Это также снижает затраты, поскольку производителям не нужно устанавливать оборудование для фильтрации и очистки воздуха.
Превосходная производительность продукта:
Холодная ковка позволяет производить изделия с превосходными характеристиками, поскольку она перестраивает зернистую структуру заготовки в соответствии с конфигурацией конечной детали.
Устраняет возможные негативные реакции:
Обработка металла может создать множество потенциальных проблем. Холодная ковка устраняет некоторые негативные эффекты, такие как усталость от пористости, за счет увеличения общей прочности металла и устранения риска потери целостности материала.
Повышенное качество и длительный срок службы:
Холоднокованые детали способны выдерживать высокие нагрузки. Когда заготовка выходит за пределы предела текучести или упругости, она все еще способна сохранять свою измененную форму.
Сохранение допусков деталей:
Критические и жесткие допуски деталей выдерживаются на протяжении всего производственного цикла. Они воспроизведены до мельчайших деталей, так что каждая часть является точной копией первой.
Свобода дизайна:
В отличие от других процессов, холодная ковка дает свободу проектирования, когда можно создавать сложные контуры и формы, которые потребуют множества различных и дорогостоящих вторичных методов в других процессах.
Высокая производительность:
Хотя между методами производства холодной штамповки могут быть различия, высокая скорость производства холодной штамповки может производить от 50 до более 400 штук в минуту. Единственное, что влияет на скорость процесса, - это размер детали.
Широкий выбор металлов:
Ковать можно широкий спектр металлов, включая твердые металлы, такие как углеродистая сталь, легированная сталь и нержавеющая сталь, а также мягкие металлы, такие как алюминий, латунь и медь.
Это изображение представляет собой образец болтов, изготовленных методом холодной ковки. Каждый из различных болтов был сделан из разного металла. В том числе из меди, латуни, алюминия и стали.
Глава четвертая – Горячая и холодная ковка
Разница между горячей ковкой и холодной ковкой заключается в температуре: холодная ковка деформирует и напрягает металлы при комнатной температуре, а горячая ковка нагревает металлы вблизи или при температуре их плавления.
Ключом к диапазону температур является рекристаллизация: холодная ковка происходит до рекристаллизации, а горячая ковка нагревает металл выше точки рекристаллизации.
Выбор холодной ковки или горячей ковки зависит от:
- Оборудование производителей и механическая обработка: производители специализируются на том или ином процессе, чтобы максимально использовать свое оборудование.
- Потребительский спрос: на этапе проектирования детали инженеры принимают решение о наилучшем процессе производства своих конструкций, поскольку холодная и горячая ковка имеют свои ограничения.
- Типы производимых деталей: Во многих случаях ограничения в отношении выбора правильного процесса определяются конструкцией детали, поскольку определенные детали могут быть изготовлены только горячей ковкой, в то время как другие идеально подходят для холодной ковки. Конструкции деталей холодной ковки просты без сложных деталей, в то время как горячая ковка позволяет получать детали с чрезвычайно точными мелкими деталями.
- Требования к более низкой стоимости: по возможности производители выбирают холодную ковку, поскольку она требует меньшего количества оборудования и не включает нагрев, что значительно снижает общую стоимость производства.
Горячая ковка
Горячая ковка выполняется при исключительно высоких температурах от 700°C или 1292°F до 1000°C или 1832°F. Повышенные температуры помогают избежать деформации и затвердевания, а также снижают поток напряжения и количество энергии, необходимой для деформации и деформации. формировать металлы. Когда металлы остывают, они сохраняют свою деформированную форму. В процессе формовки используются гидравлические, пневматические и механические прессы.
Характеристики горячей штамповки:
Штампы или пресс-формы:
Одним из основных расходов на горячую ковку является стоимость, необходимая для производства штампов и форм, изготовленных из упрочненной стали, способной выдерживать экстремальные температуры, способной противостоять усталости и иметь пластичность, ударную вязкость и прочность на растяжение.
Формы горячей ковки:
Хотя многие из методов горячей ковки аналогичны методам холодной ковки, другие методы включают газовую штамповку, закалку в штампе, вытяжку и изотермическую обработку.
Температура металла:
Тип процесса определяет температуру металла при его формовании. В некоторых процессах металл полностью расплавляют и заливают в форму или проталкивают через матрицу. В других случаях он отжигается и формуется штампом или пресс-формой под давлением и прессованием.
Опасные факторы окружающей среды:
Самым большим недостатком является количество загрязняющих веществ, образующихся в процессе нагрева. Это было серьезной проблемой с момента ее возникновения во время первой промышленной революции, и производители постоянно сталкивались с ней на протяжении многих лет.
Нагрев металлов:
Детали необходимо нагревать выше точки рекристаллизации, которая значительно превышает 300°F и может доходить до 1000 градусов. Для достижения соответствующих температур требуются большие печи или сушильные камеры.
Затраченное время:
Сложный характер горячей штамповки требует времени для нагрева металла, его обработки и охлаждения. Хотя фактическая штамповка, деформация или придание формы занимают примерно столько же времени, сколько и холодная ковка, процессы нагрева и охлаждения требуют тщательного ухода и управления в течение длительного времени.
Результаты горячей штамповки:
Нагрев и охлаждение металлов увеличивают их прочность, ударную вязкость и пластичность, но уменьшают твердость. В процессе охлаждения металлы могут деформироваться и терять форму.
Масштабирование:
Горячая ковка может привести к окислению, которое приводит к образованию накипи, которая может обесцветить поверхность металла, что затруднит ее чистовую обработку.
Отделка:
Детали должны быть обработаны для устранения деформаций, дефектов и ошибок в процессе нагрева. Эти вторичные операции трудоемки и требуют нескольких видов специализированного оборудования.
Холодная ковка
Температура, при которой происходит ковка, отличает холодную ковку от горячей ковки. Для горячей штамповки детали ее нагревают до температуры выше точки рекристаллизации, что приводит к изменению ее микроструктуры. По мере нагревания его внутреннее напряжение и прочность устраняются, что делает его более пластичным. Холодная ковка не требует нагрева, благодаря чему металл сохраняет свою прочность и микроструктуру.
Характеристики холодной штамповки следующие:
Температура формовки:
Металлы формуются при комнатной температуре ниже их точки рекристаллизации, что позволяет снизить затраты и избежать расходов на печи.
Скорость:
Скорость варьируется от семи штук в минуту для машин с малым объемом до 400 штук в минуту для машин с большим объемом.
Оборудование:
Холодная ковка выполняется на машинах, предназначенных для придания формы металлу, включая сжатие, гибку, резку и волочение. Оборудование доступно в широком диапазоне цен в зависимости от количества техники и ее размера.
Расходы:
Экономия за счет материала и скорости. Экономия материала происходит за счет небольшого количества образующегося лома, которое составляет до 70%. Поскольку детали производятся очень быстро, стоимость единицы продукции значительно ниже.
Факторы окружающей среды:
Выбросы или загрязняющие вещества не производятся, как видно на этой машине от Stalcop ниже. Все самодостаточно и закрыто. Углерод и другие загрязняющие вещества исключаются, так как нет необходимости нагревать металл.
Результаты холодной ковки:
Как видно на диаграмме ниже, зернистая структура металлов перестраивается, чтобы следовать потоку конечной детали, устраняя усталость от пористости, увеличивая прочность на сдвиг и снижая любой риск нарушения целостности материала. Напрягая металл, он становится прочнее и эластичнее. Недостатком является то, что после холодной ковки металл теряет свою пластичность и становится более хрупким.
Масштабирование:
Перед ковкой металла важно удалить любые отложения, такие как ржавчина или коррозия, которые могут образоваться во время хранения. Если оставить ее неубранной, то износ детали будет таким же, как при горячей ковке.
Отделка:
Требуется крайне мало отделки. После обработки деталь готова к использованию или отправке.
Недостатки холодной ковки
Холодная ковка не идеальна. Как и у любого метода производства, у холодной ковки есть ограничения и ограничения, которые вам необходимо учитывать, прежде чем выбрать ее для своего следующего производственного проекта.
- Только простые формы и конструкции могут производиться в больших объемах. Уникальные, необычные или замысловатые узоры не могут быть выкованы методом холодной ковки. Уровни деформации и степень деформации ограничены, а холоднокованые металлы обладают меньшей пластичностью.
- Изменение зернистой структуры металла придает ему дополнительную прочность, но может вызвать остаточное напряжение.
- Некоторые методы холодной ковки требуют термической обработки для устранения возможных трещин или ползучести.
- Существует ограничение на типы металлов, которые можно подвергать холодной ковке. Не следует выбирать материалы с низкой пластичностью и чувствительностью к деформационному упрочнению, поскольку они теряют свою пластичность и разрушаются при растяжении. Можно использовать только металлы с твердостью HRC 44 по шкале Роквелла.
- Производственные процессы требуют большой силы для создания необходимой силы сжатия и давления. Хотя добавление гидравлики и пневматики уменьшило размер оборудования, оно не устранило количество энергии, потребляемой машинами.
- Инструменты, штампы и формы должны быть специально разработаны, а также достаточно прочными и прочными, чтобы выдерживать постоянные повторяющиеся нагрузки.
Глава пятая – Процессы холодной штамповки
Развитие различных технологий и достижений в области обработки металлов привело к появлению нескольких методов холодной формовки и штамповки металлов. Каждый из них предназначен для различных целей, но все они предназначены для эффективного и быстрого производства продукции без необходимости вторичной отделки.
Восемь наиболее распространенных процессов холодной ковки:
- Изгиб
- Холодная прокатка
- Закрытый штамп
- высокая проводимость
- Экструзия
- Открытая матрица
- Кольцевая ковка
- Обжимка
Как я расскажу в конце этой главы, существует больше процессов, чем только перечисленные. Приведенные ниже описания предоставляют вам исходные данные для первоначального понимания различных методов.
Кроме того, очень важным аспектом процесса холодной штамповки является тип используемой смазки. Двумя наиболее распространенными являются фосфат цинка или некоторая форма полимерного покрытия. Хотя холодная ковка производится при комнатной температуре, процесс гибки и формовки повышает температуру металлов. Смазка может предотвратить ошибки и предотвратить прилипание заготовки к штампу и продлить срок службы инструментов.
Производители смазочных материалов предлагают различные продукты для каждого типа процесса холодной штамповки. На фото изображены графитовые смазки, но доступны типы без графита, а также покрытия из алюмината кальция, фторида алюминия и фосфата.
Распространенные методы холодной ковки:
Изгиб –
Гибка выполняется с помощью пресса и матрицы, где заготовка прижимается к формовочному инструменту. Его также называют пирамидальной прокаткой, и иногда его используют для подготовки детали к другому процессу холодной ковки. Заготовка растягивается вдоль одной оси, образуя угол.
Холодная прокатка –
Прокатка — это процесс формования, при котором металл пропускается через пару вращающихся роликов для пластической деформации, вызванной сжимающей силой. Сжимающие напряжения создают трение между валками и поверхностью металлической заготовки. Он обычно используется для обработки стали.
Закрытый кубик –
При ковке в закрытых штампах заготовке придают форму последовательными механическими ударами после того, как она была помещена между двумя половинами штампа. Поскольку молот ударяет по заготовке несколько раз, некоторые производители называют ковку в закрытых штампах штамповкой. При ударе металл затекает в полости штампа, изменяя его форму в соответствии с формой штампа.
Рисунок -
Волочение - это протягивание заготовки через матрицу за счет силы растяжения, приложенной на выходе из матрицы. По мере протягивания заготовки происходит уменьшение площади поперечного сечения при увеличении ее длины. Формованные металлы имеют более строгие допуски на размеры, чем при прокатке.
Экструзия –
Заготовка или заготовка продавливается через матрицу под сжимающей силой, которая имеет профиль конечной детали. После того, как он проходит, он обрезается до необходимой длины, подготавливается к отправке или отправляется на дальнейшую обработку. Усилие, прикладываемое при холодной экструзии, может достигать 20 000 кН или 2007 тонн. Экструзия может производиться вперед, назад или в обоих направлениях.
Выдавливание вперед – металл проталкивается вперед через матрицу.
Обратная экструзия - металл входит в головку назад, образуя отверстия или чашки, делающие дно толще, чем его стороны.
Боковое выдавливание — усилие прикладывается сбоку, вбок, к направлению выдавливания, чтобы добавить к профилю второй элемент.
Открытая матрица:
Ковка в открытых штампах предполагает использование двух плоских штампов без предварительно вырезанного профиля. Заготовка постепенно формуется с использованием нескольких процессов, позволяющих производить широкий диапазон форм и размеров. Он в основном используется в конструкциях, включающих крупные металлические компоненты, требующие высочайшей структурной целостности. Деформация достигается изменением положения заготовки.
Выдавливание, также известное как проклейка, представляет собой форму обработки в открытой матрице, при которой усилие прикладывается на небольшом расстоянии, обеспечивая точные размеры.
Ковка колец –
При кольцевой ковке круглая заготовка пробивается посередине для получения формы пончика. Когда проколотая деталь вращается, она забивается и сжимается. В процессе производятся бесшовные кольца идеального диаметра и прочности.
Обжимка –
Обжатие, или радиальная ковка, представляет собой деформацию заготовки, при которой две детали подходят друг к другу. Он автоматизирован и очень надежен. Два типа обжатия трубчатые и радиальные. Обжим труб похож на экструзию, когда заготовка продавливается через матрицу. При радиальной обжимке молоток проталкивает заготовку через два или более штампа.
Когда вы начнете поиск производителя холодной штамповки, вы найдете больше методов, чем семь описанных здесь. Базовое понимание нескольких возможных методов поможет вам авторитетно и разумно говорить с продюсерами, а также понимать их жаргон.
Как и в случае с любым современным методом производства, вы обнаружите, что холодная ковка постоянно развивается по мере развития новых технологий и методов. Важным и растущим фактором является добавление автоматизации и робототехники, которые быстро меняют облик отрасли. Специалист по ковке может указать вам правильное направление, чтобы найти процесс, который наилучшим образом соответствует вашим потребностям.
Глава шестая – Оборудование и машины для холодной ковки
Оборудование и машины для холодной ковки бывают трех видов – гидравлические, пневматические и механические. В то время как некоторые поставщики специализируются только на одном типе, вы обнаружите, что у большинства есть несколько вариантов в зависимости от цены и типа операции. Технологии и автоматизация являются общими, как вы можете видеть на рисунке ниже, который представляет собой пресс для холодной штамповки с сервоприводом от Marvel Machinery. Визуализации дизайна деталей создаются с использованием инженерного программного обеспечения, такого как САПР.
Существуют требования, которым должны соответствовать станки, чтобы их можно было использовать для холодной ковки.
- Сила. Процессы холодной ковки зависят от огромной силы. Связанное с ним оборудование должно быть способно поглощать эту силу и рассеивать ее.
- Баланс. Машины должны быть статически и динамически сбалансированы по массе, чтобы уменьшить вибрации и повысить производительность.
- Стойкость во времени – независимо от метода холодной ковки каждый требует мощного повторяющегося усилия. Чтобы машина работала долго, она должна выдерживать эту силу.
- Несколько операций. Современные машины для холодной ковки или формовки, называемые жатками, выполняют от одной до нескольких операций в течение одного процесса. Это необходимо, поскольку существует ограниченное количество деформаций, которые можно выполнить за один ход.
Виды оборудования для холодной ковки:
Гидравлический штамповочный молот –
Гидравлический штамповочный молот предназначен для обеспечения максимальной силы при минимальных затратах. Он может производить широкий ассортимент оттисков из различных штампов. Он работает с использованием инженерных концепций гидравлики, где несжимаемая жидкость содержится в цилиндре. Когда жидкость сжимается поршнем, вал с присоединенной матрицей опускается на заготовку.
Винтовой пресс –
Винтовой пресс используется для больших деформаций из-за его низкой скорости прессования. Его можно использовать для штампов без облоя и поковок с длинным стержнем. Конфигурация винтового пресса позволяет использовать его для однощелевых штампов, включающих гибку и окончательную поковку. Электрический двигатель обеспечивает мощность для вращения винта, который прижимает матрицу к заготовке.
Высокоскоростной пресс C-образной рамы –
Конструкция C-образной рамы подходит для операций формовки, штамповки, гибки и многократного прессования. Они бывают одно- или двухкривошипными с усилием продавливания от 110 до 400 тонн и ходом скольжения от 110 до 280 мм. Они могут принимать штампы высотой от 435 до 600 мм и могут использоваться для производства мелких деталей.
Пневматический силовой пресс –
Пресс с пневматическим приводом может охватывать весь спектр функций штамповки. Они оснащены фрикционной муфтой и тормозом с пневматическим приводом. Мощность пресса создается воздушным компрессором, который прижимает кузнечный молот к заготовке за счет давления воздуха в цилиндре с поршнем.
Механический холодный пресс –
Из разновидностей станков для холодной ковки механический вариант становится наименее используемым, так как они должны быть очень большими, чтобы обеспечить необходимое усилие. У них есть маховик, который накапливает энергию от двигателя. Когда маховик приводится в действие, он приводит молоток или плунжер в матрицу. Он может обеспечить мощность в течение нескольких оборотов, но должен работать на холостом ходу, чтобы восстановить мощность своего двигателя, прежде чем он сможет продолжить свои циклы.
Из многих разновидностей оборудования для холодной ковки наиболее распространены гидравлические и пневматические типы, поскольку они занимают меньше места, могут создавать различное усилие и программируются. Когда вы изучаете свой выбор для производства, лучше всего знать типы оборудования, которое есть у производителя, поскольку современное оборудование с большей вероятностью будет производить детали более высокого качества.
Глава седьмая. Типы кованых металлов.
Холодная ковка предлагает широкий выбор металла для проекта. Различные разновидности включают твердые металлы, такие как углеродистая сталь, легированная сталь и нержавеющая сталь. Алюминий, латунь, медь, кремний и магний — это мягкие металлы, которые можно использовать. Единственное требование к любому металлу — твердость 44 HRC или ниже по шкале Роквелла.
Медь -
Медь является отличным металлом для холодной ковки, так как она очень ковкая и ковкая. Его можно формовать, сгибать или тянуть с небольшим усилием, и он производит детали, устойчивые к коррозии и ржавчине.
Алюминий –
Алюминий — цветной металл, очень легкий, с низкой плотностью. Он имеет температуру плавления 1220 ° F и пластичен, а также устойчив к ржавчине и коррозии.
Углеродистая сталь -
Углеродистая сталь представляет собой сплав железа и углерода. Различные сорта зависят от количества углерода, смешанного с железом. Обладает исключительной прочностью и пластичностью.
Нержавеющая сталь -
Нержавеющая сталь стала одним из наиболее часто используемых металлов благодаря своей коррозионной стойкости, внешнему виду и прочности. Хотя термин «нержавеющая сталь» обычно используется для описания любой стали, имеющей свои характеристики, нержавеющая сталь бывает разных марок в зависимости от содержания в ней сплава.
Стали, применяемые для холодной ковки
Низкоуглеродистые стали с содержанием углерода от 0,1% до 0,25%. Холодная ковка улучшает деформационное упрочнение стали, устраняя необходимость в аустенитизации, закалке или отжиге.
Металлы, подходящие для холодной ковки
Подходящий сплав | Холодная формуемость Характеристика |
---|---|
Медь | Превосходно |
Золото, серебро и большинство их сплавов | Превосходно |
Латунь-Картридж Латунь | Хороший |
Платина, палладий, тантал и их сплавы. | Большинство из них поддаются холодной штамповке. |
Титан и его сплавы | Чистый Ti и сплавы с высокой пластичностью да, но сплавы типа 6-4 пригодны только для горячей головки. |
никель и его сплавы | Чистый Ni да, сплавы с удлинением при комнатной температуре 20% и более, да. |
Железо и стали | Чистое железо, да. Стали, зависит от стали. Многие из них поддаются холодной штамповке. |
На что обращать внимание при выборе металла:
Самое логичное и важное, что вы можете сделать, выбирая металл для проекта, — это провести исследование. Каждый тип металла по-разному реагирует на пластификацию и деформацию. Выбранный вами металл должен соответствовать его конечному назначению и требуемой прочности. Если вы проконсультируетесь со специалистом по ковке, вы можете получить ценную информацию, которая поможет вам сделать правильный выбор.
Глава восьмая – Применение холодной штамповки
Холодная ковка позволяет получать формы любых размеров с высокой точностью размеров и структурной точностью. Экономическая эффективность и скорость холодной штамповки сделали ее самой популярной альтернативой производства.
Холодная ковка отвечает требованиям современной промышленности, поскольку:
- Максимальное использование сырья: ключевой инвестицией для любой операции является сырье. Процесс холодной ковки имеет очень мало отходов. Вспышка и отделка могут быть возвращены в производственный процесс.
- Снижает затраты: поскольку детали производятся быстро, стоимость единицы продукции очень низкая, что делает конечные продукты более прибыльными и менее затратными в производстве.
- Производит детали высокого качества: холодная ковка повышает прочность и долговечность деталей и изделий, гарантируя, что они прослужат дольше. Структура и характеристики фасонного изделия не изменяются, что обеспечивает превосходную точность размеров.
Области применения, в которых используются холоднокованые детали:
Автомобили –
Высокая прочность, надежность, качество и доступная цена холодной штамповки сделали ее очень привлекательной для автомобилестроения. Холоднокованые детали устанавливаются в местах высоких нагрузок из-за их отличной ударопрочности. Такие компоненты, как трансмиссия, приводные валы, стойки или амортизаторы, изготовлены методом холодной ковки. На схеме ниже показаны некоторые детали ходовой части автомобиля, изготовленные методом холодной ковки.
Ручной инструмент и оборудование –
Соединители, такие как гвозди, болты, заклепки и гайки, уже много лет производятся методом холодной ковки. Низкие допуски и превосходная точность размеров — вот почему производители ручных инструментов предпочитают холодную ковку другим методам, таким как механическая обработка.
Военный -
Военные предъявляют очень строгие требования к военной технике и выбирают холодную ковку для изготовления гильз, пуль и другой военной техники. Детали обладают высокой надежностью и работоспособностью в условиях кризиса. Низкие допуски и прочность деталей делают их идеальными для боевого оружия.
Производство шестерен –
Холодная ковка используется для производства зубчатых колес, потому что она устраняет необходимость резки при формировании зубчатого колеса. Зубчатые колеса могут изготавливаться из заготовок размером менее 50 мм или формоваться с использованием спиральной проволоки. Некоторый отжиг может быть необходим для снятия остаточного напряжения и деформационного упрочнения. Важным преимуществом холоднокованых шестерен является то, насколько плавно и бесшумно они входят в зацепление.
Вывод
- Холодная ковка позволяет получать металлы с низкими допусками и высокой точностью размеров при очень низкой стоимости и больших объемах.
- Холодная ковка быстро и быстро создает готовые детали, которые сразу же доступны и комплектны.
- Производители предложат вам широкий выбор процессов для производства именно той детали, которая вам нужна, на самом современном и технически совершенном оборудовании.
- У вас будет широкий выбор металлов для завершения вашего проекта от закаленной стали и нержавеющей стали до меди и алюминия.
- Вы обнаружите очень мало ограничений на количество продуктов, которые вы можете производить, от устойчивых к нагрузкам компонентов для вашего автомобиля до заклепок, шестерен и рабочих инструментов.
- Если вы сравните холодную и горячую ковку, вы обнаружите, что холодная ковка занимает меньше времени и позволяет производить более прочные и долговечные детали и изделия.