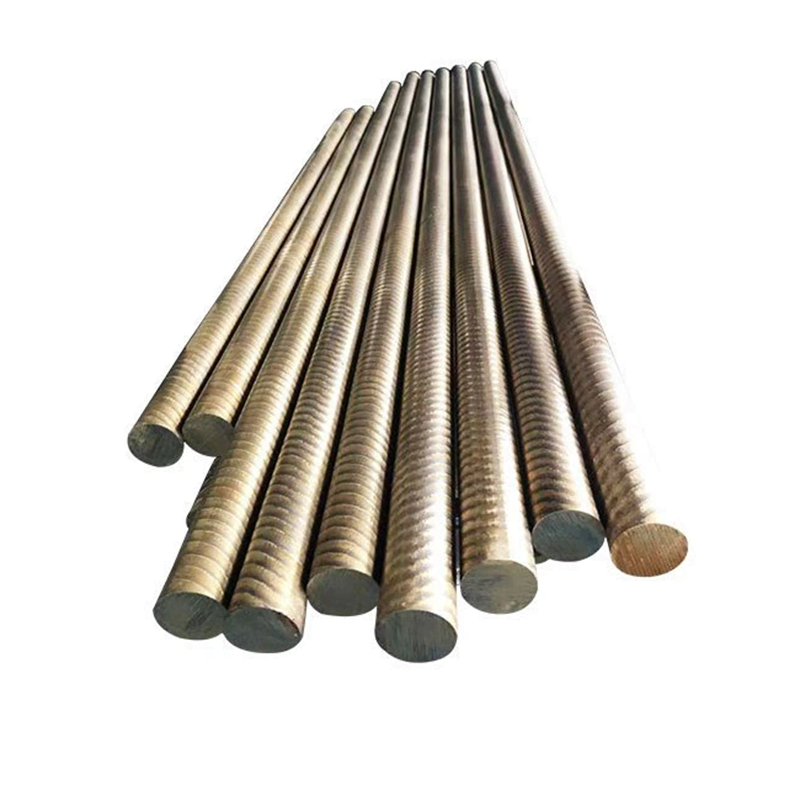
Введение:
C63000 aluminum bronze is a high-strength copper alloy that has gained significant attention in various industrial applications due to its exceptional combination of mechanical properties and corrosion resistance. This alloy, belonging to the family of aluminum bronzes, offers a unique blend of characteristics that make it particularly suitable for use in demanding environments, such as marine applications, aerospace components, and heavy machinery. The purpose of this article is to provide a comprehensive analysis of the chemical composition of C63000 aluminum bronze and explore how its constituent elements contribute to its remarkable mechanical properties.
Химический состав:
The chemical composition of C63000 aluminum bronze is carefully balanced to achieve optimal performance characteristics. The primary elements in this alloy include:
1. Copper (Cu): 79.0-81.5%
2. Aluminum (Al): 9.0-11.0%
3. Iron (Fe): 3.0-5.0%
4. Nickel (Ni): 4.0-5.5%
5. Manganese (Mn): 1.5% max
Copper, as the base metal, provides excellent electrical and thermal conductivity, as well as good corrosion resistance. The addition of aluminum to copper forms the foundation of aluminum bronze alloys, contributing to increased strength and improved wear resistance.
Iron is added to refine the grain structure and enhance the overall strength of the alloy. It also helps in improving the alloy’s resistance to corrosion, particularly in seawater environments.
Nickel plays a crucial role in improving the alloy’s strength and toughness. It also contributes to better corrosion resistance, especially in reducing environments.
Manganese, although present in smaller quantities, helps in deoxidation during the melting process and contributes to improved mechanical properties.
The precise control of these elemental percentages is crucial in achieving the desired properties of C63000 aluminum bronze. Even small variations in composition can significantly affect the alloy’s performance characteristics.
Механические свойства:
The unique chemical composition of C63000 aluminum bronze translates into a set of impressive mechanical properties that make it suitable for a wide range of applications. Some of the key mechanical properties of this alloy include:
1. Tensile Strength: C63000 exhibits high tensile strength, typically ranging from 110,000 to 125,000 psi (758 to 862 MPa). This high strength makes it suitable for applications requiring resistance to heavy loads and stresses.
2. Yield Strength: The yield strength of C63000 is generally between 65,000 to 75,000 psi (448 to 517 MPa), indicating good resistance to plastic deformation under load.
3. Elongation: With an elongation of 6-20% (depending on temper), C63000 offers a good balance between strength and ductility, allowing for some degree of plastic deformation before failure.
4. Hardness: The Brinell hardness of C63000 typically ranges from 240 to 280, providing excellent wear resistance in many applications.
5. Fatigue Strength: C63000 demonstrates good fatigue resistance, making it suitable for components subject to cyclic loading.
6. Impact Strength: The alloy exhibits good impact strength, which is crucial for applications involving sudden loads or impacts.
These mechanical properties are a direct result of the alloy’s chemical composition and microstructure. The aluminum content contributes to the formation of intermetallic compounds, which strengthen the alloy. The iron and nickel additions further enhance the strength and toughness through solid solution strengthening and precipitation hardening mechanisms.
Microstructure and Heat Treatment:
The microstructure of C63000 aluminum bronze plays a crucial role in determining its mechanical properties. In its as-cast condition, the alloy typically consists of alpha (α) phase dendrites surrounded by a beta (β) phase. The α phase is rich in copper, while the β phase contains higher concentrations of aluminum and other alloying elements.
Heat treatment can significantly alter the microstructure and, consequently, the mechanical properties of C63000. Common heat treatments include:
1. Solution Annealing: Heating the alloy to temperatures around 900-950°C (1652-1742°F) followed by rapid quenching. This process dissolves the β phase, resulting in a supersaturated α phase.
2. Aging: Subsequent aging at lower temperatures (around 400-500°C or 752-932°F) allows for controlled precipitation of intermetallic compounds, further enhancing strength and hardness.
The heat treatment process can be tailored to achieve specific combinations of strength, ductility, and toughness, depending on the intended application.
Устойчивость к коррозии:
One of the standout features of C63000 aluminum bronze is its excellent corrosion resistance, particularly in marine environments. This property is attributed to the formation of a thin, adherent aluminum oxide film on the surface of the alloy when exposed to oxygen. This protective layer acts as a barrier against further corrosion.
The presence of nickel in the alloy further enhances its corrosion resistance, especially in reducing environments. C63000 exhibits superior resistance to dezincification and stress corrosion cracking compared to many other copper alloys.
Приложения:
The combination of high strength, excellent corrosion resistance, and good wear properties makes C63000 aluminum bronze suitable for a wide range of applications, including:
1. Marine Components: Propellers, pump impellers, valve stems, and marine hardware.
2. Aerospace: Landing gear components, bushings, and bearings.
3. Oil and Gas Industry: Valve bodies, pump components, and offshore platform equipment.
4. Heavy Machinery: Gears, bearings, and wear plates in mining and construction equipment.
5. Chemical Processing: Pump components and valves in corrosive environments.
Challenges and Limitations:
Despite its many advantages, C63000 aluminum bronze does have some limitations:
1. Cost: The alloy is relatively expensive due to its high nickel content.
2. Machinability: While machinable, C63000 can be more challenging to work with compared to some other copper alloys.
3. Welding: Special techniques and precautions are required when welding C63000 to maintain its properties.
Future Developments:
Ongoing research in the field of aluminum bronzes is focused on further improving the properties of alloys like C63000. Areas of interest include:
1. Developing more cost-effective manufacturing processes.
2. Exploring the potential of additive manufacturing techniques for producing complex C63000 components.
3. Investigating the effects of nano-scale additions to further enhance mechanical properties and corrosion resistance.
4. Studying the behavior of C63000 in extreme environments, such as cryogenic temperatures or high-radiation areas.
Заключение:
C63000 aluminum bronze stands out as a high-performance alloy that offers an exceptional combination of strength, corrosion resistance, and wear properties. Its carefully balanced chemical composition, consisting primarily of copper, aluminum, iron, and nickel, results in a material that excels in demanding applications across various industries.
The mechanical properties of C63000, including its high tensile strength, good ductility, and excellent wear resistance, make it a versatile material for components that require both strength and durability. Its superior corrosion resistance, particularly in marine environments, further extends its applicability in harsh conditions.
While challenges such as cost and manufacturing complexities exist, the unique properties of C63000 aluminum bronze continue to make it an attractive choice for engineers and designers seeking high-performance materials. As research in materials science progresses, it is likely that we will see further improvements and innovations in aluminum bronze alloys, potentially expanding their applications and enhancing their already impressive capabilities.
Understanding the intricate relationship between the chemical composition and mechanical properties of C63000 aluminum bronze is crucial for optimizing its use in current applications and exploring new possibilities. As industries continue to push the boundaries of material performance, alloys like C63000 will undoubtedly play a vital role in shaping the future of engineering and manufacturing.