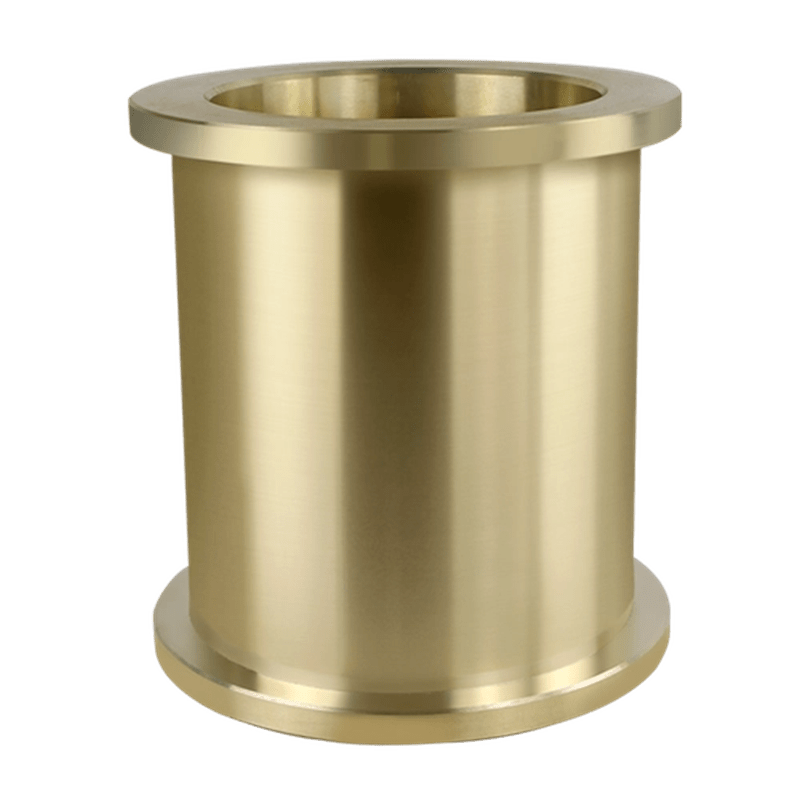
In the realm of heavy machinery, the selection of appropriate materials for gears is crucial for ensuring optimal performance, longevity, and reliability. Aluminum bronze has emerged as a popular choice for gear applications in heavy machinery due to its excellent wear resistance and other beneficial properties. This article delves into the wear resistance characteristics of aluminum bronze gears and their performance in heavy machinery applications.
Introduction to Aluminum Bronze Gears
Aluminum bronze is a family of copper-based alloys containing aluminum as the primary alloying element, often with additions of iron, nickel, and manganese. These alloys are known for their:
- Высокая прочность
- Отличная коррозионная стойкость
- Superior wear resistance
- Good friction properties
- Теплопроводность
These properties make aluminum bronze an attractive option for gears in heavy machinery, where components are subjected to high loads, harsh environments, and continuous operation.
Wear Resistance of Aluminum Bronze Gears
Wear resistance is a critical factor in gear performance, especially in heavy machinery where gear failure can lead to costly downtime and repairs. Aluminum bronze gears exhibit excellent wear resistance due to several factors:
1. Hardness and Strength
Aluminum bronze alloys used in gears typically have a Brinell hardness ranging from 150 to 280 HB, depending on the specific composition and heat treatment. This hardness, combined with high strength, contributes significantly to wear resistance.
2. Work Hardening
Aluminum bronze has the ability to work harden under load. This means that the surface of the gear teeth becomes harder with use, further enhancing wear resistance.
3. Lubrication Properties
Aluminum bronze has good oil retention properties, which helps maintain a lubricating film between mating gear surfaces, reducing friction and wear.
4. Corrosion Resistance
The excellent corrosion resistance of aluminum bronze helps prevent surface degradation that could lead to accelerated wear.
Comparative Wear Resistance Analysis
To better understand the wear resistance of aluminum bronze gears, let’s compare it with other common gear materials:
Материал | Relative Wear Resistance | Твердость (HB) | Устойчивость к коррозии |
---|---|---|---|
Алюминиевая бронза | Превосходно | 150-280 | Превосходно |
Steel (4140) | Хороший | 190-330 | Бедных |
Нержавеющая сталь | Хороший | 160-190 | Очень хороший |
Bronze (SAE 660) | Умеренный | 60-90 | Хороший |
Cast Iron | Хороший | 150-300 | Бедных |
As shown in the table, aluminum bronze offers a compelling combination of wear resistance, hardness, and corrosion resistance, making it well-suited for heavy machinery applications.
Factors Affecting Wear Resistance in Heavy Machinery
Several factors influence the wear resistance of aluminum bronze gears in heavy machinery:
- Load: Higher loads can accelerate wear, but aluminum bronze’s work hardening properties help mitigate this effect.
- Скорость: Gear speed affects the lubrication regime and heat generation, impacting wear rates.
- Lubrication: Proper lubrication is crucial for maximizing wear resistance.
- Условия окружающей среды: Exposure to corrosive environments or abrasive particles can affect wear rates.
- Чистота поверхности: A smoother surface finish can improve wear resistance by reducing friction and stress concentrations.
Case Studies: Aluminum Bronze Gears in Heavy Machinery
To illustrate the performance of aluminum bronze gears in real-world applications, consider the following case studies:
1. Mining Equipment
In a large open-pit mine, aluminum bronze gears were installed in a heavy-duty conveyor system. After 18 months of continuous operation, the gears showed minimal wear compared to the previously used steel gears, which typically required replacement every 12 months.
2. Marine Propulsion Systems
A shipyard replaced steel gears with aluminum bronze gears in the reduction gearbox of a large cargo ship. Over a 5-year period, the aluminum bronze gears exhibited 40% less wear than the steel gears, resulting in reduced maintenance costs and improved reliability.
Optimizing Aluminum Bronze Gear Performance
To maximize the wear resistance and overall performance of aluminum bronze gears in heavy machinery:
- Proper Material Selection: Choose the appropriate aluminum bronze alloy based on the specific application requirements.
- Термическая обработка: Optimize heat treatment processes to achieve the desired hardness and microstructure.
- Surface Engineering: Consider surface treatments or coatings to further enhance wear resistance.
- Lubrication Management: Implement a robust lubrication system and maintenance schedule.
- Регулярный осмотр: Conduct periodic inspections to monitor wear and address issues proactively.
Вывод
Aluminum bronze gears offer exceptional wear resistance in heavy machinery applications, outperforming many traditional gear materials. Their unique combination of hardness, work hardening ability, and corrosion resistance makes them an excellent choice for demanding environments.
While the initial cost of aluminum bronze gears may be higher than some alternatives, their superior wear resistance often results in lower long-term costs due to reduced maintenance and replacement frequency. As heavy machinery continues to evolve, requiring ever-greater performance and reliability, aluminum bronze gears are likely to play an increasingly important role in ensuring efficient and durable operation.
When considering gear materials for heavy machinery, engineers and designers should carefully evaluate the specific application requirements and consider aluminum bronze as a high-performance option. Its proven wear resistance and other beneficial properties make it a valuable material in the pursuit of improved machinery performance and longevity.