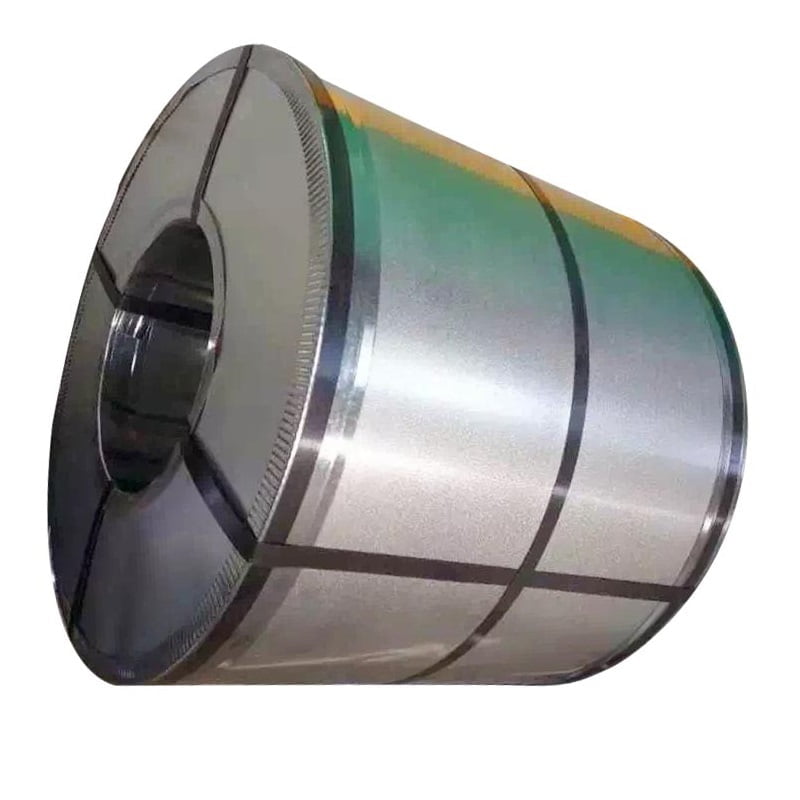
Introdução
DX51D é uma designação amplamente reconhecida para aço galvanizado por imersão a quente feito de acordo com a norma europeia EN 10346. Este tipo de aço é preferido em vários setores por seu notável equilíbrio entre durabilidade, resistência à corrosão e conformabilidade. Ele desempenha um papel crucial em inúmeras aplicações, especialmente nos setores de construção, automotivo e manufatureiro. Este documento fornecerá uma visão geral abrangente do DX51D, suas propriedades, aplicações, graus equivalentes e vantagens e desvantagens, estendendo-se a insights abrangentes que abrangerão aproximadamente 2.000 palavras.
O que é DX51D?
O aço DX51D é caracterizado principalmente por seu processo de galvanização por imersão a quente. Em essência, a galvanização por imersão a quente envolve a imersão do aço em zinco fundido, criando uma camada protetora espessa que protege contra a corrosão. Esta designação enquadra-se na norma europeia para chapas e tiras de aço revestidas para conformação a frio.
Principais características do DX51D
- Resistência à corrosão: Um dos atributos mais significativos do DX51D é a sua capacidade de resistir à corrosão. O revestimento de zinco serve como barreira, evitando que a umidade e fatores ambientais comprometam a integridade do aço subjacente.
- Propriedades mecânicas: DX51D normalmente tem um limite de escoamento mínimo de cerca de 250 MPa, com uma resistência à tração variando de 330 MPa a 450 MPa, dependendo da espessura específica e do peso do revestimento.
- Formabilidade: O DX51D apresenta excelente conformabilidade, tornando-o adequado para diversas aplicações que exigem dobra, estampagem ou outros processos de usinagem de metal.
- Acabamento de superfície: Este tipo de aço é conhecido por seu acabamento superficial liso, geralmente preferido em aplicações onde a estética é importante.
Composição química
A composição química do DX51D consiste principalmente de ferro, complementado por zinco e outros elementos de liga. Embora a composição exata possa variar dependendo dos processos de fabricação específicos, os valores típicos incluem:
Elemento | Porcentagem (%) |
---|---|
Ferro (Fe) | Equilíbrio |
Zinco (Zn) | < 0.21% |
Carbono (C) | < 0.12% |
Manganês (Mn) | < 0.60% |
Fósforo (P) | < 0.04% |
Enxofre (S) | < 0.05% |
Manter a composição química correta é vital para garantir que o DX51D atenda às especificações exigidas de resistência, resistência à corrosão e conformabilidade.
Aplicações do Aço DX51D
O aço DX51D é empregado em vários setores e aplicações devido às suas propriedades favoráveis. Aqui estão algumas aplicações comuns:
1. Construção
O DX51D é amplamente utilizado na indústria da construção. Sua resistência à corrosão o torna ideal para:
- Painéis de cobertura: Materiais de cobertura duráveis que podem suportar os elementos.
- Revestimento de parede: Revestimentos estéticos e protetores de paredes para edifícios.
- Quadros Estruturais: Usado em estruturas de construção onde a resistência e a longevidade são críticas.
2. Indústria Automotiva
O setor automotivo depende do aço DX51D para diversos componentes devido à sua resistência e leveza. As aplicações incluem:
- Painéis Corporais: A carroceria externa dos veículos geralmente usa DX51D por sua resistência à corrosão e resistência ao impacto.
- Componentes do chassi: A estrutura dos veículos se beneficia da relação resistência/peso oferecida por este tipo de aço.
- Peças internas: Certos componentes internos que exigem durabilidade e apelo estético podem ser fabricados a partir do DX51D.
3. Fabricação
Na fabricação, o DX51D encontra lugar em diversos produtos, como:
- Eletrodomésticos: Componentes de geladeiras, máquinas de lavar e outros eletrodomésticos.
- Mobília: As estruturas de mesas, cadeiras e estantes podem utilizar o DX51D devido à sua resistência e durabilidade.
- Equipamentos Industriais: Peças de máquinas e equipamentos em ambientes agressivos onde a resistência à corrosão é essencial.
Classes equivalentes de DX51D
Compreender os equivalentes ao DX51D ajuda fabricantes e engenheiros a identificar materiais alternativos para aplicações específicas. Abaixo estão notas conhecidas equivalentes a Aço DX51D:
Padrão | Nota equivalente | Descrição |
---|---|---|
EN 10346 | DX51D | Aço galvanizado por imersão a quente adaptado para conformação a frio. |
ASTM A653 | G90 | Equivalente americano com gramatura mínima de revestimento de 90 g/m². |
JIS G3302 | SGCC | Padrão japonês para galvanização com aplicações gerais. |
ISO 3574 | SPCC | Chapa de aço carbono laminada a frio para processamento posterior. |
EN 10327 | S250GD | Aço galvanizado por imersão a quente para aplicações de conformação a frio. |
Identificar os graus equivalentes apropriados é crucial para garantir as propriedades corretas do material e o desempenho em aplicações específicas.
Vantagens do aço DX51D
A escolha do aço DX51D beneficia as indústrias de diversas maneiras:
1. Excelente resistência à corrosão
A galvanização do DX51D proporciona uma defesa robusta contra ferrugem e deterioração. Esta característica é particularmente vital em ambientes externos ou locais expostos à umidade ou a produtos químicos.
2. Alta relação resistência/peso
Com um limite de escoamento mínimo de aproximadamente 250 MPa, o DX51D oferece resistência significativa sem peso excessivo, tornando-o adequado para aplicações que exigem resistência e leveza.
3. Custo-benefício
Embora o custo inicial do DX51D possa ser mais elevado do que as alternativas não galvanizadas, a sua longevidade e os requisitos de manutenção reduzidos conduzem frequentemente a custos globais mais baixos a longo prazo.
4. Apelo Estético
O acabamento superficial liso e brilhante do aço DX51D também o torna visualmente atraente, tornando-o a escolha preferida para aplicações onde a aparência é importante.
5. Versatilidade nas aplicações
O DX51D pode ser usado em vários processos, como estampagem, dobra e perfilagem, tornando-o uma escolha versátil em vários setores.
Desvantagens do aço DX51D
Embora o DX51D tenha muitas vantagens, também existem algumas desvantagens a serem consideradas:
Desvantagem | Descrição |
---|---|
Custo Inicial | Custos iniciais mais elevados em comparação com o aço não galvanizado. |
Desempenho limitado em altas temperaturas | Pode perder algumas de suas propriedades em temperaturas extremamente altas. |
Desafios de soldagem | O revestimento de zinco pode apresentar dificuldades na soldagem e exigir técnicas específicas para evitar a toxicidade dos vapores de zinco. |
Conformidade com Padrões | A conformidade com padrões específicos pode variar entre os fabricantes, por isso é crucial verificar as propriedades dos materiais. |
Exemplo de desvantagens que afetam os aplicativos
- Limitações de soldagem: Ao fabricar componentes que requerem soldagem extensa, deve-se tomar cuidado para remover ou manusear o revestimento de zinco, que pode produzir vapores nocivos se não for manuseado adequadamente.
- Implicações de custos: Em projetos onde as restrições orçamentárias são rigorosas, o custo inicial mais elevado do uso do DX51D pode exigir uma justificativa cuidadosa com base na longevidade e durabilidade esperadas.
Tendências e desenvolvimentos futuros
À medida que as indústrias continuam a evoluir, também evoluem os materiais utilizados na construção, na indústria automóvel e na indústria transformadora. Várias tendências que impactam o DX51D podem ser observadas:
1. Demanda crescente por materiais sustentáveis
À medida que o mundo se concentra mais em práticas sustentáveis, aumenta a necessidade de materiais recicláveis e com menor impacto ambiental. O DX51D, com seu revestimento de zinco, pode ser reciclado e utilizado em outros produtos.
2. Desenvolvimento de Revestimentos Avançados
A pesquisa contínua em revestimentos avançados pode aprimorar as propriedades do DX51D, como melhorar seu desempenho em ambientes de alta temperatura ou aumentar ainda mais a resistência à corrosão por meio de experiências com diferentes elementos de liga.
3. Tecnologias de aço inteligentes
A incorporação da tecnologia na produção e nas aplicações do aço pode levar ao desenvolvimento de materiais inteligentes que possam monitorar o seu próprio estado estrutural, ajudando a prever falhas antes que elas ocorram.
4. Expansão nas áreas de aplicação
À medida que o DX51D continua a provar o seu valor nas aplicações atuais, poderão surgir novas possibilidades de utilização, especialmente em setores de energia renovável como a eólica e a solar, onde materiais duráveis e resistentes à corrosão são uma necessidade.
5. Personalização de Materiais
A tendência para materiais customizados que atendam a aplicações específicas exige flexibilidade nos processos de produção, incentivando os fabricantes a explorar novas formas de atender às necessidades dos clientes em relação à espessura, propriedades mecânicas e pesos do revestimento.
Conclusão
O aço DX51D é um material crucial que exemplifica o equilíbrio entre durabilidade, resistência à corrosão e conformabilidade. Seu amplo uso em diversas indústrias sem sacrificar o desempenho demonstra a importância de selecionar o material certo para aplicações específicas. Embora os custos iniciais possam ser superiores aos das alternativas, as vantagens a longo prazo justificam frequentemente o investimento.
A incorporação de uma compreensão abrangente de classes, aplicações, vantagens, desvantagens e tendências futuras equivalentes permite que engenheiros e fabricantes tomem decisões informadas. Seja na construção, na fabricação automotiva ou em vários tipos de aplicações industriais, o DX51D e suas propriedades continuarão a desempenhar um papel fundamental no avanço da infraestrutura moderna e dos processos de fabricação.
À medida que olhamos para o futuro, abraçar inovações e sustentabilidade irá melhorar o desempenho do DX51D, ao mesmo tempo que aborda as exigências e desafios de novos cenários industriais. Isto solidificará ainda mais a posição do DX51D como uma escolha confiável em engenharia de materiais.