2507 Stainless steel
2507 is a ferritic – austenitic (duplex) stainless steel with excellent pitting, crevice and uniform corrosion resistance.
Alias: Super duplex stainless steel
Ingredients: 25Cr-7Ni-4Mo-0.27N
EURONORM: 1.4410 – X2 Cr Ni MoN 25.7.4
2507 is a ferritic — austenitic (duplex) stainless steel that combines many of the most beneficial properties of both ferritic and austenitic steels. Due to its high chromium and molybdenum content, the steel offers excellent resistance to spot, gap and uniform corrosion. The biphase microstructure ensures that the steel has high stress corrosion cracking resistance and high mechanical strength.
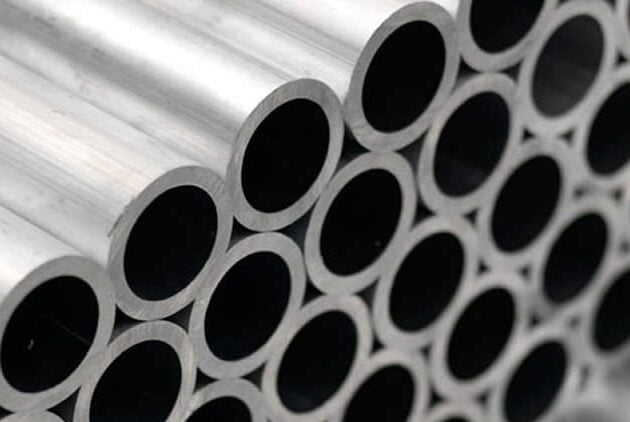
Duplex 2507 (UNS S32750) is a super duplex stainless steel with 25% chromium, 4% molybdenum, and 7% nickel designed for demanding applications which require exceptional strength and corrosion resistance, such as chemical process, petrochemical, and seawater equipment.
Duplex Stainless Steels, also referred to as austeniticferritic stainless steels, are a family of grades having around equal proportions of austenite and ferrite.
These steels have a duplex microstructure which contributes to their high strength and high resistance to stress corrosion cracking.
Duplex steels offer high resistance to uniform and local corrosion because of their high content of nitrogen, chromium and molybdenum. Duplex stainless steels have good weldability.
There are three groups of duplex stainless steels that include the following:
- Lean Duplex
- Standard Duplex
- Super Duplex.
Standards
- ASTM/ASME A240 – Specification for Chromium and Chromium-Nickel Stainless Steel Plate, Sheet, and Strip for Pressure Vessels and for General Applications
- EURONORM 1.4410 – X2 Cr Ni MoN 25.7.4
- AFNOR Z3 CN 25.06 Az
S32750 or Duplex 2507
Duplex 2507 is a super duplex stainless steel developed for applications that demand high strength and corrosion resistance. Alloy 2507 has 25% chromium, 4% molybdenum, and 7% nickel.
This high molybdenum, chromium and nitrogen content causes high resistance to chloride pitting and crevice corrosion attack and the duplex structure provides 2507 with exceptional resistance to chloride stress corrosion cracking.
Using Duplex 2507 must be restricted to applications below 600° F (316° C). Extended elevated temperature exposure can reduce both the toughness and corrosion resistance of alloy 2507.
Duplex 2507 has good mechanical properties. Often a light gauge of 2507 material can be used to achieve the same design strength of a thicker nickel alloy. The resulting weight savings can considerably reduce the overall cost of fabrication.
Properties of Super Duplex Steel 2507 or S32750
- High resistance to chloride stress corrosion cracking.
- High Strength.
- Combination of properties given by austenitic and ferritic structure.
- Good weldability and workability.
- Superior resistance to chloride pitting and crevice corrosion.
- Good general corrosion resistance.
- Suggested for applications up to 600° F.Stainless Steel S32760
Applications of S32750 Super Duplex Stainless Steel
Alloy 2507 (UNS S32750) is a super duplex stainless steel with 25% chromium, 4% molybdenum, and 7% nickel designed for demanding applications which require exceptional strength and corrosion resistance, such as chemical process, petrochemical, and seawater equipment. The steel has excellent resistance to chloride stress corrosion cracking, high thermal conductivity, and a low coefficient of thermal expansion. The high chromium, molybdenum, and nitrogen levels provide excellent resistance to pitting, crevice, and general corrosion.
The applications of S32750 super duplex stainless steel are:
- Desalination Equipment.
- Chemical process pressure vessels, piping and heat exchangers.
- Marine Applications.
- Flue Gas Scrubbing Equipment.
- Pulp & Paper Mill Equipment.
- Offshore Oil production/technology.
- Oil and gas industry equipment.
Chemical Analysis
Typical Values (Weight %)
Carbon | Chromium | Nickel | Molybdenum | Nitrogen | Others |
---|---|---|---|---|---|
0.020 | 25 | 7 | 4.0 | 0.27 | S=0.001 |
PREN = [Cr%] = 3.3 [Mo%] = 16 [N %] ≥ 40 |
Mechanical Properties
Mechanical and Physical Properties
2507 combines high tensile and impact strength with a low coefficient of thermal expansion and high thermal conductivity. These properties are suitable for many structural and mechanical components. The low, ambient, and elevated temperature mechanical properties of 2507 sheet and plate are shown below. All of the test data shown are for samples in the annealed and quenched condition.
2507 is not recommended for applications which require long exposures to temperatures in excess of 570°F because of the increased risk of a reduction in toughness. The data listed here are typical for wrought products and should not be regarded as a maximum or minimum value unless specifically stated.
Properties
0.2% Offset Yield Strength, ksi 80 min.
Ultimate Tensile Strength, ksi 116 min.
1% Offset Yield Strength, ksi 91 min.
Elongation in 2 inches, % 15 min.
Hardness, Rockwell C 32 max
Impact Energy, ft-lbs 74 min.
Low Temperature Impact Properties
Temperature °F | RT | 32 | -4 | -40 |
---|---|---|---|---|
Ft-lbs | 162 | 162 | 155 | 140 |
Temperature °F | -76 | -112 | -148 | -320 |
Ft-lbs | 110 | 44 | 30 | 7 |
Elevated Temperature Tensile Properties
Temperature °F | 68 | 212 | 302 | 392 | 482 |
---|---|---|---|---|---|
0.2% Offset Yield Strength, ksi | 80 | 65 | 61 | 58 | 55 |
Ultimate Tensile Strength, ksi | 116 | 101 | 98 | 95 | 94 |
Values obtained for hot rolled plates (th ≤ 2″). Alloy 2304 must not be used for a long time at temperatures higher than 300°C (572°F), where precipitation hardening phenomenon occurs.
Physical Properties
Density : 7,800 kg/m3 – 0.28 lb/in3
Interval Temper °C | Thermal expansion ax10M-bK-1 | °C | Resistivity (μ_ cm) | Thermal conductivity (W.m-1.K-1) | Specific heat (J.kg-1.K-1 | Young modulus E (GPa) | Shear modulus G (GPa) |
---|---|---|---|---|---|---|---|
20-100 | 13 | 20 | 80 | 17 | 450 | 200 | 75 |
20-100 | 13 | 100 | 92 | 18 | 500 | 190 | 73 |
20-200 | 13.5 | 200 | 100 | 19 | 530 | 180 | 70 |
20-300 | 14 | 300 | 105 | 20 | 560 | 170 | 67 |
Processing
Hot Forming
2507 should be hot worked between 1875 F and 2250 F. This should be followed by a solution anneal at 1925F minimum and a rapid air or water quench.
Cold Forming
Most of the common stainless steel forming methods can be used for cold working 2507. The alloy has a higher yield strength and lower ductility than the austenitic steels so fabricators may find that higher forming forces, increased radius of bending, and increased allowance for springback are necessary. Deep drawing, stretch forming, and similar processes are more difficult to perform on 2507 than on an austenitic stainless steel. When forming requires more than 10% cold deformation, a solution anneal and quench are recommended.
Heat Treatment
2507 should be solution annealed and quenched after either hot or cold forming. Solution annealing should be done at a minimum of 1925 F. Annealing should be followed immediately by a rapid air or water quench. To obtain maximum corrosion resistance, heat treated products should be pickled and rinsed.