1.2344 Tool Steel Description
Lion Metal is 1.2344 Steel stockholders and suppliers from China. What’ more, We Supply in Tool steel round bar, flat bar, and plate more 26 years experience. 1.2344 Tool Steel/H13 steel is chromium hot work tool steels which are widely used in hot and cold work tooling applications.
Din 1.2344 Steel is a high quality Hot work tool steel, and it belongs to the high quality high carbon alloy tool steel. And Oil Quench & Temper Hardness is 28-34 HRC. And DIN 1.2344 steel Annealing delivery hardness less than 250HB.
DIN 1.2344 tool steel/AISI H13 steel is characterized by:
- Good resistance to abrasion at both low and high temperatures
- High toughness and ductility
- Good high-temperature strength and resistance of thermal fatigue
- Good through-hardening properties
- Small distortion during hardening
1.2344 Hot Work Tool Steel
1.2344 is pressure resistant hot work die steel. The steel by electroslag remelting, uniform material, good hardenability, has excellent machining performance and polishing performance, high toughness and plasticity, good high and low temperature wear resistance and resistance to high temperature fatigue and heat resistance.
DIN 1.2344 steel, we can supply the round bar, steel flat bar, plate, hexagonal steel bar and steel square block. Moreover, 1.2344 steel Round bar can be saw to your required lengths as one offs or multiple cut pieces. Furthermore, 1.2344 steel Rectangular pieces can be saw from flat bar or plate to your specific sizes.
And Ground tool steel bar can be supply, providing a quality precision finished bar to tight tolerances.
- Length:3-5.8mm or Customization
- Surface:black, peeled, or rough turned
- Heat treatment:air-cooling, normalized, annealed, Q&T
- Smelting process:EAF+LF+VD
Supply Form & Size & Tolerance
Supply Form | Size(mm) | Process | Tolerance | |
Round | Φ6-Φ100 | Cold Drawn | Bright/Black | Best H11 |
Φ16-Φ350 | Hot Rolled | Black | -0/+1mm | |
Peeled/ground | Best H11 | |||
Φ90-Φ1000 | Hot Forged | Black | -0/+5mm | |
Rough Turned | -0/+3mm | |||
Flat/Square/Block | Thickness :120-800 | Hot Forged | Black | -0/+8mm |
Width:120-1500 | Rough Machined | -0/+3mm |
Remark:Tolerance can be customized as per requests
1.2344 Chemical Composition
Standard | Grade | C | Si | Mn | P | S | Cr | Mo | V |
ASTM A681 | H13 | 0.32-0.45 | 0.8-1.2 | 0.20-0.50 | 0.03 | 0.03 | 4.75-5.50 | 1.1-1.75 | 0.8-1.2 |
DIN ISO 4957 | 1.2344 | 0.37-0.42 | 0.9-1.2 | 0.3-0.5 | 0.03 | 0.03 | 4.8-5.5 | 1.2-1.5 | 0.9-1.1 |
GB/T 1299 | 4Cr5MoSiV1 | 0.32-0.42 | 0.8-1.2 | 0.2-0.5 | 0.03 | 0.03 | 4.75-5.5 | 1.1-1.75 | 0.8-1.2 |
JIS G4404 | SKD61 | 0.35-0.42 | 0.8-1.2 | 0.25-0.5 | 0.03 | 0.03 | 4.8-5.5 | 1-1.5 | 0.8-1.15 |
1.2344 Physical Property
Temperature | 20°C | 400°C | 1110°C |
Density G/cm3 | 7.8 | 7.7 | 7.6 |
Modulus of elasticity N/mm2 | 210000 | 180000 | 140000 |
Coefficient of thermal expansion, per °C from 20°C | — | 12.6 x 10^–6 | 13.2 x 10^–6 |
Thermal conductivity W/m °C | 25 | 29 | 30 |
Melting point | 1427°C | ||
Specific Gravity | 7.75 | ||
Machinability | 65-70% of a 1% carbon steel |
1.2344 Mechanical Property
Tempering Tem. °C | After quenched | 200 | 400 | 500 | 520 | 550 | 580 | 600 | 650 | 700 |
Hardness HRC | 56 | 54 | 54 | 55.5 | 54 | 52.5 | 49 | 45.5 | 33 | 28 |
Tensile Strength Mpa | — | — | 2040 | 2100 | 2080 | 1980 | 1780 | 1650 | 1180 | — |
Reduction of area | — | — | 40 | 34 | 40 | 48 | 53 | 54 | 55 | — |
Elongation % | — | — | 11 | 11 | 11.5 | 12 | 12.5 | 14 | 18 | — |
Impact J | — | — | 40 | 32 | 35 | 50 | 60 | 70 | 100 | — |
Forging
Heat AISI H13 with two steps,first heat the temperature to 750°C – 800°C ,hold for suitable time,then heat the temperature up to 1050°C – 1100°C,hold enough time for the steel to be thoroughly heated.Reheat is necessary when temperature below 950oC.H13 steel should be cooled as slowly as possible in the furnace.Annealing is always required after forged.
Annealing
Annealing is considered as a treatment suitable for machining.Heat the temperature to 840°C-860°C, hold suitable time for the steel to be thoroughly heated, then furnace cooling.Annealed black surface, hardness≤255HB.
Stress Relieving
It is recommended to stress relieve after machining and prior to hardening to minimise the possibility of distortion.H13 should be heated through to 600-650°C, holding time 2 hours. Cool slowly in furnace.
Hardening
Pre-heating temperature: 600–850°C,normally in two pre-heating steps.
Austenitizing temperature: 1020–1050°C,normally 1020–1030°C
Temperature,°C | Soaking Time,Minutes | Hardness before tempering |
1025 | 30 | 53±2 HRC |
1050 | 15 | 54±2 HRC |
Soaking time = time at hardening temperature after the tool is fully heated through.
Tempering
Tempering should be carried out immediately after quenching. Heat slowly and uniformly to the tempering temperature,soak well not less than 2 hours(one hour per 25mm of total thickness).The usual tempering range is 530-650°C depending on the hardness requirements and the operating temperature of the tool.Double tempering is strongly recommended,H13 H13 should be cooled to room temperature between tempers.Tempering within the range 425-550°C is not recommended due to the reduction in toughness properties.
Application
H13 hot work tool steel has excellent properties which is widely used in hot work and cold work applications.
Typical applications include die casting dies for aluminium, magnesium and zinc, extrusion dies for aluminium and brass, liners, mandrels, pressure pads, followers, bolsters, die cases, die holders and adaptor rings for copper and brass extrusion. H13 is used to produce hot stamping and press forge dies, split hot heading dies, gripper dies, hot punching, piercing and trimming tools. Other applications include plastic moulds, shear blades for hot work and hot swaging dies.
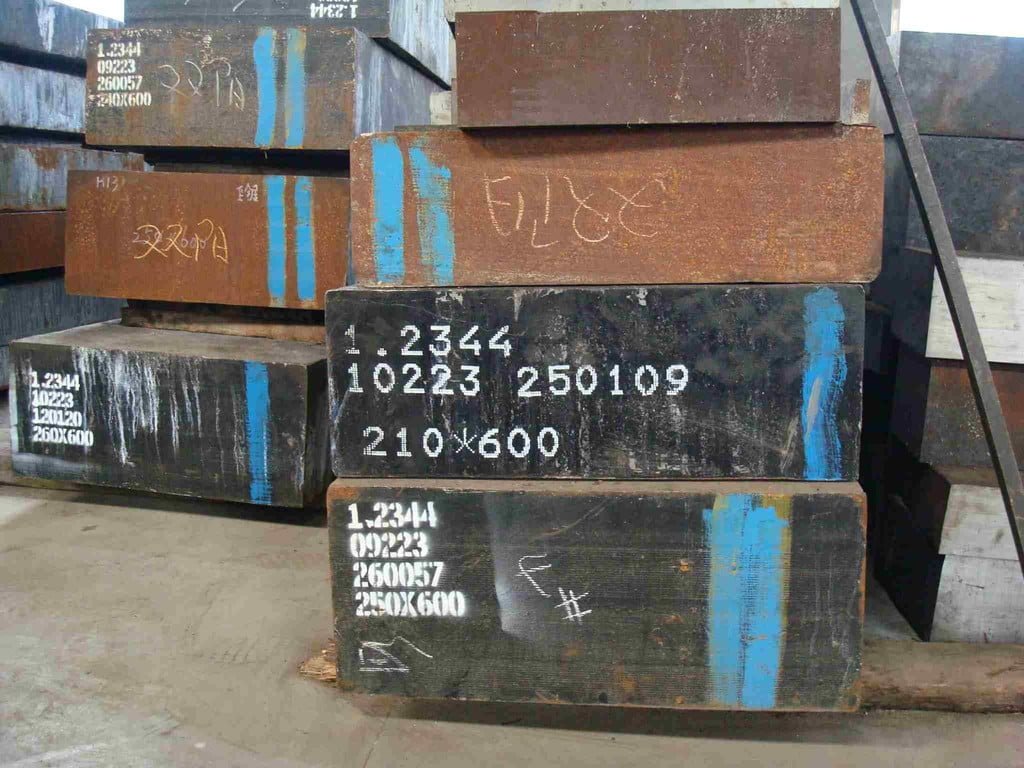
What is the difference between steel 2344 and 1.2344?
2344 steel and 1.2344 are the same material.
The difference between 1.2344 and H13
1.2344 and H13 are two similar grades, H13 is the American standard and 1.2344 is the German standard.
They differ slightly in composition.