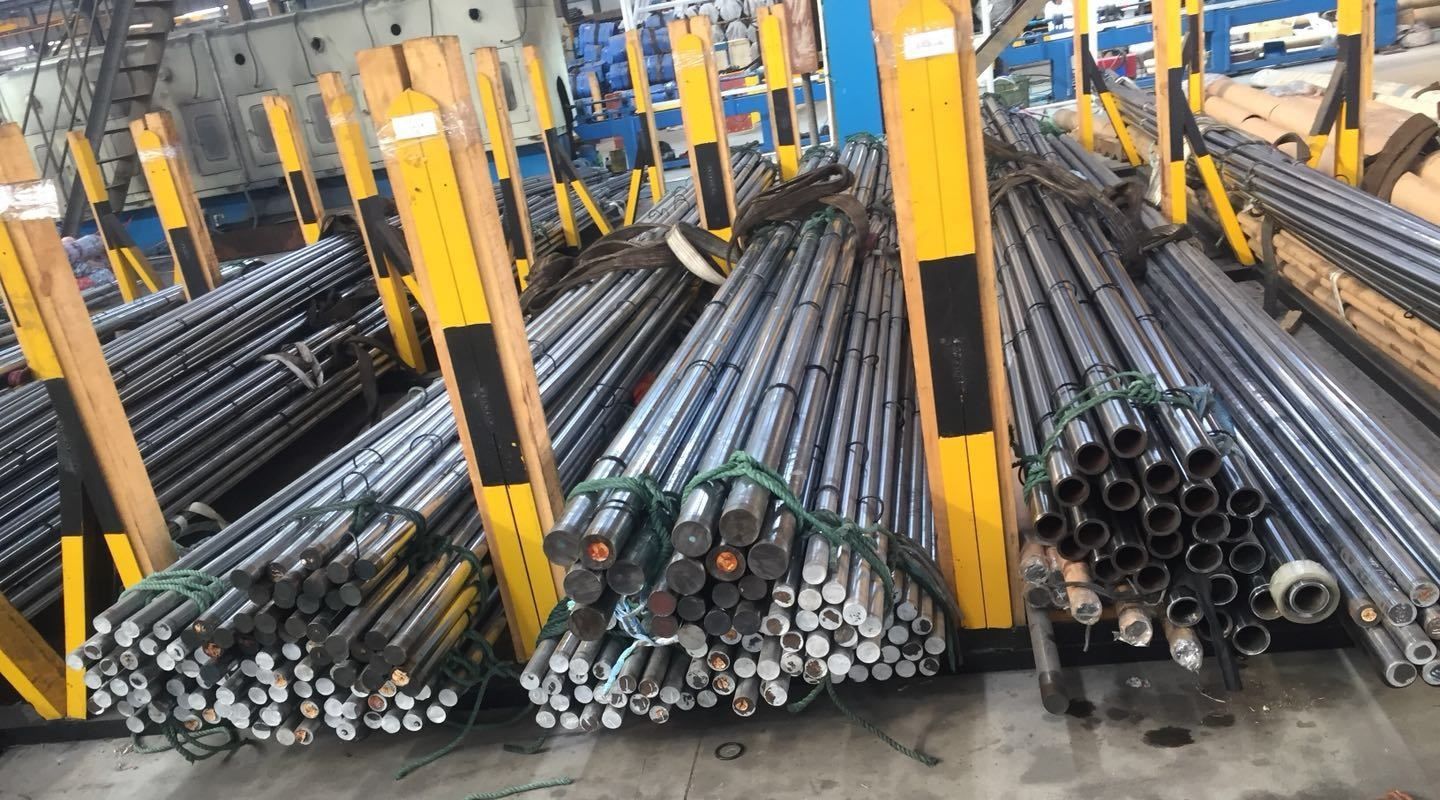
Zawartość tej strony pochodzi z Iqsdirectory.com
Wstęp
Jest to najobszerniejszy przewodnik po kuciu na zimno dostępny online.
Ten artykuł obejmuje następujące tematy:
- Co to jest kucie na zimno i jak to działa
- Cold forging benefits & disadvantages
- Kucie na gorąco a kucie na zimno
- Zastosowane metale i sprzęt/maszyny
- Zastosowania kucia na zimno
- I więcej…
Rozdział pierwszy – Co to jest kucie na zimno i jak to działa?
Cold forging is a metal shaping & manufacturing process in which bar stock is inserted into a die and squeezed into a second closed die. The process, completed is at room temperature or below the metal‘s recrystallization temperature to form a metal into a desired shape or configuration.
Kucie na zimno to wydajny i ekonomiczny proces odkształcania metalu do produkcji dużych ilości części przy niskich kosztach. Istnieją trzy metody kucia, które różnią się w zależności od temperatury, która może być zimna, ciepła lub gorąca i obejmują użycie młotków, matryc lub pras do kształtowania, ściskania, odkształcania i walcowania metali. Kucia na zimno nie należy mylić z obróbką skrawaniem lub odlewaniem, ponieważ efektem końcowym jest produkt mocniejszy i wyższej jakości.
W przeciwieństwie do kucia na ciepło lub na gorąco, kucie na zimno kształtuje i odkształca pręt w temperaturze pokojowej przy użyciu zlokalizowanej siły ściskającej. W zależności od wymagań projektu części, przedmiot obrabiany może przechodzić przez wiele matryc lub być uderzany kilka razy z rzędu, aby uzyskać właściwy kształt.
Rozdział drugi — Jak działa kucie na zimno
Niski koszt kucia na zimno wynika z obniżenia kosztów pracy i wyeliminowania obróbki wtórnej. Części są produkowane szybko i wydajnie w tempie nawet 1000 sztuk na godzinę, co obniża koszt jednostkowy. Produkcja polega po prostu na wstawieniu kawałka metalu i umożliwieniu maszynom szybkiego i ekonomicznego wykonania pracy.
Gotowe produkty z kucia na zimno mają doskonałe wykończenie powierzchni i lepszą stabilność wymiarową, co widać na poniższym obrazku. Różne procesy zwiększają wytrzymałość i trwałość przedmiotu obrabianego, tworząc trwałe produkty lub części.
Proces kucia na zimno
Krok 1: Smar
– Przed kuciem przedmiot obrabiany jest smarowany, aby zapobiec przywieraniu do matrycy i utrzymać go w chłodzie podczas procesu formowania, ponieważ odkształcanie może powodować temperatury od 250° do 450°.
Krok 2: Wkładanie metalowego elementu
– Metalowy kawałek jest umieszczany na matrycy, która ma kształt końcowej części. Matryca może mieć dwie sekcje, z których jedna jest przymocowana do młotka, a druga pod przedmiotem obrabianym. Młotek to górna część i mechanizm uderzający, który wytwarza siłę deformującą metalowy element.
Krok 3: Udar
– Uderzenie przedmiotu obrabianego lub skok może być wywołane przez trzy mechanizmy – hydrauliczny, pneumatyczny lub mechaniczny. Każda z technik wbija wałek z młotkiem w dół z dużą siłą na przedmiot obrabiany, aby uzyskać pożądany kształt. Dzieje się to w skali milisekund. W niektórych przypadkach konieczne może być upuszczenie młotka kilka razy z rzędu, aby uzyskać dokładny kontur i kształt.
Krok 4: flashowanie
– Flash to nadmiar metalu wokół matrycy lub zestawu matryc. Rozciąga się od korpusu odkuwki jako cienka płyta w miejscu styku matryc i jest usuwana podczas okrawania. Błysk ogranicza płynięcie metalu zapewniając doskonały odcisk. Obecność wypływki jest niezbędna, aby zmusić metal do całkowitego wypełnienia matrycy.
Krok 5: Usuwanie części
– Sposób usunięcia części zależy od rodzaju procesu. Większość współczesnych producentów wykorzystuje automatyzację do usuwania części za pomocą przenośnika lub robota ręcznego. Jest to kolejny sposób oszczędzania kosztów, który eliminuje potrzebę obsługi materiałów.
Krok 6: Po kształtowaniu
– Podobnie jak w przypadku innych części procesu, może to przybierać różne formy. W przypadku części, które wymagają jednej matrycy i jednego skoku, część jest przycinana i wysyłana do wysyłki. W przypadku części, które mają wiele aspektów, są one przenoszone do innych procesów matrycowych w celu dodania funkcji. Ruch matrycy ze stanowiska na stanowisko jest zwykle zautomatyzowany. W przypadku większych części stosuje się inne metody zmechanizowane, które mogą obejmować hi-lo, wózek widłowy lub dźwig.
Rozdział trzeci – Korzyści z kucia na zimno
W tym rozdziale szczegółowo omówiono sześć głównych zalet zimnego pogranicza. Zawierają:
- Opłacalne
- Szybsza produkcja
- Przyjazny dla środowiska
- Doskonała wydajność produktu
- Wysoka wydajność produkcyjna
- Szeroki wybór metali
Poniższe informacje przedstawiają niektóre zalety kucia na zimno i dlaczego jest tak szeroko stosowane. Rozdział trzeci to porównanie kucia na zimno z kuciem na gorąco oraz zalety każdego z nich.
Opłacalny:
Kucie na zimno jest tanie ze względu na 3 czynniki – obróbkę wstępną, temperaturę i wykończenie. W innych metodach kształtowania metalu przedmiot obrabiany musi zostać poddany jakiejś formie obróbki wstępnej, takiej jak ogrzewanie. Piece, piece lub elektryczność są zwykle używane do podniesienia temperatury metalu powyżej jego punktu rekrystalizacji. Są drogie w utrzymaniu, wytwarzają zanieczyszczenia i są czasochłonne.
W przypadku kucia na zimno przedmiot obrabiany jest kompletny i wymaga minimalnej obróbki wykończeniowej, co pozwala zaoszczędzić na kosztach robocizny.
Kucie na zimno zapewnia oszczędności materiałowe do 70% kosztów produkcji, ponieważ jest bardzo mało odpadów i złomu.
Szybsza produkcja:
Kucie na zimno to prosty proces, w którym przedmiot obrabiany jest umieszczany bezpośrednio w maszynie do kucia w celu natychmiastowego wytworzenia gotowej części. Współcześni producenci wykorzystują automatyzację do ładowania przedmiotu obrabianego i wyjmowania go z prasy. Jak widać na tym schemacie, metal jest podawany do maszyny, przetwarzany i przesuwany dalej. Czas między wejściem a zakończeniem jest krótszy niż sekunda.
Przyjazny dla środowiska:
Głównym powodem, dla którego kucie na zimno jest przyjazne dla środowiska, jest wyeliminowanie zapotrzebowania na ciepło, ponieważ opary i dym z pieców powodują znaczną emisję węgla. Zmniejsza to również koszty, ponieważ producenci nie muszą instalować urządzeń do filtrowania i czyszczenia powietrza.
Doskonała wydajność produktu:
Kucie na zimno wytwarza produkty o doskonałych parametrach, ponieważ zmienia strukturę ziarna przedmiotu obrabianego, aby dostosować się do konfiguracji końcowej części.
Eliminuje możliwe negatywne reakcje:
Obróbka metalu może stwarzać wiele potencjalnych problemów. Kucie na zimno eliminuje niektóre negatywne efekty, takie jak zmęczenie porowatością, zwiększając ogólną wytrzymałość metalu i usuwając ryzyko utraty integralności materiału.
Wyższa jakość i długa żywotność:
Części kute na zimno są w stanie wytrzymać duże obciążenia. Gdy przedmiot obrabiany jest wypychany poza granicę plastyczności lub elastyczności, nadal jest w stanie zachować swój zmieniony kształt.
Zachowanie tolerancji części:
Krytyczne i wąskie tolerancje części są utrzymywane przez cały cykl produkcyjny. Są one odtworzone w najdrobniejszych szczegółach, dzięki czemu każda część jest dokładną kopią pierwszej.
Swoboda projektowania:
W przeciwieństwie do innych procesów, kucie na zimno zapewnia swobodę projektowania, gdzie można wytwarzać skomplikowane kontury i kształty, które wymagałyby wielu różnych i kosztownych metod wtórnych w innych procesach.
Wysoka wydajność produkcyjna:
Chociaż mogą istnieć różnice między metodami produkcji kucia na zimno, wysoka prędkość produkcyjna kucia na zimno może wyprodukować od 50 sztuk na minutę do ponad 400. Jedyną rzeczą, która wpływa na szybkość procesu, jest rozmiar części.
Szeroki wybór metali:
Można kuć szeroką gamę metali, w tym metale twarde, takie jak stal węglowa, stal stopowa i stal nierdzewna, a także metale miękkie, takie jak aluminium, mosiądz i miedź.
To zdjęcie przedstawia próbkę śrub, które zostały wyprodukowane przez kucie na zimno. Każda z różnych śrub została wykonana z innego metalu. Uwzględniono te wykonane z miedzi, mosiądzu, aluminium i stali.
Rozdział czwarty — Kucie na gorąco kontra zimno
Różnica między kuciem na gorąco a kuciem na zimno polega na temperaturze: kucie na zimno odkształca i napręża metale w temperaturze pokojowej, podczas gdy kucie na gorąco podgrzewa metale w pobliżu lub w temperaturze topnienia.
Kluczem do zakresu temperatur jest rekrystalizacja: kucie na zimno odbywa się przed rekrystalizacją, podczas gdy kucie na gorąco podgrzewa metal powyżej punktu rekrystalizacji.
Wybór kucia na zimno vs kucia na gorąco zależy od:
- Wyposażenie i obróbka wytwórców: producenci specjalizują się w jednym lub drugim procesie, aby zmaksymalizować wykorzystanie swojego sprzętu.
- Wymagania klientów: Podczas fazy projektowania części inżynierowie podejmują decyzję dotyczącą najlepszego procesu produkcji swoich projektów, ponieważ kucie na zimno i na gorąco ma swoje ograniczenia.
- Rodzaje produkowanych części: Wiele razy ograniczenia dotyczące wyboru odpowiedniego procesu są określone przez projekt części, ponieważ określone części można kuć tylko na gorąco, podczas gdy inne doskonale nadają się do kucia na zimno. Projekty części kutych na zimno są proste, bez skomplikowanych szczegółów, podczas gdy kucie na gorąco może wytwarzać elementy o niezwykle precyzyjnych, drobnych elementach.
- Niższe wymagania dotyczące kosztów: W miarę możliwości producenci wybierają kucie na zimno, ponieważ wymaga mniej sprzętu i nie obejmuje ogrzewania, co znacznie obniża całkowity koszt produkcji.
Kucie na gorąco
Kucie na gorąco odbywa się w wyjątkowo wysokich temperaturach od 700 ° C lub 1292 ° F do 1000 ° C lub 1832 ° F. Podwyższone temperatury pomagają uniknąć naprężeń i utwardzania, a także obniżają przepływ naprężeń i ilość energii potrzebnej do odkształcenia i kształtować metale. Gdy metale ostygną, zachowują swój zdeformowany kształt. W procesie formowania wykorzystuje się prasy hydrauliczne, pneumatyczne i mechaniczne.
Charakterystyka kucia na gorąco:
Matryce lub formy:
Jednym z głównych wydatków związanych z kuciem na gorąco jest koszt produkcji matryc i form wykonanych ze wzmocnionej stali, zaprojektowanej tak, aby wytrzymywała ekstremalne temperatury, była odporna na zmęczenie i miała plastyczność, wytrzymałość i wytrzymałość na rozciąganie.
Formy kucia na gorąco:
Chociaż wiele metod kucia na gorąco jest podobnych do metod kucia na zimno, inne metody obejmują formowanie gazowe, hartowanie matrycowe, formowanie ciągnione i izotermiczne.
Temperatura metalu:
Rodzaj procesu określa temperaturę metalu podczas jego kształtowania. W niektórych procesach metal jest całkowicie topiony i wlewany do formy lub przeciskany przez matrycę. W innych jest wyżarzany i kształtowany przez matrycę lub formę pod naciskiem i ciśnieniem.
Niebezpieczne czynniki środowiskowe:
Największą wadą jest ilość zanieczyszczeń powstających w procesie ogrzewania. Był to główny problem od jego powstania podczas pierwszej rewolucji przemysłowej i był to problem, z którym producenci nieustannie borykali się przez lata.
Ogrzewanie metali:
Części muszą być podgrzewane powyżej punktu rekrystalizacji, który wynosi znacznie ponad 300° F i może dochodzić do 1000 stopni. Do osiągnięcia odpowiednich temperatur wymagane są duże piece lub piece.
Zaangażowany czas:
Skomplikowany charakter kucia na gorąco wymaga czasu na podgrzanie metalu, obróbkę i schłodzenie. Chociaż rzeczywiste tłoczenie, odkształcanie lub kształtowanie zajmuje mniej więcej tyle samo czasu, co kucie na zimno, procesy ogrzewania i chłodzenia wymagają starannej opieki i zarządzania przez dłuższy czas.
Wyniki kucia na gorąco:
Ogrzewanie i chłodzenie metali zwiększa ich wytrzymałość, wytrzymałość i plastyczność, ale zmniejsza ich twardość. Podczas procesu chłodzenia metale mogą się wypaczać i tracić kształt.
Skalowanie:
Kucie na gorąco może powodować utlenianie, które prowadzi do osadzania się kamienia, co może odbarwić powierzchnię metalu, utrudniając wykończenie.
Wykończeniowy:
Części muszą być wykończone, aby usunąć deformacje, wady i błędy z procesu nagrzewania. Te drugorzędne operacje są pracochłonne i wymagają kilku rodzajów specjalistycznego sprzętu.
Kucie na zimno
Temperatura, w której odbywa się kucie, odróżnia kucie na zimno od kucia na gorąco. Aby część była kuta na gorąco, jest ona podgrzewana do temperatury powyżej punktu rekrystalizacji, co zmienia jej mikrostrukturę. Gdy jest podgrzewany, jego wewnętrzne naprężenia i wytrzymałość są eliminowane, aby uczynić go bardziej plastycznym. Kucie na zimno nie wymaga ogrzewania, dzięki czemu metal zachowuje swoją wytrzymałość i mikrostrukturę.
Charakterystyka odkuwek na zimno jest następująca:
Temperatura formowania:
Metale są kształtowane w temperaturze pokojowej poniżej ich punktu rekrystalizacji, co ma tę zaletę, że obniża koszty i pozwala uniknąć wydatków na piece.
Prędkość:
Prędkości wahają się od siedmiu sztuk na minutę w przypadku maszyn o małej objętości do 400 sztuk na minutę w przypadku maszyn o dużej objętości.
Sprzęt:
Kucie na zimno odbywa się za pomocą maszyn zaprojektowanych do kształtowania metalu i obejmuje ściskanie, gięcie, ścinanie i ciągnienie. Sprzęt dostępny jest w szerokiej rozpiętości cenowej w zależności od ilości technologii oraz jej wielkości.
Koszt:
Oszczędności kosztów wynikają z materiału i szybkości. Oszczędności materiałowe wynikają z niewielkiej ilości wytwarzanego złomu, która wynosi do 70%. Ponieważ części są produkowane w bardzo szybkim tempie, koszt jednostkowy jest znacznie niski.
Czynniki środowiskowe:
Nie ma żadnych emisji ani zanieczyszczeń, jak widać na poniższej maszynie firmy Stalcop. Wszystko jest samoistne i zamknięte. Węgiel i inne zanieczyszczenia są eliminowane, ponieważ nie ma potrzeby podgrzewania metalu.
Wyniki kucia na zimno:
Jak widać na poniższym diagramie, struktura ziarnowa metali jest przestawiana, aby podążać za przepływem końcowej części, eliminując zmęczenie porowatością, zwiększając wytrzymałość na ścinanie i zmniejszając ryzyko integralności materiału. Napinając metal, staje się on mocniejszy i bardziej sprężysty. Wadą jest to, że po kuciu na zimno metal traci swoją plastyczność i staje się bardziej kruchy.
Skalowanie:
Przed kuciem metalu ważne jest, aby usunąć wszelkie osady, takie jak rdza lub korozja, które mogą powstać podczas przechowywania. Jeśli nie zostanie usunięta, część będzie miała takie samo pogorszenie, jak w przypadku kucia na gorąco.
Wykończeniowy:
Wymagane jest bardzo mało wykończenia. Po przetworzeniu część jest gotowa do użycia lub wysyłki.
Wady kucia na zimno
Kucie na zimno nie jest doskonałe. Jak każda metoda produkcji, kucie na zimno ma swoje ograniczenia i ograniczenia, które należy wziąć pod uwagę przed wybraniem go do następnego projektu produkcyjnego.
- Tylko proste kształty i projekty mogą być produkowane w dużych ilościach. Unikalne, niezwykłe lub skomplikowane wzory nie mogą być kute na zimno. Poziomy odkształceń i stopnie kształtowania są ograniczone, a metale kute na zimno mają mniejszą plastyczność.
- Zmiana struktury ziarna metalu nadaje mu dodatkową wytrzymałość, ale może powodować naprężenia szczątkowe.
- Niektóre metody kucia na zimno wymagają obróbki cieplnej w celu wyeliminowania ewentualnych pęknięć lub pełzania.
- Istnieje ograniczenie rodzajów metali, które mogą być kute na zimno. Nie należy wybierać tych o niskiej ciągliwości i wrażliwości na utwardzanie przez odkształcenie, ponieważ tracą one swoją plastyczność i pękają pod wpływem naprężeń rozciągających. Można używać tylko metali o twardości HRC 44 w skali Rockwella.
- Procesy produkcyjne wymagają dużej siły, aby wytworzyć niezbędną siłę ściskającą i ciśnienie. Chociaż dodanie hydrauliki i pneumatyki zmniejszyło rozmiar sprzętu, nie wyeliminowało ilości energii zużywanej przez maszyny.
- Narzędzia, matryce i formy muszą być specjalnie zaprojektowane, a także solidne i wystarczająco mocne, aby wytrzymać stałą, powtarzalną siłę.
Rozdział piąty – Procesy kucia na zimno
Rozwój różnych technologii i postęp w obróbce metali zaowocował kilkoma metodami kształtowania i formowania metalu na zimno. Każdy służy do innego zastosowania, ale wszystkie są zaprojektowane do wydajnego i szybkiego wytwarzania produktów bez konieczności wtórnego wykańczania.
Osiem najczęstszych procesów kucia na zimno to:
- Pochylenie się
- Walcowanie na zimno
- Zamknięta matryca
- Rysunek
- Wyrzucenie
- Otwórz matrycę
- Kucie pierścieni
- Kształtowanie
Jak omówię to na końcu tego rozdziału, procesów jest więcej niż tylko te wymienione. Poniższe opisy zapewniają podstawowe dane umożliwiające wstępne zrozumienie różnych metod.
Również bardzo ważnym aspektem procesu kucia na zimno jest rodzaj stosowanego smaru. Dwa najczęstsze to fosforan cynku lub jakaś forma powłoki polimerowej. Chociaż kucie na zimno odbywa się w temperaturze pokojowej, proces gięcia i kształtowania zwiększa temperaturę metali. Smar może zapobiegać błędom i zapobiegać przywieraniu przedmiotu obrabianego do matrycy oraz wydłużać żywotność narzędzi.
Producenci smarów oferują różnorodne produkty pasujące do każdego rodzaju procesu kucia na zimno. Na ilustracji przedstawiono smary grafitowe, ale dostępne są smary bez grafitu, a także glinian wapnia, fluorek glinu i powłoki fosforanowe.
Typowe metody kucia na zimno:
Gięcie –
Gięcie odbywa się za pomocą prasy i matrycy, w której obrabiany przedmiot jest dociskany do narzędzia kształtującego. Jest również określany jako walcowanie piramidy i jest czasami używany do przygotowania elementu do innego procesu kucia na zimno. Obrabiany przedmiot jest napinany wzdłuż jednej osi, aby utworzyć kąt.
Walcowanie na zimno –
Walcowanie to proces formowania, w którym metal jest przepuszczany przez parę obracających się rolek w celu odkształcenia plastycznego spowodowanego siłą ściskającą. Naprężenia ściskające powodują tarcie między rolkami a powierzchnią półfabrykatu metalowego. Jest powszechnie stosowany do obróbki stali.
Zamknięta matryca –
W przypadku kucia matrycowego przedmiot obrabiany jest kształtowany przez kolejne uderzenia mechaniczne po umieszczeniu go pomiędzy dwiema połówkami matrycy. Ponieważ młotek wielokrotnie uderza w przedmiot obrabiany, niektórzy producenci określają kucie matrycowe jako kucie matrycowe. Gdy metal jest uderzany, wpływa do wnęk matrycy, zmieniając go w kształt matrycy.
Rysunek -
Ciągnienie polega na przeciągnięciu przedmiotu obrabianego przez matrycę za pomocą siły rozciągającej przyłożonej na wyjściu matrycy. Podczas przeciągania przedmiotu obrabianego zmniejsza się pole przekroju poprzecznego wraz ze wzrostem jego długości. Uformowane metale mają mniejszą tolerancję wymiarową niż te wytwarzane przez walcowanie.
Wytłaczanie –
Kęs lub kęs jest przeciskany przez matrycę pod działaniem siły ściskającej, która ma profil końcowej części. Po przejściu jest cięty na wymaganą długość, przygotowywany do wysyłki lub wysyłany do dalszej obróbki. Siła wywierana podczas wytłaczania na zimno może sięgać nawet 20 000 kN lub 2007 ton. Wytłaczanie można wykonać do przodu, do tyłu lub w obu kierunkach.
Wyciskanie do przodu – metal jest popychany do przodu przez matrycę.
Wytłaczanie wsteczne – metal wchodzi do matrycy do tyłu, tworząc otwory lub miseczki, dzięki czemu dno jest grubsze niż jego boki.
Wytłaczanie boczne — siła jest przykładana poprzecznie, na boki, w kierunku wyciągnięcia, aby dodać drugą cechę do profilu.
Otwórz kostkę:
Kucie matrycowe obejmuje dwie płaskie matryce bez wstępnie wyciętego profilu. Przedmiot obrabiany jest stopniowo kształtowany przy użyciu kilku procesów, co pozwala na produkcję szerokiej gamy kształtów i rozmiarów. Jest używany głównie w projektach zawierających duże metalowe elementy, które wymagają najwyższej integralności strukturalnej. Odkształcenie uzyskuje się przez zmianę położenia przedmiotu obrabianego.
Ściskanie, znane również jako formatowanie, jest formą obróbki z otwartą matrycą, w której siła jest przykładana na niewielką odległość, co zapewnia dokładne wykończenie wymiarowe.
Kucie pierścieni –
Z kuciem pierścieniowym, okrągły przedmiot obrabiany dziurkowany w środku, aby uzyskać kształt pączka. Gdy przekłuty kawałek jest obracany, jest wbijany i ściskany. W procesie tym powstają bezszwowe pierścienie o doskonałych średnicach i wytrzymałości.
kształtowanie –
Kucie lub kucie promieniowe to odkształcenie przedmiotu obrabianego, tak aby dwie części pasowały do siebie. Jest zautomatyzowany i wysoce niezawodny. Dwa rodzaje kształtowania to rurowe i promieniowe. Kształtowanie rur jest jak wytłaczanie, w którym przedmiot obrabiany jest przeciskany przez matrycę. W przypadku kucia promieniowego młotek przepycha przedmiot przez dwie lub więcej matryc.
Kiedy zaczniesz szukać producenta kucia na zimno, znajdziesz więcej metod niż siedem opisanych tutaj. Posiadanie podstawowej wiedzy na temat kilku możliwych metod pomoże ci przemawiać autorytatywnie i inteligentnie do producentów, a także będzie w stanie zinterpretować ich żargon.
Jak w przypadku każdej nowoczesnej metody produkcji, przekonasz się, że kucie na zimno stale się rozwija wraz z rozwojem nowych technik i metod. Ważnym i rosnącym czynnikiem jest dodanie automatyzacji i robotyki, które szybko zmieniają oblicze branży. Specjalista od kucia może wskazać właściwy kierunek, aby znaleźć proces, który najlepiej odpowiada Twoim potrzebom.
Rozdział szósty - Urządzenia i maszyny do kucia na zimno
Urządzenia i maszyny do kucia na zimno występują w trzech odmianach – hydraulicznej, pneumatycznej i mechanicznej. Podczas gdy niektórzy dostawcy specjalizują się tylko w jednym typie, większość ma kilka możliwości wyboru w zależności od ceny i rodzaju operacji. Technologia i automatyzacja są powszechne, jak widać na poniższym obrazku, który przedstawia prasę do kucia na zimno z serwomechanizmem firmy Marvel Machinery. Rendery projektów części są tworzone przy użyciu oprogramowania inżynierskiego, takiego jak CAD.
Istnieją wymagania, które muszą spełniać maszyny, aby mogły być używane do kucia na zimno.
- Siła – Procesy kucia na zimno zależą od ogromnej siły. Sprzęt z nim połączony musi być w stanie pochłonąć tę siłę i ją rozproszyć.
- Równowaga — maszyny muszą być wyważone statycznie i dynamicznie, aby zredukować wibracje i zwiększyć wydajność.
- Wytrzymałość w czasie – Niezależnie od metody kucia na zimno, każda wymaga dużej, powtarzalnej siły. Aby maszyna przetrwała, musi być w stanie wytrzymać tę siłę.
- Wiele operacji – Nowoczesne maszyny do kucia na zimno lub formowania, zwane hederami, wykonują od jednej do kilku operacji podczas jednego procesu. Jest to konieczne, ponieważ istnieje ograniczona liczba odkształceń, które można wykonać jednym pociągnięciem.
Rodzaje sprzętu do kucia na zimno:
Hydrauliczny młot kuźniczy –
Hydrauliczny młot do kucia matrycowego został zaprojektowany tak, aby zapewnić maksymalną siłę przy najniższej inwestycji. Może wytwarzać szeroki asortyment wycisków z różnych matryc. Działa w oparciu o inżynierskie koncepcje hydrauliki, w których nieściśliwa ciecz znajduje się w cylindrze. Kiedy ciecz jest ściskana przez tłok, wał z zamocowaną matrycą jest wbijany w obrabiany przedmiot.
Prasa śrubowa –
Prasa śrubowa jest używana do dużych odkształceń ze względu na małą prędkość prasy. Może być stosowany do matryc bezwypływkowych i odkuwek długich prętów. Konfiguracja prasy śrubowej pozwala na zastosowanie jej do matryc jednoszczelinowych, które obejmują gięcie i odkuwki końcowe. Silnik elektryczny zapewnia moc do obracania śruby, która popycha matrycę na obrabiany przedmiot.
Prasa szybkoobrotowa ramy C –
Konstrukcja ramy C nadaje się do operacji formowania, wykrawania, gięcia i wielokrotnego prasowania. Występują w wersjach z pojedynczą lub podwójną korbą, o sile uderzenia od 110 do 400 ton i skoku suwaka od 110 do 280 mm. Mogą przyjmować matryce o wysokości od 435 do 600 mm i mogą być używane do produkcji małych części.
Prasa pneumatyczna –
Pneumatyczna prasa zasilana może obejmować pełny zakres funkcji tłoczenia matryc. Wyposażone są w sterowane pneumatycznie sprzęgło i hamulec cierny. Zasilanie prasy jest wytwarzane przez sprężarkę powietrza, która dociska młot kuźniczy do przedmiotu obrabianego za pomocą ciśnienia powietrza w cylindrze z tłokiem.
Prasa mechaniczna na zimno –
Spośród odmian maszyn do kucia na zimno wersja mechaniczna jest najmniej używana, ponieważ muszą być bardzo duże, aby zapewnić niezbędną siłę. Mają koło zamachowe, które przechowuje energię z silnika. Kiedy koło zamachowe jest aktywowane, napędza młotek lub tłok w dół na matrycę. Może zapewnić moc przez kilka obrotów, ale musi pracować na biegu jałowym, aby odzyskać moc z silnika, zanim będzie mógł kontynuować swoje cykle.
Spośród wielu odmian sprzętu do kucia na zimno, najpopularniejszymi typami są hydrauliczne i pneumatyczne, ponieważ zajmują mniej miejsca, mogą dostarczać różne ilości siły i są programowalne. Kiedy analizujesz swoje wybory do produkcji, najlepiej jest znać rodzaje sprzętu, jaki posiada producent, ponieważ najnowocześniejszy sprzęt jest bardziej skłonny do produkcji części lepszej jakości.
Rozdział siódmy — Rodzaje kutych metali
Kucie na zimno oferuje szeroki wachlarz możliwości wyboru metalu do projektu. Różne odmiany obejmują twarde metale, takie jak stal węglowa, stal stopowa i stal nierdzewna. Aluminium, mosiądz, miedź, krzem i magnez to metale miękkie, których można użyć. Jedynym wymaganiem dla każdego metalu jest twardość 44 HRC lub niższa w skali Rockwella.
Miedź -
Miedź jest doskonałym metalem do kucia na zimno, ponieważ jest bardzo ciągliwa i ciągliwa. Można go kształtować, zginać lub ciągnąć przy użyciu niewielkiej siły i wytwarzać części odporne na korozję i rdzę.
aluminium –
Aluminium to metal nieżelazny, który jest niezwykle lekki i ma niską gęstość. Ma temperaturę topnienia 1220 ° F i jest ciągliwy, a także odporny na rdzę i korozję.
Stal węglowa -
Stal węglowa jest stopem żelaza i węgla. Różne stopnie zależą od ilości węgla zmieszanego z żelazem. Cechuje się wyjątkową wytrzymałością i ciągliwością.
Stal nierdzewna -
Stal nierdzewna stała się jednym z najczęściej używanych metali ze względu na swoją odporność na korozję, wygląd i wytrzymałość. Chociaż termin stal nierdzewna jest ogólnie używany do opisania dowolnej stali, która ma swoje właściwości, stal nierdzewna występuje w różnych gatunkach w zależności od zawartości stopu.
Stale stosowane do kucia na zimno
Stale niskowęglowe o zawartości węgla od 0,1% do 0,25%. Kucie na zimno poprawia utwardzanie przez odkształcenie stali, eliminując potrzebę austenityzacji, hartowania lub wyżarzania.
Metale nadające się do kucia na zimno
Odpowiedni stop | Charakterystyka plastyczności na zimno |
---|---|
Miedź | Doskonały |
Złoto, srebro i większość ich stopów | Doskonały |
Mosiądz- wkład z mosiądzu | Dobrze |
Platyna, pallad, tantal i ich stopy | Większość z nich nadaje się do formowania na zimno. |
Tytan i jego stopy | Czysty Ti i stopy o wysokiej ciągliwości, tak, ale stopy takie jak 6-4 są zdolne tylko do gorącej głowy. |
Nikiel i jego stopy | Czysty Ni tak, stopy o wydłużeniu w temperaturze pokojowej 20% lub więcej, tak. |
Żelazo i stale | Czyste żelazo, tak. Stale, zależy od stali. Wiele można formować na zimno. |
Uwagi przy wyborze metalu:
Najbardziej logiczną i najważniejszą rzeczą, jaką możesz zrobić, decydując się na metal do projektu, jest przeprowadzenie badań. Każdy rodzaj metalu reaguje na plastyfikację i deformację w inny sposób. Wybrany metal musi pasować do jego ostatecznego zastosowania i wymaganej wytrzymałości. Jeśli skonsultujesz się z ekspertem od kucia, możesz uzyskać cenne informacje, które pomogą Ci dokonać właściwego wyboru.
Rozdział ósmy – Zastosowania kucia na zimno
Kucie na zimno pozwala uzyskać kształty dowolnej wielkości z dużą dokładnością wymiarową i strukturalną. Efektywność ekonomiczna i szybkość kucia na zimno sprawiły, że jest to najpopularniejsza alternatywa produkcyjna.
Kucie na zimno spełnia wymagania nowoczesnych gałęzi przemysłu, ponieważ:
- Maksymalizuje wykorzystanie surowców: Kluczową inwestycją dla każdej operacji są surowce. Proces kucia na zimno ma bardzo ograniczone odpady. Flash i wykończenia można ponownie umieścić w procesie produkcyjnym.
- Zmniejsza koszty: Ponieważ części są produkowane szybko, koszt jednostkowy jest bardzo niski, co sprawia, że produkty końcowe są bardziej opłacalne i tańsze w produkcji.
- Produkuje wysokiej jakości części: kucie na zimno zwiększa wytrzymałość i trwałość części i produktów, gwarantując ich dłuższą żywotność. Struktura i właściwości kształtki nie zmieniają się, zapewniając doskonałą dokładność wymiarową.
Zastosowania, w których stosowane są części kute na zimno:
samochody –
Wysoka wytrzymałość, niezawodność, jakość i przystępna cena kucia na zimno sprawiły, że stało się ono bardzo atrakcyjne w produkcji samochodów. Części kute na zimno są instalowane w miejscach o dużym obciążeniu ze względu na ich doskonałą odporność na wstrząsy. Komponenty, takie jak układy napędowe, wały napędowe i rozpórki lub amortyzatory, są kute na zimno. Poniższy schemat przedstawia niektóre części podwozia samochodu, które są wytwarzane przez kucie na zimno.
Narzędzia ręczne i sprzęt –
Łączniki, takie jak gwoździe, śruby, nity i nakrętki, są od lat wytwarzane metodą kucia na zimno. Niskie tolerancje i doskonała dokładność wymiarowa powodują, że producenci narzędzi ręcznych wolą kucie na zimno niż inne metody, takie jak obróbka skrawaniem.
Wojskowy –
Wojsko ma bardzo surowe wymagania dotyczące sprzętu wojskowego i wybiera kucie na zimno do produkcji łusek, pocisków i innego sprzętu wojskowego. Części charakteryzują się wysoką niezawodnością i wydajnością w czasach kryzysu. Niskie tolerancje i wytrzymałość części czynią je idealnymi do broni wojskowej.
Produkcja kół zębatych –
Do produkcji kół zębatych stosuje się kucie na zimno, ponieważ eliminuje to konieczność skrawania podczas kształtowania kół zębatych. Koła zębate mogą być wytwarzane z kęsów mniejszych niż 50 mm lub kształtowane za pomocą drutu w zwojach. Może być konieczne pewne wyżarzanie w celu usunięcia naprężeń szczątkowych i utwardzenia przez zgniot. Ważną zaletą kutych na zimno kół zębatych jest to, jak płynnie i cicho zazębiają się.
Wniosek
- Kucie na zimno wytwarza metale o niskich tolerancjach i wysokiej dokładności wymiarowej przy bardzo niskich kosztach i dużych ilościach.
- Kucie na zimno szybko i szybko tworzy gotowe części, które są natychmiast dostępne i kompletne.
- Producenci oferują szeroki wybór procesów umożliwiających wyprodukowanie dokładnie i dokładnie takiej części, jakiej potrzebujesz, przy użyciu najnowocześniejszego i najbardziej zaawansowanego technicznie sprzętu.
- Będziesz mieć do wyboru szeroką gamę metali do realizacji swojego projektu, od stali hartowanej i stali nierdzewnej po miedź i aluminium.
- Znajdziesz bardzo niewiele ograniczeń co do liczby produktów, które możesz wyprodukować, od odpornych na naprężenia komponentów do twojego samochodu po nity, koła zębate i narzędzia robocze.
- Porównując kucie na zimno i na gorąco, przekonasz się, że kucie na zimno zajmuje mniej czasu i wytwarza mocniejsze i trwalsze części i produkty.