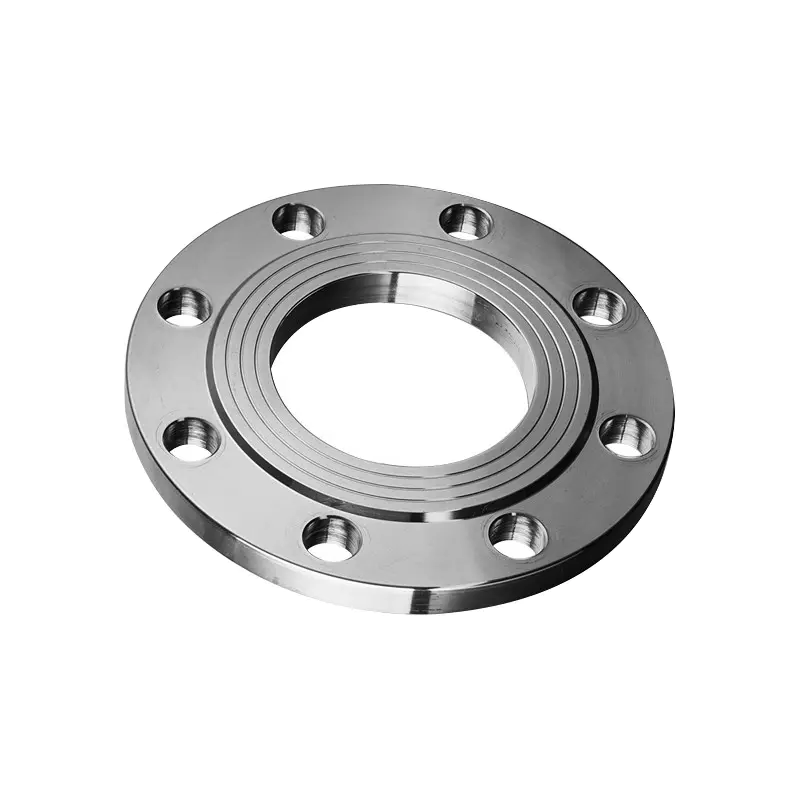
The production of nickel-based alloy flanges is a complex and intricate process, predominantly designed for pipe connection systems operating under high temperatures, high pressures, and extreme corrosive environments. The manufacturing process involves multiple stages, from material selection to final inspection, where each stage plays a crucial role in ensuring the performance and quality of the flanges.
1. Material Selection
The choice of materials is the most critical first step in the production of nickel-based alloy flanges. Nickel-based alloys are known for their excellent high-temperature performance, oxidation resistance, corrosion resistance, and mechanical strength. Common nickel-based alloys include:
- Inconel: This is an alloy primarily composed of nickel, chromium, and iron, extensively used in aerospace, oil, and chemical industries. It exhibits high resistance to heat and corrosion, making it suitable for extreme environments.
- Monel: Mainly composed of nickel and copper, Monel alloys show remarkable performance in marine environments, effectively resisting saltwater corrosion.
- Hastelloy: A high-performance alloy mainly used in the chemical and petroleum industries, known for its ability to withstand severe corrosive conditions.
When selecting materials, it is essential to consider the operating temperature, pressure, and required strength level of the flange to ensure the chosen alloy meets the process requirements and application conditions.
2. Melting
The melting process is the core stage in the production of nickel-based alloy flanges. This process typically occurs in high-temperature furnaces and can employ electric arc furnaces or induction furnaces. During melting, careful control of temperature, time, and atmosphere is necessary to ensure the alloy’s uniform composition and to minimize oxidation. Key considerations during melting include:
- Temperature Control: Both excessive and inadequate temperatures can adversely affect the properties of the alloy, necessitating precise temperature control during the melting process.
- Atmospheric Protection: Melting in an inert gas or vacuum environment effectively prevents oxidation and protects the purity of the alloy.
- Alloy Composition Monitoring: Periodic sampling and analysis of chemical composition are important to ensure adherence to the specified formulas.
3. Casting
Once melted, the molten metal is cast into molds to cool and solidify. There are several common casting methods:
- Sand Casting: This method is suitable for mass production, allowing for the reuse of sand molds, which keeps costs relatively low.
- Investment Casting: Ideal for small batches and complex shapes, this method produces high-quality surface finishes and precise dimensions.
- Lost Foam Casting: Utilizes foam patterns that evaporate during the casting process, suitable for high-precision and high-quality flange manufacturing.
During casting, controlling the cooling rate and temperature is crucial as it directly affects the microstructure, mechanical properties, and internal defects of the castings.
4. Heat Treatment
Post-casting, the flanges typically undergo heat treatment to enhance their properties. Common heat treatment processes include:
- Solution Treatment: The castings are heated to a solution temperature and then rapidly cooled, promoting equal distribution of phases within the alloy.
- Aging Treatment: This process increases the strength and hardness of the material through controlled temperature and time.
- Annealing: This reduces the hardness of the material and improves ductility for subsequent processing.
The specific time and temperature for heat treatment should be optimized based on the characteristics of the alloy used.
5. Machining
Machining is the stage where the cast flanges are finely processed to achieve accurate dimensions and surface quality. Common machining methods include:
- Turning: This process is used to machine the outer and inner diameters of the flange, ensuring that they meet specifications.
- Milling: Used to machine the flanges’ faces and grooves, particularly the sealing surfaces.
- Drilling: Creating holes for pipe connections, which is critical for the sealing performance of the flanges.
During machining, high-performance tools and cutting fluids are essential to extend tool life and improve processing quality.
6. Surface Treatment
Surface treatment not only enhances corrosion resistance but also improves the appearance of the flanges. Common surface treatment methods include:
- Polishing: Achieved through mechanical or chemical methods to create a smooth surface, enhancing aesthetics while reducing corrosion potential.
- Coating or Painting: Applying protective coatings to the flange surface to enhance corrosion resistance.
- Pickling: Removing oxide layers and impurities from the surface to improve the cleanliness of the metal.
The selection of suitable surface treatment processes can significantly improve the performance and extend the service life of the flanges.
7. Inspection and Quality Control
Strict inspection and quality control at each stage of the production process are essential. The main inspection methods include:
- Chemical Composition Analysis: Ensuring that the alloy’s composition meets the specified standards.
- Physical Property Testing: Such as hardness and tensile strength, to ensure the mechanical properties of the flange meet requirements.
- Non-destructive Testing: Using methods like ultrasound, magnetic particle inspection, and dye penetrant testing to check for defects in welded areas and cracks.
- Dimensional Measurement: Utilizing coordinate measuring machines (CMM) and other tools for precision measurement to ensure compliance with design specifications.
Quality control is integral throughout the production process, guaranteeing the reliability and safety of the final product.
8. Packaging and Shipping
After passing inspections, the nickel-based alloy flanges are appropriately packaged to prevent damage during transportation. The packaging materials should have moisture and rust resistance properties. Ultimately, the flanges are shipped to customers for installation and use.
9. Conclusion
The production of nickel-based alloy flanges involves multiple stages, including material selection, melting, casting, heat treatment, machining, surface treatment, and quality control. Each stage requires high technical standards and stringent management to ensure superior performance and durability of the products. As industrial technologies continue to advance, the application of nickel-based alloy flanges across various industries will become increasingly widespread, and production techniques will continue to evolve and improve.