Inconel X-750 and Inconel 625 are both high-performance nickel-chromium alloys developed for specific applications, but they have different compositions and properties that make them suitable for different environments and conditions.
Inconel X-750
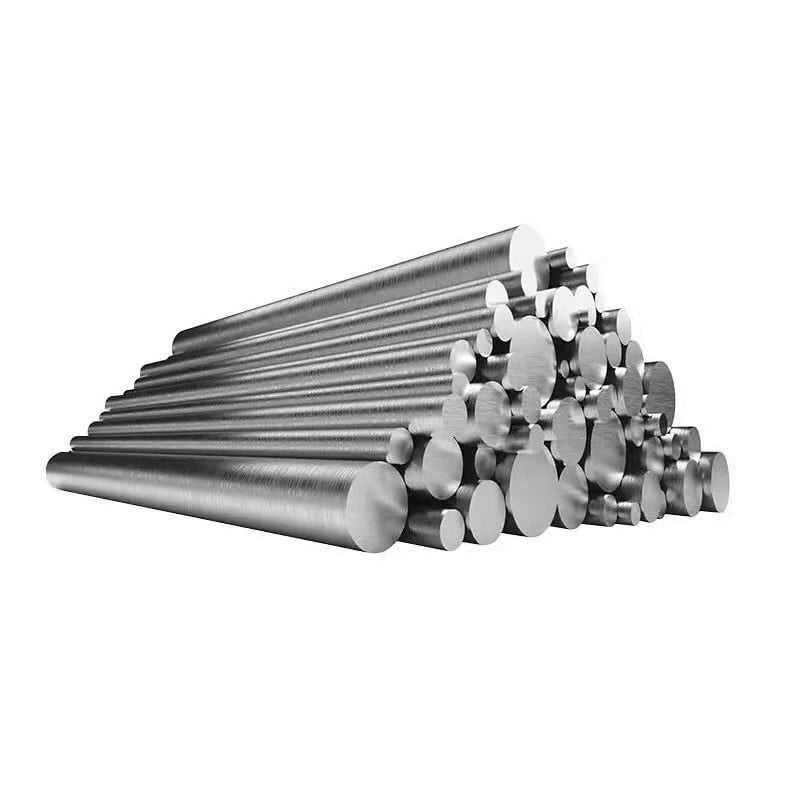
Composition:
- Inconel X-750 is a precipitation-hardenable nickel-chromium alloy.
- It typically contains 70% nickel, 14-17% chromium, 2.25-2.75% titanium, 0.7-1.2% aluminum, and small amounts of other elements such as iron, niobium, and manganese.
Properties:
- Strength: Inconel X-750 is known for its excellent strength at high temperatures up to 704°C (1300°F).
- Heat Resistance: It retains its strength and oxidation resistance at elevated temperatures.
- Applications: Commonly used in gas turbines, rocket engines, nuclear reactors, pressure vessels, and springs where high strength at elevated temperatures is required.
Inconel 625
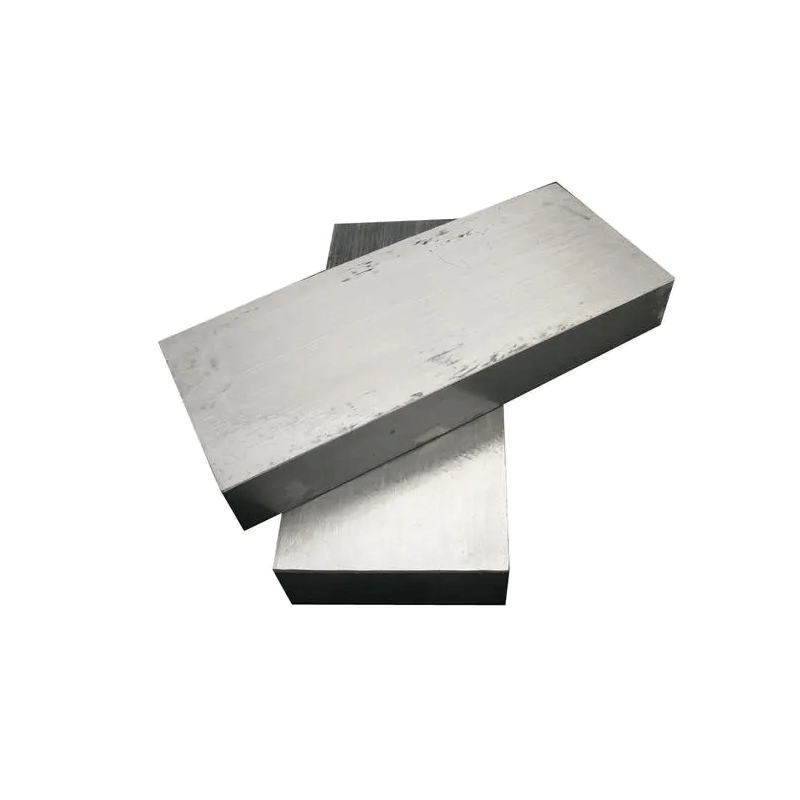
Composition:
- Inconel 625 is a solid-solution nickel-chromium alloy strengthened by the addition of molybdenum and niobium.
- It typically contains 58% nickel, 20-23% chromium, 8-10% molybdenum, 3.15-4.15% niobium (columbium), and smaller amounts of iron, tantalum, silicon, and aluminum.
Properties:
- Corrosion Resistance: Inconel 625 is highly resistant to corrosion and oxidation in a wide range of severe environments, including seawater and chemical processing.
- Strength: It offers good strength and toughness at both cryogenic and high temperatures (up to 1093°C or 2000°F).
- Applications: Used in marine applications, chemical processing equipment, aerospace and defense components, and pollution control systems.
Comparison
- Strength and Temperature Resistance:
- Inconel X-750 has superior strength at high temperatures compared to Inconel 625. It is specifically designed for applications where high strength is crucial at temperatures up to 704°C (1300°F).
- Corrosion Resistance:
- Inconel 625 has better corrosion resistance compared to Inconel X-750, particularly in harsh environments involving acids, seawater, and oxidation.
- Applications:
- Inconel X-750 is used in applications where high strength at elevated temperatures is critical, such as gas turbines, rocket engines, and nuclear reactors.
- Inconel 625 finds applications where corrosion resistance is paramount, including marine environments, chemical processing, and aerospace components.
Conclusion
Choosing between Inconel X-750 and Inconel 625 depends largely on the specific requirements of the application. If high strength at elevated temperatures is the primary consideration, Inconel X-750 is preferred. For applications requiring superior corrosion resistance across various environments, Inconel 625 is the better choice. Both alloys represent advanced materials engineering solutions for demanding industrial and aerospace applications.