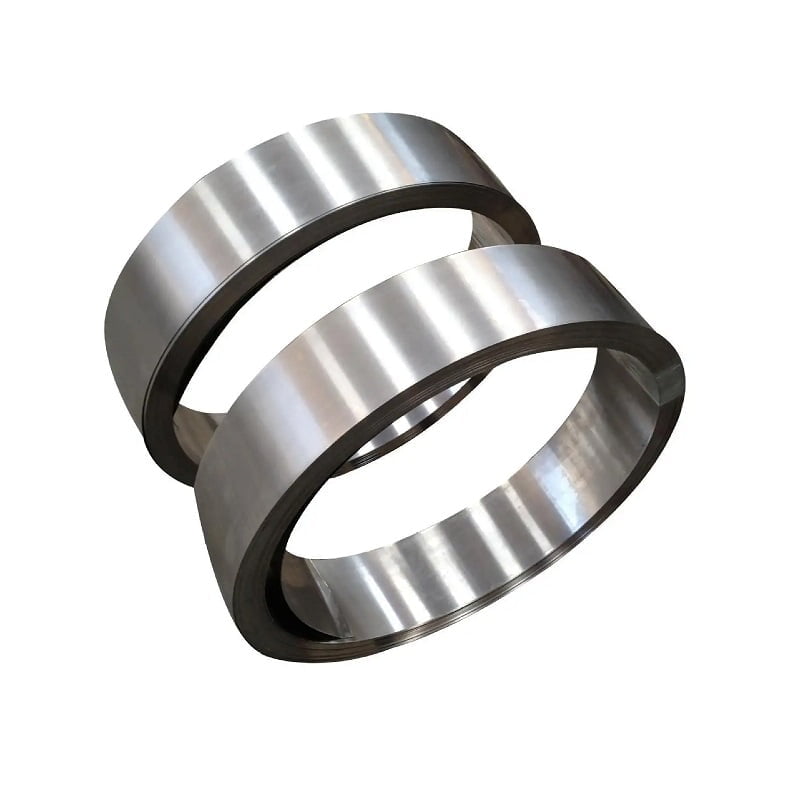
NIMONIC and INCONEL are highly regarded nickel-based superalloys commonly utilized across various industries for their exceptional performance characteristics. Key aspects of these alloys include:
- Composition: Both alloys are primarily composed of nickel, but they differ in the amounts of chromium, molybdenum, and other elements, impacting their performance.
- Mechanical Properties: They exhibit high strength and good ductility, but their specific properties vary, influencing their suitability for different applications.
- Corrosion and Oxidation Resistance: Both alloys excel in resisting corrosion and oxidation, but INCONEL is particularly noted for its versatility in aggressive environments.
- Applications: NIMONIC is often used in aerospace applications, while INCONEL finds extensive use in chemical processing and marine environments.
- Fabrication and Workability: The workability of these alloys varies, with INCONEL being generally easier to process.
Composition
Alloy | Nickel (Ni) | Chromium (Cr) | Iron (Fe) | Molybdenum (Mo) | Cobalt (Co) | Titanium (Ti) | Aluminum (Al) |
---|---|---|---|---|---|---|---|
NIMONIC | 63-70% | 15-20% | Bal. | 1-3% | 8-11% | 3-4% | 0.2-0.5% |
INCONEL | 58-72% | 14-22% | Bal. | 2-10% | 3-8% | <1% | 0.2-1% |
Mechanical Properties
Property | NIMONIC 80A | INCONEL 625 |
---|---|---|
Density | 8.4 g/cm³ | 8.44 g/cm³ |
Tensile Strength (Room Temp) | ~1000 MPa | ~827 MPa |
Yield Strength (Room Temp) | ~800 MPa | ~690 MPa |
Operating Temperature Range | Up to 1000 °C | Up to 1000 °C |
Elongation (at fracture) | 30% | 48% |
Corrosion and Oxidation Resistance
Alloy | Description |
---|---|
NIMONIC | Superior oxidation resistance at high temperatures, ideal for turbine components in aerospace. |
INCONEL | Excellent corrosion resistance in a wide range of reactive environments, making it suitable for aggressive chemical processing industries. |
Applications
Industry | NIMONIC Applications | INCONEL Applications |
---|---|---|
Aerospace | Turbine blades, combustion chambers | Exhaust systems, structural components |
Power Generation | Gas turbines, heat exchangers | Steam generator tubing, nuclear reactor components |
Oil and Gas | Downhole tubulars, refinery components | Oil and gas production machinery, pipelines |
Chemical Processing | Reactors, heat exchangers | Chemical processing equipment, valves, and fittings |
Marine Applications | Not commonly used | Offshore oil rigs, marine applications |
Fabrication and Workability
Alloy | Fabrication Techniques | Workability |
---|---|---|
NIMONIC | Welding, machining, casting | Moderate – can be challenging to machine due to high strength. |
INCONEL | Welding, machining, formability | Good – offers excellent welding characteristics and can be easily formed. |
Advantages
Alloy | Advantages |
---|---|
NIMONIC | – Excellent high-temperature strength |
– Superior oxidation resistance | |
– Designed for high-stress applications | |
INCONEL | – Excellent corrosion resistance in reactive environments |
– Good mechanical properties across a wide temperature range | |
– Versatile applications in various industries |
Differences
Feature | NIMONIC | INCONEL |
---|---|---|
Primary Focus | High-temperature applications, especially in aerospace and gas turbines. | Corrosion resistance across various industries. |
Composition Variability | Higher cobalt and titanium for improved high-temperature strength. | A broader range of grades designed for different applications. |
Workability | Harder to machine due to higher strength. | Generally easier to fabricate and weld. |
This comparative analysis provides a clear overview of the distinctions and similarities between NIMONIC and INCONEL, helping to identify which alloy may be more suitable for specific engineering applications.