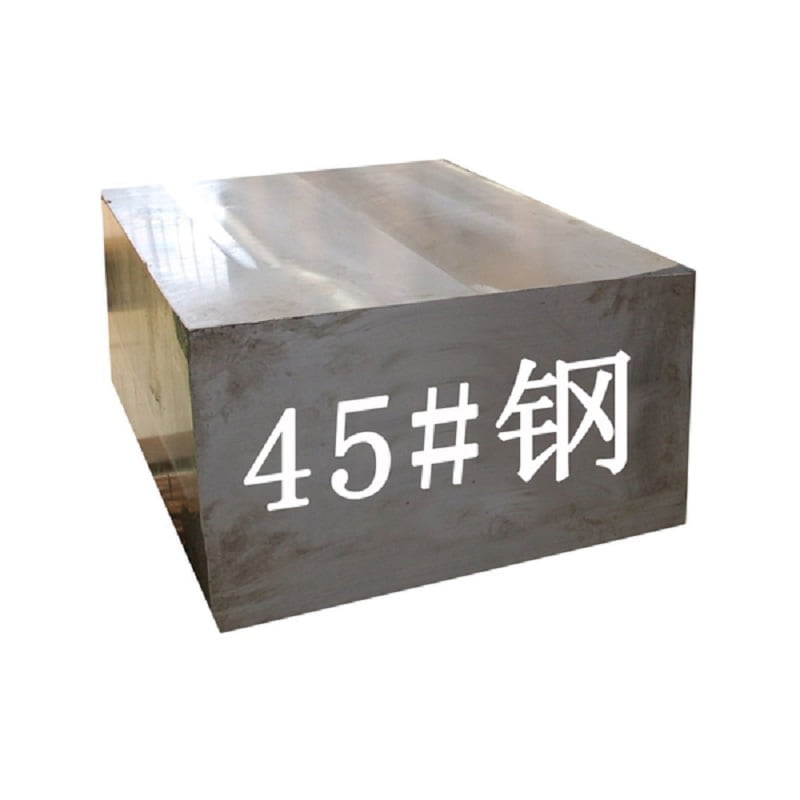
Introduction
S45C and 42CrMo4 are two grades of carbon and alloy steel widely used in various engineering and manufacturing applications. This article provides a thorough comparison of these two materials, focusing on their chemical compositions, mechanical properties, heat treatment responses, applications, and their respective advantages and disadvantages.
Chemical Composition
The chemical composition of both S45C and 42CrMo4 is vital in determining their mechanical properties and overall performance.
Element | S45C Composition (%) | 42CrMo4 Composition (%) |
---|---|---|
Carbon (C) | 0.42% – 0.48% | 0.38% – 0.45% |
Manganese (Mn) | 0.60% – 0.90% | 0.60% – 0.90% |
Chromium (Cr) | – | 0.90% – 1.20% |
Molybdenum (Mo) | – | 0.15% – 0.30% |
Phosphorus (P) | 0.03% max | 0.03% max |
Sulfur (S) | 0.03% max | 0.03% max |
Explanation of Chemical Composition
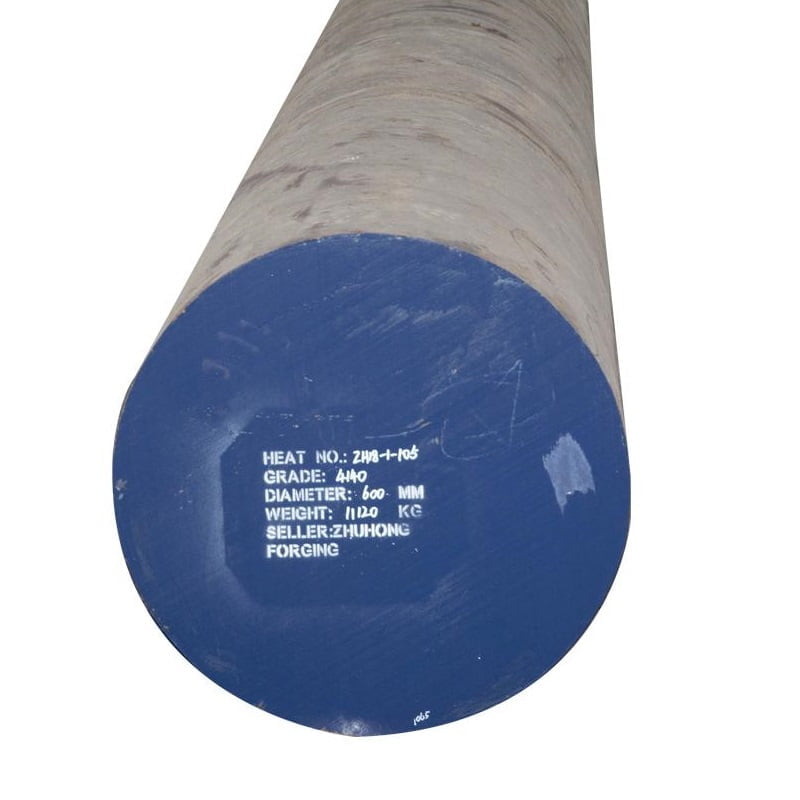
- Carbon (C): S45C has a slightly higher carbon content than 42CrMo4, contributing to its properties. Higher carbon content typically enhances hardness and strength.
- Chromium (Cr) and Molybdenum (Mo): 42CrMo4 contains chromium and molybdenum, which improve hardness, corrosion resistance, and toughness, making it suitable for dynamic and high-stress applications.
- Manganese (Mn): Both grades have similar manganese content, which aids in deoxidation and improves hardenability.
Mechanical Properties
Mechanical properties play a critical role in determining performance under load and stress.
Property | S45C | 42CrMo4 |
---|---|---|
Yield Strength (MPa) | Approximately 355 MPa | Approximately 600 – 800 MPa |
Tensile Strength (MPa) | 570 – 700 MPa | 700 – 900 MPa |
Elongation (%) | 14% (minimum) | 12% (minimum) |
Hardness (HB) | 170 – 210 HB | 250 – 300 HB |
Detailed Explanation of Mechanical Properties
- Yield Strength: 42CrMo4 has a significantly higher yield strength than S45C, making it more suitable for high-stress applications.
- Tensile Strength: Similarly, the tensile strength of 42CrMo4 surpasses that of S45C, indicating better load-bearing capacity.
- Elongation: S45C has better elongation properties, allowing it to undergo more plastic deformation compared to 42CrMo4.
- Hardness: 42CrMo4 is generally harder than S45C, contributing to its wear resistance and durability.
Heat Treatment Responses
The heat treatment process can influence the mechanical properties of both grades.
Heat Treatment Type | S45C | 42CrMo4 |
---|---|---|
Quenching | Suitable for hardening | Suitable for hardening |
Tempering | Reduces brittleness while maintaining strength | Improves toughness while enhancing hardness |
Explanation of Heat Treatment
- Quenching: Both materials can be quenched to increase hardness, but 42CrMo4 tends to achieve greater hardness due to its alloying elements.
- Tempering: Tempering is essential after quenching to relieve stresses. Both materials benefit from tempering, with 42CrMo4 enhancing toughness while retaining hardness.
Applications
S45C and 42CrMo4 are utilized in a variety of applications depending on their properties.
Application | S45C | 42CrMo4 |
---|---|---|
Gears | Commonly used | Used in high-stress gears |
Shafts | Suitable for general use | High-performance shafts |
Machine Parts | General engineering parts | Critical components requiring high strength |
Tools | Not commonly used | Applicable for cutting tools and dies |
Automotive Components | Often used | Commonly used in axles and crankshafts |
Explanation of Applications
- S45C: Its good machinability and balanced properties make it appropriate for general engineering applications.
- 42CrMo4: The alloying elements and high strength make it suitable for dynamic applications, including automotive parts where durability is essential.
Advantages and Disadvantages
Both S45C and 42CrMo4 have their specific advantages and disadvantages.
Aspect | S45C | 42CrMo4 |
---|---|---|
Advantages | – Good machinability | – Higher strength and hardness |
– Cost-effective for general applications | – Excellent toughness and fatigue resistance | |
– Balanced properties | – Suitable for high-stress environments | |
Disadvantages | – Lower strength compared to 42CrMo4 | – Higher cost compared to S45C |
– Limited hardness | – More challenging to machine |
Detailed Explanation of Advantages and Disadvantages
- S45C Advantages: Its good machinability and cost-effectiveness make it suitable for various engineering applications.
- S45C Disadvantages: The lower strength and hardness may limit its effectiveness in high-stress applications.
- 42CrMo4 Advantages: The enhanced strength, toughness, and resistance to fatigue make it ideal for demanding applications.
- 42CrMo4 Disadvantages: Increased hardness can complicate machining processes, and its cost is higher compared to S45C.
Conclusion
Choosing between S45C and 42CrMo4 depends on the specific requirements of the application. S45C is appropriate for general engineering use, offering a balance of strength and machinability, while 42CrMo4 is favored for its high strength, toughness, and suitability in dynamic applications. Understanding their differences in chemical composition, mechanical properties, heat treatment responses, and applications will assist engineers and manufacturers in making informed material selections tailored to their project needs.