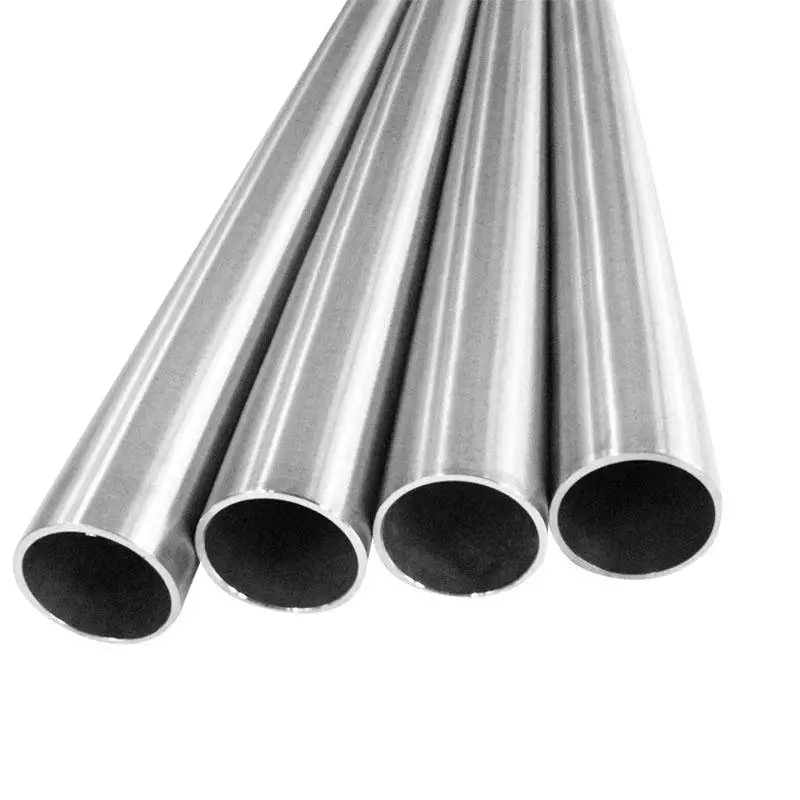
In the challenging world of oil and gas exploration and production, where extreme conditions are the norm rather than the exception, the choice of materials can make the difference between success and failure. At the forefront of this materials revolution stand nickel-based alloy pipes, the unsung heroes of the petroleum industry. These remarkable engineered solutions have become indispensable in an industry where corrosive environments, high temperatures, and immense pressures are everyday challenges.
As we delve into the world of nickel-based alloy pipes, we’ll uncover the unique properties that make them essential, explore their diverse applications across the oil and gas sector, and understand why engineers and industry leaders consistently turn to these high-performance materials. From the depths of offshore drilling to the intricacies of refinery operations, nickel-based alloy pipes are silently revolutionizing how we extract, transport, and process one of the world’s most valuable resources.
Join us on this journey as we explore the science, engineering, and practical applications behind these crucial components of modern oil and gas infrastructure. Whether you’re an industry professional seeking to expand your knowledge or a curious reader interested in the technological marvels that power our energy-dependent world, this comprehensive guide to nickel-based alloy pipes in the oil industry promises to be both informative and enlightening.
- 소개
Nickel-based alloy pipes play a crucial role in the oil and gas industry. These high-performance materials maintain excellent properties under extreme conditions, making them indispensable components in oil extraction and transportation processes. This article will provide a detailed introduction to the characteristics, applications, main types, and selection considerations of nickel-based alloy pipes used in the oil industry. - Characteristics of Nickel Alloy Pipes
The widespread use of nickel alloy pipes in the oil industry is primarily due to their outstanding physical and chemical properties. The following table summarizes the key characteristics of nickel alloy pipes:
특성 | 설명 | English Term |
---|---|---|
내식성 | Excellent resistance to acids, alkalis, and saltwater corrosion | 내식성 |
고온 성능 | Maintains strength and stability in high-temperature environments | 고온 성능 |
Mechanical Strength | Excellent tensile and compressive strength | Mechanical Strength |
용접성 | Good welding properties, facilitating installation and maintenance | 용접성 |
내마모성 | Ability to resist wear and erosion | 내마모성 |
Low Thermal Expansion Coefficient | Maintains dimensional stability during temperature changes | Low Thermal Expansion |
- Applications in the Oil Industry
Nickel alloy pipes have a wide range of applications in the oil industry, including:
Drilling Equipment:
- Drill Pipes
- Casing
- Tubing
Production Equipment:
- Christmas Trees
- Safety Valves
- Separators
Transportation Systems:
- Oil Pipelines
- Subsea Pipelines
Refinery Equipment:
- 열교환기
- Reactors
- Distillation Columns
- Major Nickel Alloy Types
There are various types of nickel alloy pipes commonly used in the oil industry, each with specific properties and applications. The following table lists some of the main nickel alloy types and their characteristics:
Alloy Name | Main Components | 특징 | 주요 응용 프로그램 |
---|---|---|---|
인코넬 625 | Ni-Cr-Mo | Excellent corrosion resistance, high strength | Offshore oil platforms, chemical processing equipment |
인콜로이 825 | Ni-Fe-Cr | Good resistance to chloride stress corrosion cracking | Acidic oil and gas wells, seawater treatment systems |
하스텔로이 C-276 | Ni-Mo-Cr | Superior resistance to various corrosive environments | High-temperature and high-pressure wells, acid gas processing |
모넬 400 | Ni-Cu | 우수한 해수 부식 저항 | Seawater cooling systems, desalination equipment |
Alloy 20 | Ni-Cr-Cu | Good resistance to sulfuric acid corrosion | Sulfuric acid processing equipment, phosphoric acid production |
- Selection Considerations
When selecting appropriate nickel alloy pipes for oil applications, several factors need to be considered:
Operating Environment:
- 온도 범위
- Pressure Conditions
- Corrosive Media
Mechanical Property Requirements:
- 힘
- 인성
- Fatigue Performance
Economic Factors:
- 초기비용
- Life-Cycle Cost
- Maintenance Requirements
Regulations and Standards:
- Industry Standards
- Environmental Regulations
- Safety Requirements
- Manufacturing and Processing
The manufacturing and processing of nickel alloy pipes significantly impact their final performance. The main manufacturing methods include:
Seamless Pipe Manufacturing:
- Hot Extrusion
- 냉간 인발
Welded Pipe Manufacturing:
- Longitudinal Welding
- Spiral Welding
열처리:
- 가열 냉각
- 용액 처리
Surface Treatment:
- Pickling
- Passivation
- Quality Control and Inspection
To ensure that nickel alloy pipes meet the strict requirements of the oil industry, comprehensive quality control and inspection are necessary:
Inspection Method | 목적 | English Term |
---|---|---|
초음파 테스트 | 내부 결함 감지 | Ultrasonic Testing (UT) |
방사선 촬영 테스트 | Check weld quality | Radiographic Testing (RT) |
Magnetic Particle Inspection | Detect surface and near-surface defects | Magnetic Particle Inspection (MPI) |
Chemical Composition Analysis | Verify material composition | Chemical Composition Analysis |
Mechanical Property Testing | Confirm strength and toughness | Mechanical Property Testing |
Corrosion Resistance Testing | Evaluate corrosion resistance capability | Corrosion Resistance Testing |
- 결론
Nickel-based alloy pipes play a key role in the oil and gas industry due to their excellent performance. Through proper selection and correct use of these high-performance materials, equipment reliability and lifespan can be significantly improved, maintenance costs reduced, and safe operations ensured in extreme environments. As oil extraction technologies continue to advance and environmental requirements become increasingly stringent, nickel alloy pipes will continue to play an important role in the industry and may lead to the development and application of more innovative alloys.