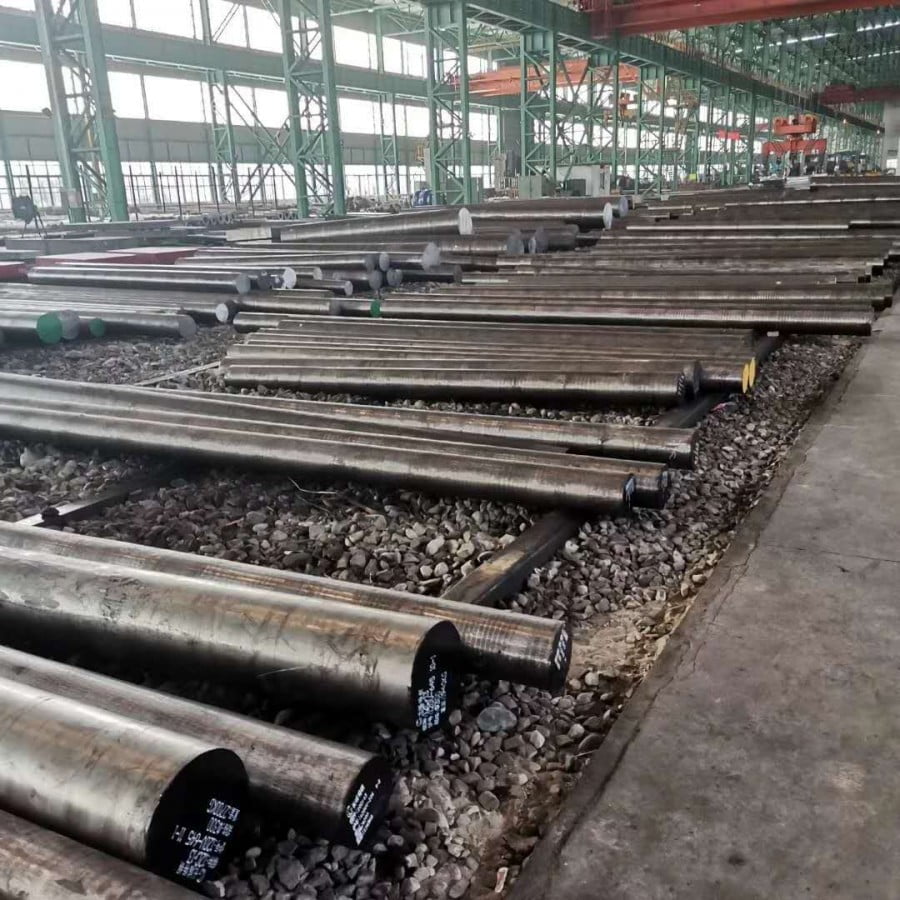
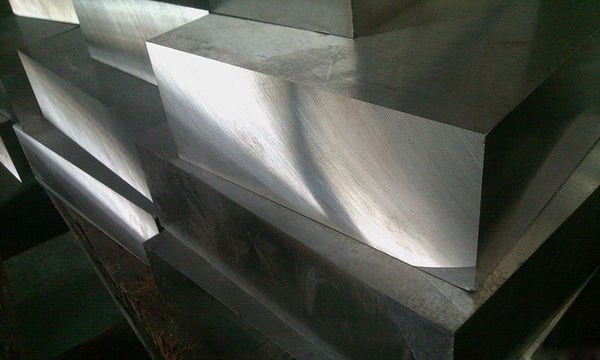
So, why does Cr12MoV mold steel crack after heat treatment? What are the reasons for this?
Causes of Cr12MoV cracking after heat treatment:
1. During the heat treatment of the Cr12MoV mold steel, the workpiece was not preheated, and the heating speed was too high, resulting in heating cracking.
2. When Cr12MoV mold steel is cooled, it cools quickly below MS temperature and the stress is too large; Or quenching heating temperature is too high, coarse grain, brittleness, over burning grain boundary oxidation or melting, resulting in material cracking.
3, raw materials exist mesh eutectic carbide or spheroidizing annealing, or raw materials have microscopic cracks, quenching crack expansion cracking may.
4. Cr12MoV mould steel is not tempered in time after quenching, which is also a reason for cracking of Cr12MoV mould steel during heat treatment.
5. The plane size of the workpiece is too large, leading to uneven heat treatment of the steel of the Cr12MoV mould, or containing impurities, unqualified flaw detection, or excessive concentration of stress in some places, leading to cracking.
The above is the summary of Lion Metal about “why Cr12MoV material cracks after heat treatment”.In fact, the heat treatment process and the heat treatment operation specification are the most likely causes of cracking of Cr12MoV mold steel after heat treatment. Therefore, attention should be paid to its heat treatment.