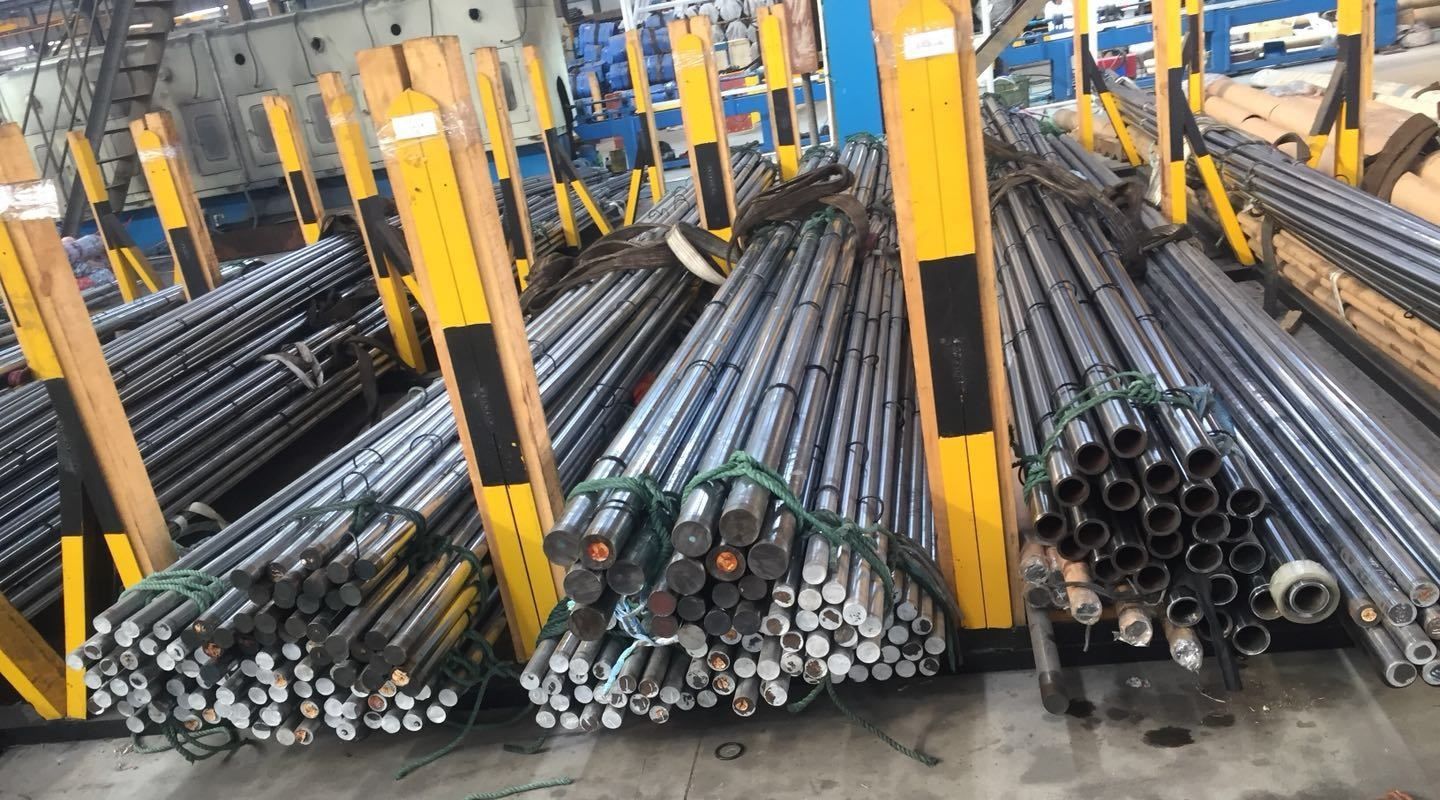
このページのコンテンツは派生しています iqsdirectory.com
導入
これは、オンラインで利用可能なコールドフォーミングの最も包括的なガイドです。
この記事では、次のトピックについて説明します。
- 冷たい鍛造とは何か、そしてそれがどのように機能するか
- Cold forging benefits & disadvantages
- ホットフォーミングとコールドフォーミング
- 使用される金属および機器/機械
- コールドフォーミングアプリケーション
- そしてもっと…
第1章 - コールドフォーミングとは何ですか?それはどのように機能しますか?
Cold forging is a metal shaping & manufacturing process in which bar stock is inserted into a die and squeezed into a second closed die. The process, completed is at room temperature or below the metal‘s recrystallization temperature to form a metal into a desired shape or configuration.
コールドフォージングは、低コストで大量の部品を生産するための効率的で経済的な金属変形プロセスです。温度に応じて異なる3つの方法があります。これは、寒さ、暖かく、または高温であり、ハンマー、ダイ、またはプレスの使用を伴う可能性があります。最終結果はより強力で高品質の製品であるため、コールド鍛造は機械加工や鋳造と混同しないでください。
暖かいまたは熱い鍛造とは異なり、局所的な圧縮力を使用して、室温でのコールドフォーミングの形状と変形はバーのストックを備えています。部品設計の要件に応じて、ワークピースは複数のダイを通過するか、適切な形状を達成するために連続して数回打たれる場合があります。
第2章 - 冷たい鍛造の仕組み
低コストの寒冷鍛造は、人件費の削減と二次処理の削除によるものです。部品は、1時間あたり1000までのレートで迅速かつ効率的に生産され、単位コストが低くなります。生産は、単に金属製の部分を挿入し、機械を迅速かつコスト効果的に作業させることの問題です。
コールドフォーギングの完成品は、下の画像に見られるように、完全な表面仕上げと寸法の安定性が改善されています。さまざまなプロセスは、長持ちする製品または部品を生成するワークピースの強度と耐久性を高めます。
コールドフォーミングプロセス
ステップ1:潤滑剤
- 鍛造の前に、ワークピースは潤滑剤で処理され、変形が250°〜450°の温度を生成できるため、形成プロセス中にダイに固執し、涼しく保つことができます。
ステップ2:金属片を挿入します
- 金属製の部分は、最終部分の形状を持つダイに配置されます。ダイには2つのセクションがあり、1つはハンマーに取り付けられ、もう1つはワークピースの下にあります。ハンマーは、金属片を変形させる力を生成する上部と顕著なメカニズムです。
ステップ3:ストローク
- ワークピース、またはストロークの印象は、油圧、空気圧、または機械的な3つのメカニズムによって生成できます。それぞれの技術は、ハンマーをかぶったシャフトを駆動し、ワークピースに大きな力をかけて、目的の形状を作成します。これは、ミリ秒のスケール内で発生します。場合によっては、正確な輪郭と形状を生成するために、ハンマーを連続して数回落とす必要がある場合があります。
ステップ4:フラッシュ
- フラッシュは、ダイまたはダイのセットの周りにある余分な金属です。それは、鍛造の本体から、死が出会い、トリミング中に除去される薄いプレートとして伸びています。フラッシュは金属の流れを制限し、完全な印象を確保します。フラッシュの存在は、金属にダイを完全に満たすように強制するために不可欠です。
ステップ5:部品削除
- 部品の除去方法は、プロセスのタイプによって異なります。ほとんどの最新のメーカーは、自動化を使用して、コンベアまたはロボットの手で部品を削除します。これは、材料の取り扱いの必要性を排除する別のコスト削減策です。
ステップ6:シェーピング後
- プロセスの他の部分と同様に、これは多くの形をとることができます。 1つのダイと1つのストロークを必要とする部品の場合、部品はトリミングされ、輸送に送られます。複数のファセットを持つ部品の場合、それらは他のダイプロセスに移動して、機能を追加します。駅から駅へのダイの動きは、通常自動化されます。大きな部分では、Hi-Lo、Forklift、またはCraneを含む他の機械化された方法が使用されます。
第3章 - コールドフォーミングの利点
この章で詳細に議論されているコールドバージングには、6つの主な利点があります。それらは次のとおりです:
- 費用対効果
- より速い生産
- 環境に優しい
- 優れた製品パフォーマンス
- 高い生産出力
- 金属の幅広い選択
以下の情報は、コールドフォーミングの利点の一部と、それが非常に広く使用されている理由を概説しています。第3章は、コールドフォーミングとホットフォーミングとそれぞれの利点の比較です。
費用対効果:
コールドフォーミングは、前処理、温度、仕上げの3つの要因により、低コストです。他の金属型の方法では、ワークピースは加熱されるなどの何らかの形の前処理を受ける必要があります。炉、ki、または電気は、通常、その再結晶点を上回る金属の温度を上げるために使用されます。彼らは維持、汚染物質の生産、および時間のかかるのに費用がかかります。
コールドフォーミングでは、ワークピースが処理されると、完了し、最小限の仕上げが必要であり、人件費を節約できます。
コールドフォーゲンは、廃棄物とスクラップがほとんどないため、生産コストの最大70%の物質的な節約があります。
より速い生産:
コールドフォーミングは、ワークピースを鍛造マシンに直接配置して、即座に完成した部品を生成する簡単なプロセスです。現代の生産者は、オートメーションを使用してワークピースをロードし、マスコミから削除します。この図でわかるように、金属は機械に供給され、処理され、先に進みます。入場から終了までの時間は1秒未満です。
環境に優しい:
コールドフォーミングが環境に優しい主な理由は、炉からの煙と煙が著しい炭素排出量を生成するため、熱の必要性を除去することです。また、生産者はエアフィルタリングおよびクリーニング装置を設置する必要がないため、コストも削減されます。
優れた製品パフォーマンス:
Cold Forgingは、最終部品の構成に従うためにワークの粒構造を再配置するため、優れた性能を備えた製品を生産します。
考えられる否定的な反応を排除します:
金属の動作は、さまざまな潜在的な問題を引き起こす可能性があります。コールドフォーミングは、金属の全体的な強度を高め、材料の完全性の損失のリスクを除去することにより、多孔性疲労などの負の影響の一部を排除します。
質と長寿命の向上:
コールドフォードされた部品は、高いストレスを処理することができます。ワークピースが収量または弾性の制限を超えて強制されている場合、変更された形状を保持することができます。
パーツ公差の保持:
部品の重大で密接な耐性は、生産の実行中に維持されます。それらは、すべての部分が最初の部分の正確な複製であるように、最も細かい詳細に再現されます。
デザインの自由:
他のプロセスとは異なり、コールドフォーミングは、他のプロセスで多くの異なる費用のかかる二次方法を必要とする複雑な輪郭と形状を生成できる設計の自由を可能にします。
高い生産出力:
コールドフォーミング生産方法の間にはバリエーションがあるかもしれませんが、コールドフォージングの製造速度が高いため、1分あたり50個のピースが400を超える可能性があります。プロセスの速度に影響を与える唯一のものは、パーツのサイズです。
金属の幅広い選択:
炭素鋼、合金鋼、ステンレス鋼などの硬い金属、アルミニウム、真鍮、銅などの軟さを含む幅広い金属を鍛造できます。
この画像は、コールドフォーミングによって生成されたボルトのサンプリングです。さまざまなボルトのそれぞれは、別の金属から作られています。銅、真鍮、アルミニウム、鋼で作られたものが含まれています。
第4章 - ホットとコールドフォーミング
熱い鍛造とコールドフォーミングの違いは温度です。室温で金属を冷間鍛造してストレスをかけますが、熱鍛造は融点の近くまたは融点で金属を熱します。
温度範囲の鍵は再結晶です:コールドフォーミングは再結晶前に行われ、ホットフォーミングはその再結晶点の上に金属を加熱します。
コールドフォーミングとホットフォーミングの選択は次のとおりです。
- 製造業者の機器と機械加工:生産者は、あるプロセスまたは他のプロセスを専門として、機器の使用を最大化します。
- 顧客の需要:部品開発の設計段階では、エンジニアは、寒さと熱い鍛造には制限があるため、設計を作成するのに最適なプロセスに関する決定を下します。
- 生成される部品の種類:適切なプロセスの選択に関する制限は、特定の部品はホットできないが、他の部分はコールドフォーミングに最適であるため、部品の設計によって決定されます。コールドフォードパーツのデザインは、複雑なディテールなしでシンプルですが、ホットフォーゲンは非常に正確な小さな分の機能を備えたピースを生成できます。
- 低コストの要件:可能な場合はいつでも、メーカーは、より少ない機器を必要とし、暖房を含めないため、コールドフォーギングを選択します。
熱間鍛造
温度は、700°Cまたは1292°F〜1000°Cまたは1832°Fの間の非常に高い温度で行われます。金属が冷めたら、変形した形状を保持します。形成プロセスでは、油圧、空気圧、および機械的プレスが使用されます。
ホットフォーミングの特性:
死または型:
熱い鍛造の主な費用の1つは、極端な温度に耐えられ、疲労に抵抗し、延性、靭性、引張強度を持つように設計された強化された鋼で作られたダイと金型を生成するために必要なコストです。
ホットフォーミングの形式:
熱い鍛造方法の多くはコールドフォーミングの方法に似ていますが、他の方法にはガス形成、消光、描画形成、等温が含まれます。
金属の温度:
プロセスのタイプは、金属が形作られているときに金属の温度を決定します。一部のプロセスでは、金属が完全に溶けて型に注がれたり、ダイを押したりします。他の人では、それはアニールされ、圧縮と圧力の下でダイまたはカビによって形作られます。
危険な環境要因:
最大の欠点は、暖房プロセスによって生成される汚染物質の量です。これは、最初の産業革命中の創業以来、主要な問題であり、生産者が長年にわたって継続的に直面してきた問題でした。
暖房金属:
部品は再結晶点の上に加熱する必要があります。これは300°Fをはるかに超えており、1000度の学位に入ることができます。適切な温度に達するには、大きな炉またはkiが必要です。
関係する時間:
熱い鍛造の複雑な性質には、金属を加熱し、処理し、冷却するのに時間が必要です。実際のスタンピング、変形、またはシェーピングにはコールドフォーミングとほぼ同じ時間がかかりますが、加熱および冷却プロセスには、長期間にわたって注意深いケアと管理が必要です。
ホットフォーミングの結果:
金属の加熱と冷却は、強度、靭性、延性を高めますが、硬さを低下させます。冷却プロセス中、金属はゆがんで形状を失うことがあります。
スケーリング:
熱い鍛造は酸化を生成し、スケーリングにつながり、金属の表面を変色させ、仕上げが困難になります。
仕上げ:
暖房プロセスから奇形、欠陥、エラーを除去するには、部品を完成させる必要があります。これらの二次操作は労働集約的であり、いくつかのタイプの専門機器が必要です。
コールドフォーミング
鍛造が行われる温度は、コールドフォーミングとホットフォーゲンを分離するものです。部分が熱くなるためには、再結晶ポイントを上回る温度に加熱され、マイクロ構造が変化します。加熱されると、その内部ストレスと強度が排除され、より延性があります。コールド鍛造は、金属がその強度と微細構造を保持できるように加熱する必要はありません。
冷たい鍛造の特徴は次のとおりです。
シェーピングの温度:
金属は、再結晶点より下の室温で形作られます。これは、コストを下げて炉の費用を回避することの利点があります。
スピード:
速度は、低ボリュームマシンでは1分あたり7ピースから、大量のマシンでは1分あたり400個までの範囲です。
装置:
コールド鍛造は、金属を形作り、絞り、曲げ、せん断、描画を含むように設計された機械で行われます。機器は、技術の量とその規模に応じて、幅広い価格で利用できます。
料金:
コスト削減は、材料と速度によるものです。材料の節約は、生産された少量のスクラップから得られます。これは最大70%です。部品は非常に速い速度で生産されるため、ユニットあたりのコストは大幅に低くなります。
環境要因:
Stalcopから以下のこの機械に見られるように、排出量や汚染物質は生成されません。すべてが自己完結型で囲まれています。金属を加熱する必要がないため、炭素やその他の汚染物質は排除されます。
コールドフォーミングの結果:
下の図に見られるように、金属の粒子構造は再配置され、最終的な部分の流れに続いて多孔性疲労を排除し、せん断強度を高め、材料の完全性のリスクを減らします。金属を緊張させることにより、それはより強く、より回復力が高くなります。欠点は、金属が冷たくなると、その延性を失い、より脆くなります。
スケーリング:
金属が鍛造される前に、保管中に発生する可能性のある錆や腐食などのスケーリングを除去することが重要です。解除されていない場合、その部分は熱い鍛造で見られるのと同じ劣化を持ちます。
仕上げ:
仕上げは非常に少ないです。部品が処理されると、使用または発送の準備が整います。
コールドフォーミングの短所
コールドフォーミングは完璧ではありません。生産のすべての方法と同様に、コールドフォーミングには制限と制限があり、次の生産プロジェクトに選択する前に考慮する必要があります。
- 大量のシンプルな形状とデザインのみを生成できます。ユニーク、珍しい、または複雑なパターンは、冷静にすることはできません。変形レベルと形状グレードは限られており、冷たい金属は延性が少なくなります。
- 金属の粒構造の変化は、余分な強度を与えますが、残留応力を生成する可能性があります。
- 冷間鍛造の特定の方法では、亀裂やクリープ硬化を排除するために熱処理が必要です。
- 冷たくなることができる金属の種類には制限があります。延性が低く、緊張硬化に対して感受性がある人は、延性を失い、引張ストレスの下で壊れるため、選択すべきではありません。 RockwellスケールでHRC 44の硬度を持つ金属のみを使用できます。
- 生産プロセスには、必要な圧縮力と圧力を生成するために、大きな力が必要です。油圧と空気圧の追加により、機器のサイズが減少しましたが、機械が消費する電力量を排除していません。
- ツール、ダイ、および金型は、一定の反復力に耐えることができるほど頑丈で強力なものであると同時に特別に設計する必要があります。
第5章 - コールドフォーミングプロセス
さまざまな技術の開発と金属加工における進歩により、いくつかの冷たい金属の形成と形成方法が生成されました。それぞれが異なるアプリケーションを提供しますが、すべては二次仕上げを必要とせずに効率的かつ迅速に製品を生産するように設計されています。
8つの最も一般的なコールドフォーミングプロセスは次のとおりです。
- 曲げ
- 冷間圧延
- 閉じたダイ
- 描画
- 押し出し
- オープンダイ
- リング鍛造
- スワージング
この章の最後で説明するように、リストされているプロセスよりも多くのプロセスがあります。以下の説明は、さまざまな方法を最初に理解するためのデータのベースラインを提供します。
また、コールドフォーミングプロセスの非常に重要な側面は、使用される潤滑剤のタイプです。最も一般的な2つは、リン酸亜鉛または何らかの形のポリマーコーティングです。室温ではコールドフォーミングが行われますが、曲げと形成プロセスは金属の温度を上げます。潤滑剤は、エラーを防ぎ、ワークピースがダイに固執し、ツールの寿命を延ばさないようにすることができます。
潤滑剤メーカーは、各タイプのコールドフォーミングプロセスに合わせてさまざまな製品を提供しています。写真はグラファイト潤滑剤ですが、グラファイトフリーのタイプとアルミン酸カルシウム、フッ化アルミニウム、リン酸塩コーティングが利用できます。
一般的なコールドフォーミング方法:
曲げ -
曲げは、ワークピースがシェーピングツールに対して強制されるプレスとダイを使用して実行されます。また、ピラミッドローリングとも呼ばれ、別のコールドフォーミングプロセスのためにピースを準備するために使用されることもあります。ワークピースは、角度を形成するために単一の軸に沿って緊張しています。
コールドローリング -
ローリングは、圧縮力によって引き起こされる塑性変形のために、金属が回転ローラーのペアを通過する形成プロセスです。圧縮応力は、ロールと金属ストックの表面の間に摩擦を生み出します。一般的に鋼の処理に使用されます。
閉じたダイ -
閉じたダイの鍛造では、ワークピースは、2つのダイの半分の間に配置された後、連続した機械的打撃によって形作られます。ハンマーがワークピースを複数回攻撃するため、一部の生産者は閉じたダイをドロップ鍛造と呼びます。金属が打たれると、それはダイの空洞に流れ込み、それをダイの形に変えます。
描画 -
描画は、ダイの出口で適用された引張強度を使用することにより、ダイを通してワークピースを引っ張っています。ワークが引き抜かれると、断面積が減少し、その長さが増加します。形成された金属は、ローリングによって生成されるよりも寸法耐性が密接になります。
押し出し -
ビレットまたはナメクジは、最終部分のプロファイルを持つ圧縮力の下のダイを強制されます。通過すると、必要な長さにカットされたり、配送用に準備されたり、さらに処理したりします。寒い押出に適用される力は、20,000 kNまたは2007トンに達することがあります。押し出しは、前方、後方、または両方向で行うことができます。
前方の押し出し - 金属はダイを通して前方に押し込まれます。
後方の押し出し - 金属はダイに入り、穴またはカップを形成し、底を側面よりも厚くします。
横方向の押し出し - 力が横方向に横向きに適用され、押し出しの方向に、プロファイルに2番目の特徴を追加します。
オープンダイ:
Open Die Forgingには、事前にカットされたプロファイルなしで2つのフラットダイが含まれます。ワークピースは、いくつかのプロセスを使用して徐々に形成され、幅広い形状とサイズを生成できるようにします。主に、最高の構造的完全性を必要とする大きな金属成分を組み込んだ設計で使用されます。ワークの再配置によって変形が達成されます。
サイジングとも呼ばれる絞り込みは、正確な寸法仕上げを生成する短い距離で力が加えられるオープンダイ処理の一形態です。
リング鍛造 -
リングの鍛造を使用して、ドーナツの形を作るために中央に円形のワークピースがパンチされました。ピアスピースが回転すると、ハンマーされて絞られます。このプロセスは、完全な直径と強度のシームレスなリングを生成します。
スワージング -
スワージング、または放射状の鍛造は、ワークピースの変形であり、2つの部分が一緒に収まるようにします。自動化されており、信頼性が高くなります。 2種類のスワージングは、チューブとラジアルです。チューブスワージングは、ワークピースがダイを強制される押出のようなものです。ラジアルスワージングを使用すると、ハンマーは2つ以上のダイを通してワークピースを強制します。
コールドフォーギングメーカーの検索を開始すると、ここで説明する7つよりも多くの方法が見つかります。可能な方法のいくつかを基本的に理解することは、プロデューサーに信頼的かつ知的に話すだけでなく、彼らの言語を解釈できるようにするのに役立ちます。
他の最新の生産方法と同様に、新しい技術と方法が発展するにつれて、コールドフォーミングが成長していることがわかります。重要な要因は、自動化とロボット工学の追加であり、業界の顔を急速に変化させています。鍛造スペシャリストは、あなたのニーズに最適なプロセスを見つけるために、あなたを正しい方向に向けることができます。
第6章 - コールドフォーミング機器と機械
コールドフォーギング機器と機械には、油圧、空気圧、および機械的な3種類があります。一部のサプライヤーは1つのタイプに特化していますが、大半に価格と操作の種類に応じていくつかの選択肢があることがわかります。テクノロジーと自動化は、以下の写真で見ることができるように一般的です。これは、Marvel Machineryのサーボコールドフォーミングプレスです。パーツデザインレンダリングは、CADなどのエンジニアリングソフトウェアを使用して作成されます。
コールドフォーミングに使用するためには、機械が満たさなければならない要件があります。
- 力 - コールドフォーミングプロセスは、膨大な量の力に依存します。それに関連する機器は、その力を吸収して消散させることができなければなりません。
- バランス - マシンは、振動を減らし、パフォーマンスを向上させるために、静的かつ動的に質量のバランスをとる必要があります。
- 長期にわたる持久力 - コールドフォーミングの方法に関係なく、それぞれに強力な繰り返しの力が必要です。マシンが持続するには、その力に耐えることができなければなりません。
- 複数の操作 - ヘッダーと呼ばれる最新のコールドフォーミングまたはフォーミングマシンは、1つのプロセス中に1つから複数の操作を完了します。これは、1つのストロークで実行できる量の変形が限られているため、必要です。
コールドフォーミング機器の種類:
油圧ダイフォーミングハンマー -
油圧ダイの鍛造ハンマーは、最低投資で最大の力を提供するように設計されています。さまざまなダイから幅広いインプレッションを生み出すことができます。非圧縮性液体がシリンダーに含まれている油圧のエンジニアリング概念を使用して動作します。液体がピストンによって圧縮されると、ダイが取り付けられたシャフトがワークピースに駆動されます。
スクリュープレス -
スクリュープレスは、プレス速度が遅いため、大きな変形に使用されます。フラッシュレスのダイとロングロッドの鍛造に使用できます。スクリュープレスの構成により、曲げや最終鍛造を含むシングルスロットダイに使用できます。電気モーターは、ダイをワークピースに押し込むネジを回す電力を提供します。
Cフレーム高速プレス -
Cフレーム設計は、形成、パンチング、曲げ、およびマルチプレッシング操作に適しています。それらは、110〜400トンのパンチ力と110〜280 mmのスライドストロークを備えたシングルまたはダブルクランクデザインで提供されます。 435〜600 mmの高さを受け入れることができ、小さな部品を生産するために使用できます。
空気圧パワープレス -
空気圧駆動のプレスは、ダイプレス機能の全範囲をカバーできます。それらは、空気圧で動作した操作摩擦クラッチとブレーキを備えています。プレスの電力は、ピストンを備えたシリンダーの空気圧により、鍛造ハンマーをワークピースに押し下げる空気圧縮機によって生成されます。
メカニカルコールドプレス -
品種のコールドフォーミングマシンのうち、必要な力を供給するために非常に大きくする必要があるため、機械式バージョンは最も使用されていません。彼らはモーターからエネルギーを蓄えるフライホイールを持っています。フライホイールがアクティブになると、ハンマーまたはラムをダイに押し下げます。いくつかの回転にわたって電力を供給することができますが、サイクルを継続する前にモーターから電力を取り戻すためにアイドル状態にする必要があります。
多くの品種のコールドフォーミング装置のうち、最も一般的なタイプは、油圧と空気圧です。なぜなら、それらはより少ない部屋を占有し、さまざまな量の力を供給し、プログラム可能であるためです。生産の選択肢を調べるとき、生産者が最新の機器を持っている機器の種類を知るのが最善です。
第7章 - 鍛造金属の種類
Cold Forgingは、プロジェクト用の金属を選択しているときに幅広い選択肢を提供します。さまざまな品種には、炭素鋼、合金鋼、ステンレス鋼などの硬い金属が含まれます。アルミニウム、真鍮、銅、シリコン、マグネシウムは、使用できる柔らかい金属です。金属の1つの要件は、ロックウェルスケールで44 HRC以下の硬度があることです。
銅 -
銅は非常に延性があり順応性があるため、コールドフォーゲン剤に優れた金属です。それはほとんど力で形を付けたり、曲げたり、引っ張ったりすることができ、腐食と錆の耐性のある部分を生成することができます。
アルミニウム -
アルミニウムは、密度が低い非常に軽い非鉄金属です。融解温度は1220°Fで、錆と耐食性の柔軟性と同様に順応性があります。
炭素鋼 -
炭素鋼は鉄と炭素の合金です。さまざまなグレードは、鉄と混合された炭素の量に依存します。並外れた強度と延性があります。
ステンレス鋼 -
ステンレス鋼は、耐食性、外観、強度に最も使用される金属の1つになりました。ステンレス鋼という用語は一般に、その特性を持つ鋼鉄を記述するために使用されますが、ステンレス鋼はその合金含有量に応じてさまざまなグレードで提供されます。
コールドフォーミングに使用される鋼
0.1%から0.25%の炭素含有量の低い炭素鋼。コールドフォーミングは、鋼のひずみ硬化を改善し、オーステナイト化、消光、またはアニーリングの必要性を除去します。
コールドフォーミングに適した金属
適切な合金 | 冷たい形成性特性 |
---|---|
銅 | 素晴らしい |
金、銀、およびそのほとんどの合金 | 素晴らしい |
ブラスカートリッジブラス | 良い |
プラチナ、パラジウム、タンタル、およびその合金 | ほとんどは冷たい形式です。 |
チタンとその合金 | ゆっくりと延性のある純粋なTiおよび合金、はい、6-4のような合金はホットヘッドのみです。 |
ニッケルとその合金 | 純粋なniはい、室温伸びが20%以上の合金です。はい。 |
鉄と鋼 | 純粋な鉄、はい。鋼は、鋼に依存します。多くは冷たい形式です。 |
考慮事項メタルを選択する際の:
プロジェクトのために金属を決定しているときにできる最も論理的で重要なことは、研究を行うことです。各タイプの金属は、さまざまな方法で可塑化と変形に反応します。選択した金属は、最終的な使用と必要な強度に適合する必要があります。鍛造専門家と相談すると、正しい選択をすることを導くことができる貴重な情報を得ることができます。
第8章 - コールドフォーミングアプリケーション
コールドフォーミングは、高度な寸法精度と構造的な正確性を備えたあらゆるサイズの形状を生成します。コールドフォージングの経済効率と速度により、最も人気のある生産の代替手段になりました。
コールドフォーミングは、現代産業の要求に応えます。
- 原材料の使用を最大化する:あらゆる操作の重要な投資は原材料です。コールドフォーミングプロセスの無駄は非常に限られています。フラッシュとトリムは製造プロセスに戻すことができます。
- コストの削減:部品が急速に生産されるため、ユニットあたりのコストは非常に低く、最終製品の収益性が高く、生産に安価です。
- 高品質の部品を生産する:コールドフォーミングは、部品と製品の強度と耐久性を高め、それらが長持ちすることを保証します。形状の作品の構造と特性は、優れた次元の精度を提供しても変化しません。
コールド鍛造部品が使用されるアプリケーション:
自動車 -
高強度、信頼性、品質、および手頃な価格のコールドフォーギングにより、自動車製造にとって非常に魅力的になりました。コールドフォード部品は、優れた衝撃耐性のため、高ストレスポイントに設置されています。ドライブトレイン、ドライブシャフト、ストラットやショックなどのコンポーネントは冷たくなります。以下の図は、コールドフォーギングによって生産される車の伸びの一部の一部の表示です。
ハンドツールとハードウェア -
爪、ボルト、リベット、ナッツなどのコネクタは、長年の冷たい鍛造によって生成されてきました。低い許容範囲と優れた寸法精度は、ハンドツールの生産者が機械加工などの他の方法よりもコールドフォーミングを好む理由です。
軍隊 -
軍は軍事ハードウェアに関して非常に厳しい規定を抱いており、シェルケース、弾丸、その他の軍事ハードウェアを製造するためにコールドフォーゲンを選択します。部品は、危機の時期に高い信頼性とパフォーマンスを持っています。耐性と部品の強さは、軍事兵器に最適です。
ギアの生産 -
コールドフォーギングは、ギアの形成を切断する必要性を排除するため、ギアの生産に使用されます。ギアは、50 mm未満のビレットから生産するか、コイルドワイヤを使用して形作られます。残留ストレスを除去し、硬化を加工するためには、一部のアニーリングが必要になる場合があります。冷たい鍛造ギアの重要な利点は、彼らがどれほどスムーズかつ静かにメッシュしているかです。
結論
- コールドフォーミングは、非常に低コストと大量の高度で、耐性が低く、高次元精度を備えた金属を生成します。
- コールドフォーミングは、すぐに利用可能な完成した部品を迅速かつ迅速に作成します。
- メーカーは、最新および技術的に高度な機器を使用して必要な部分を正確かつ正確に生産するための幅広い選択のプロセスを提供します。
- 硬化鋼やステンレス鋼から銅やアルミニウムまでプロジェクトを完了するために、幅広い金属を選択することができます。
- あなたの車のリベット、ギア、作業ツールに耐えるストレスから生産できる製品の数には、ほとんど制限がありません。
- 冷たい鍛造と熱い鍛造を比較すると、コールド鍛造には時間が少なく、より長くて長持ちする部品と製品が生成されることがわかります。