42CrMo4 and 4140 are essentially the same grade according to different international standards. Here’s the breakdown:
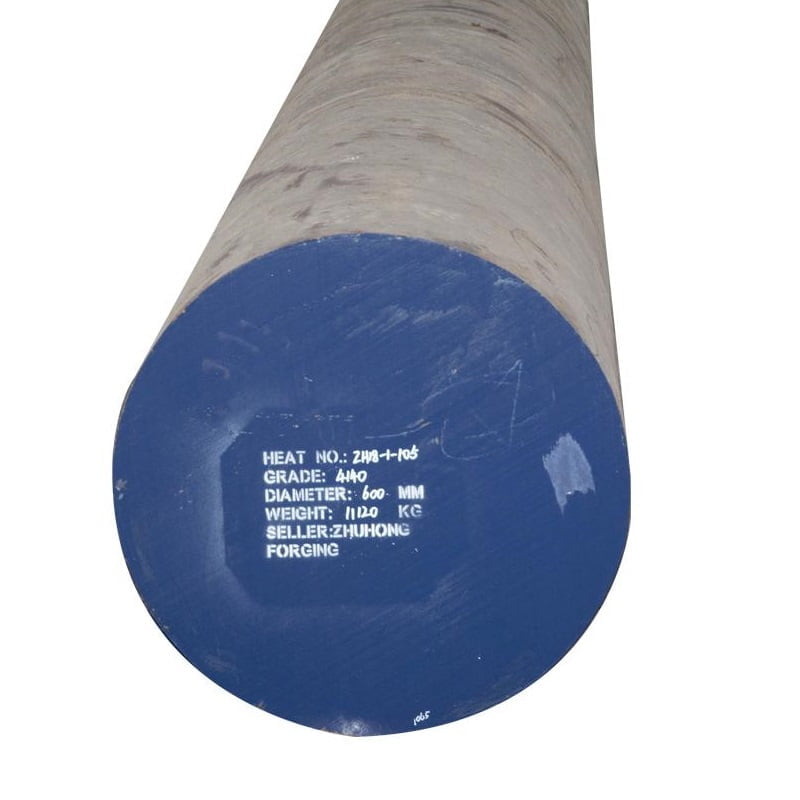
- 42CrMo4: This is the European (EN) designation for the same steel alloy as AISI 4140 steel. In Europe, the alloy is typically known by its EN designation “42CrMo4” or its British BS 708M40 designation.
- 4140: This is the AISI (American Iron and Steel Institute) designation for a chromium-molybdenum steel (AISI 41xx series steel). Specifically, AISI 4140 is a low alloy steel containing chromium and molybdenum as strengthening agents.
Key Points:
- Composizione chimica: Both 42CrMo4 and 4140 steel have similar chemical compositions, with slight variations depending on the exact specifications and standards (such as EN or AISI).
- Applicazioni: They are both commonly used for a variety of applications where high strength and good toughness are required, such as in automotive, oil and gas, and mechanical engineering industries.
- Equivalent Standards: While they are essentially the same material, they are named differently due to being standardized by different organizations (EN and AISI). Manufacturers and users often choose one designation based on their location and the standards they follow.
In summary, 42CrMo4 and 4140 refer to the same steel alloy, with 42CrMo4 being the designation in the European standard and 4140 being the designation in the AISI/SAE standard. Both are widely used and interchangeable in many applications.
International Standards and Availability
While 42CrMo4 is more commonly recognized in Europe and 4140 in North America, both alloys are internationally recognized and available globally. Manufacturers and engineers can choose between these designations based on regional standards or specific project requirements, with the assurance of comparable performance and properties.
Conclusione
In summary, 42CrMo4 and 4140 are two designations for the same alloy steel, differing only in their naming conventions based on regional standards. They share similar chemical compositions and mechanical properties, making them interchangeable in many applications across various industries. Their high strength, toughness, and versatility in heat treatment make them indispensable in manufacturing components that require durability and reliability under demanding conditions. Whether in automotive, aerospace, or construction sectors, these alloys continue to play a vital role in modern engineering, ensuring the integrity and performance of critical components worldwide.