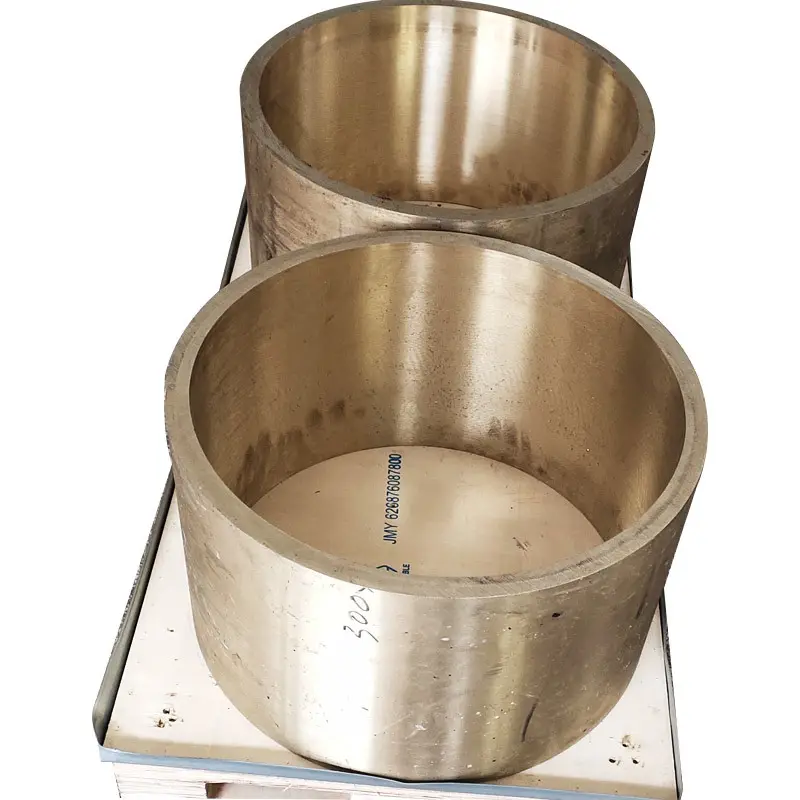
introduzione
Aluminum bronze pipes have gained significant popularity in various industries due to their exceptional combination of strength, corrosion resistance, and durability. This comprehensive guide explores the characteristics, applications, manufacturing processes, and maintenance of aluminum bronze pipes, providing valuable insights for engineers, procurement specialists, and industry professionals.
Composition and Properties
Aluminum bronze pipes are copper-based alloys containing aluminum as the primary alloying element. The addition of aluminum significantly enhances the material’s properties, making it suitable for demanding applications.
Composizione chimica
The typical composition of aluminum bronze pipes varies depending on the specific grade. Here’s a table showing the composition of common aluminum bronze alloys used for pipes:
Lega | Cu (%) | Al (%) | Fe (%) | Ni (%) | Mn (%) | Other (%) |
---|---|---|---|---|---|---|
C95200 | 86-89 | 8.5-9.5 | 2.5-4.0 | – | – | 00,25 massimo |
C95400 | 85-89 | 10-11.5 | 3.0-5.0 | – | 0.5 max | 00,25 massimo |
C95500 | 78-82 | 10-11.5 | 3.5-4.5 | 4.0-5.0 | 0.5 max | 00,25 massimo |
C95800 | 79-82 | 8.5-9.5 | 3.5-4.5 | 4.0-5.0 | 0.8-1.5 | 00,25 massimo |
Proprietà chiave
Aluminum bronze pipes offer a unique set of properties that make them ideal for various applications:
- Resistenza alla corrosione: Excellent resistance to seawater, brackish water, and many chemicals.
- Molta forza: Superior strength compared to standard copper alloys.
- Resistenza all'usura: Good resistance to abrasion and erosion.
- Conduttività termica: Moderate thermal conductivity, better than stainless steel.
- Antiscintilla: Suitable for use in explosive environments.
- Resistenza al biofouling: Naturally resistant to marine growth.
Applicazioni
Aluminum bronze pipes find applications across various industries due to their unique properties. Here’s a table summarizing key applications:
Industria | Applicazioni |
---|---|
Marino | Seawater piping systems, propeller shafts, pump casings |
Oil & Gas | Offshore platforms, subsea equipment, valve bodies |
Elaborazione chimica | Heat exchangers, reaction vessels, distillation columns |
Produzione di energia | Condenser tubes, cooling water systems, valve components |
Aerospaziale | Hydraulic systems, landing gear components |
Estrazione mineraria | Slurry pipelines, pump components, screening equipment |
Case Study: Seawater Cooling Systems
In a notable application, a coastal power plant replaced its stainless steel seawater cooling pipes with C95800 aluminum bronze pipes. The results were impressive:
- 40% reduction in maintenance costs
- 25% increase in heat transfer efficiency
- Extended system lifespan from 15 to 25 years
Processi di produzione
Aluminum bronze pipes are manufactured using various processes to meet specific requirements:
- Colata centrifuga: Ideal for large diameter pipes with excellent dimensional accuracy.
- Estrusione: Suitable for smaller diameter pipes with consistent wall thickness.
- Continuous Casting: Efficient for high-volume production of standard sizes.
- Welded Fabrication: Custom shapes and sizes for specialized applications.
Quality Control Measures
To ensure the highest quality, manufacturers implement rigorous quality control measures:
- Non-destructive testing (NDT) methods such as ultrasonic testing and radiography
- Chemical composition analysis using spectrometry
- Mechanical property testing including tensile strength and hardness tests
- Dimensional inspections and tolerance checks
Selection Guide
Choosing the right aluminum bronze pipe for your application involves considering several factors:
- Operating Environment: Consider factors like temperature, pressure, and chemical exposure.
- Mechanical Requirements: Evaluate strength, hardness, and wear resistance needs.
- Resistenza alla corrosione: Assess the specific corrosive agents present in the application.
- Considerazioni sui costi: Balance initial costs with long-term performance and maintenance savings.
Comparison with Other Materials
Here’s a comparison table of aluminum bronze pipes with other common piping materials:
Proprietà | Bronzo alluminio | Acciaio inossidabile | Acciaio al carbonio | Rame-Nichel |
---|---|---|---|---|
Resistenza alla corrosione | Eccellente | Bene | Povero | Molto bene |
Forza | Alto | Alto | Moderare | Moderare |
Costo | Alto | Moderare | Basso | Moderare |
Il peso | Moderare | Alto | Alto | Moderare |
Conduttività termica | Moderare | Basso | Alto | Moderare |
Resistenza al biofouling | Eccellente | Povero | Povero | Bene |
Installation and Maintenance
Proper installation and maintenance are crucial for maximizing the performance and lifespan of aluminum bronze pipes:
Installation Best Practices
- Use compatible fittings and gaskets to prevent galvanic corrosion.
- Implement proper support and anchoring to minimize stress on the pipes.
- Follow recommended welding procedures if joining is required.
- Conduct thorough flushing and cleaning before commissioning.
Maintenance Tips
- Regular inspections for signs of wear or corrosion
- Proper cleaning to remove marine growth or scale buildup
- Cathodic protection systems for submerged applications
- Monitoring of water chemistry in cooling systems
Tendenze future
The aluminum bronze pipe industry is evolving with new trends and innovations:
- Advanced Alloys: Development of new aluminum bronze compositions with enhanced properties.
- Additive Manufacturing: Exploration of 3D printing techniques for complex pipe geometries.
- Smart Piping Systems: Integration of sensors for real-time monitoring and predictive maintenance.
- Sustainable Production: Focus on recycling and eco-friendly manufacturing processes.
Conclusione
Aluminum bronze pipes offer a compelling combination of properties that make them ideal for challenging applications across various industries. By understanding their characteristics, manufacturing processes, and selection criteria, engineers and procurement specialists can make informed decisions to optimize performance and cost-effectiveness in their piping systems.
As the industry continues to evolve, aluminum bronze pipes are likely to play an increasingly important role in addressing the demands of modern industrial applications, particularly in corrosive and high-stress environments.