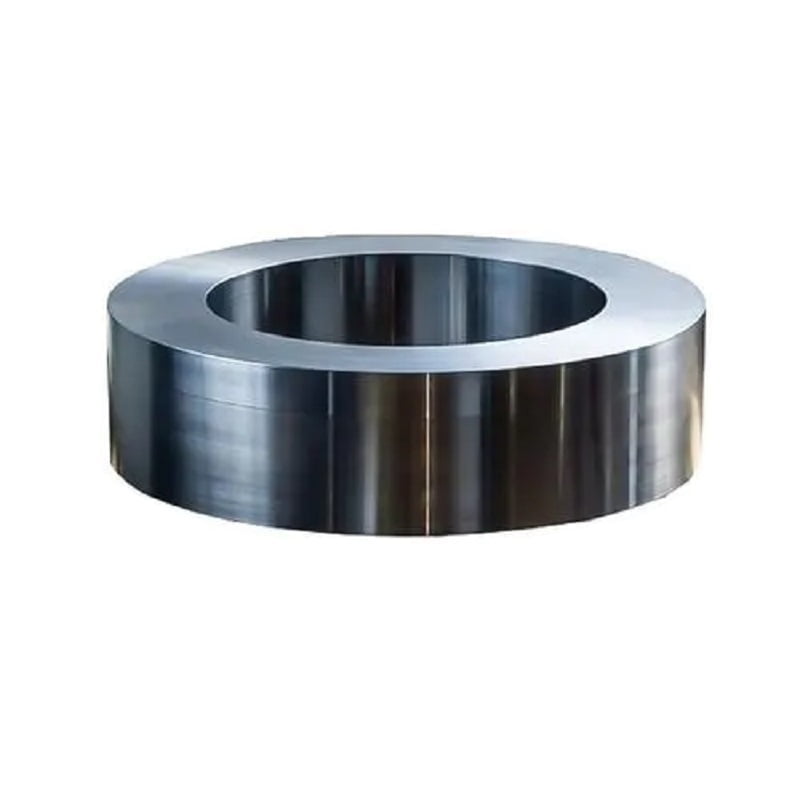
NIMONIC 90 et INCONEL 718 sont tous deux des superalliages renommés à base de nickel qui présentent des performances exceptionnelles dans des conditions extrêmes, ce qui les rend très recherchés dans diverses applications à fortes contraintes. Ces alliages sont spécialement conçus pour offrir des propriétés mécaniques exceptionnelles, une résistance à l'oxydation et une durabilité accrue dans des environnements soumis à des températures élevées et à des substances corrosives. La compréhension de leurs caractéristiques distinctes est cruciale pour les ingénieurs et les scientifiques des matériaux lors de la sélection du matériau approprié pour des applications exigeantes. Les principaux aspects de NIMONIC 90 et INCONEL 718 comprennent :
Fabrication et maniabilité: Bien que les deux alliages puissent être soudés et usinés, leur ouvrabilité diffère considérablement, ce qui a un impact sur les processus de fabrication.
Composition: Les deux alliages sont principalement composés de nickel mais diffèrent par leurs éléments d'alliage, qui influencent leurs propriétés mécaniques et leurs performances.
Propriétés mécaniques: Chaque alliage offre des limites de traction et d'élasticité élevées, avec des variations qui répondent aux besoins spécifiques de l'industrie.
Caractéristiques de résistance: Les deux alliages démontrent une excellente résistance à la corrosion et à l’oxydation, cruciale pour les applications dans l’aérospatiale et la production d’électricité.
Applications: Ils sont largement utilisés dans les composants critiques d’industries telles que l’aérospatiale, le pétrole et le gaz et l’énergie nucléaire.
Composition
Alliage | Nickel (Ni) | Chrome (Cr) | Fer (Fe) | Molybdène (Mo) | Cobalt (Co) | Titane (Ti) | Aluminium (Al) |
---|---|---|---|---|---|---|---|
NIMONIQUE 90 | 50-55% | 19-21% | Bal. | 5-6% | 15% | 00,5-1 % | 3-4% |
INCONEL718 | 50-55% | 17-21% | Bal. | 2,8-3,4% | 5% | 00,7-1,5% | 00,2-0,8% |
Propriétés mécaniques
Propriété | NIMONIQUE 90 | INCONEL718 |
---|---|---|
Densité | 8,2 g/cm³ | 8,19 g/cm³ |
Résistance à la traction (température ambiante) | ~950MPa | ~1 000 MPa |
Limite d'élasticité (température ambiante) | ~750 MPa | ~900MPa |
Plage de température de fonctionnement | Jusqu'à 980 °C | Jusqu'à 700 °C |
Allongement (à la fracture) | 20% | 30% |
Résistance à la corrosion et à l'oxydation
Alliage | La description |
---|---|
NIMONIQUE 90 | Excellente résistance à l'oxydation, en particulier à haute température, ce qui le rend idéal pour les composants de turbines et les scénarios de contraintes élevées. |
INCONEL718 | Bonne résistance à l’oxydation et à la corrosion dans une variété d’environnements, notamment dans les applications aérospatiales et pétrolières et gazières. |
Applications
Industrie | Applications NIMONIC 90 | Applications de l'INCONEL 718 |
---|---|---|
Aérospatial | Aubes de turbine, chambres de combustion et composants haute température | Moteurs d'avion, turbines à gaz et moteurs de fusée |
La production d'énergie | Composants de turbines à gaz | Fabrication de turbines et de réacteurs |
Pétrole et Gaz | Tubes et composants de fond de trou dans des environnements hostiles | Matériel de forage et composants de vannes |
Industrie Nucléaire | Composants de réacteur, en particulier là où une résistance élevée est requise | Utilisé dans les récipients sous pression et autres composants critiques du réacteur |
Fabrication et maniabilité
Alliage | Techniques de fabrication | Ouvrage écroui par laminage puis stabilisé par traitement thermique à basse température jusqu'au quart de dur |
---|---|---|
NIMONIQUE 90 | Soudage, usinage, forgeage | Modéré – peut être difficile à usiner en raison de sa haute résistance. |
INCONEL718 | Soudage, usinage, formage | Bon – connu pour sa usinabilité et sa bonne soudabilité. |
Avantages
Alliage | Avantages |
---|---|
NIMONIQUE 90 | – Résistance aux hautes températures et résistance à l’oxydation. |
– Bonne fabricabilité et haute résistance à la fatigue thermique. | |
INCONEL718 | – Excellente résistance à la corrosion dans divers environnements. |
– Limite d’élasticité et ténacité élevées, ce qui le rend adapté aux applications critiques. | |
– Bonne soudabilité et usinabilité, permettant des procédés de fabrication polyvalents. |
Différences
Caractéristique | NIMONIQUE 90 | INCONEL718 |
---|---|---|
Objectif principal | Conçu pour les applications à haute température, en particulier dans les environnements aérospatiaux et de turbines. | Applications polyvalentes dans les industries aérospatiale, pétrolière, gazière et nucléaire, avec une bonne résistance à la corrosion. |
Variabilité de la composition | Une teneur plus élevée en cobalt améliore les performances à haute température. | Teneur en nickel inférieure, équilibrée avec d'autres éléments d'alliage pour des performances complètes. |
Ouvrage écroui par laminage puis stabilisé par traitement thermique à basse température jusqu'au quart de dur | Plus difficile à usiner en raison des caractéristiques de résistance. | Généralement plus facile à traiter, adapté aux géométries et fabrications complexes. |
Cette analyse comparative décrit les principales caractéristiques et applications du NIMONIC 90 et de l'INCONEL 718, aidant à déterminer quel alliage peut être le plus approprié pour des besoins d'ingénierie spécifiques en fonction de leurs propriétés et avantages respectifs.