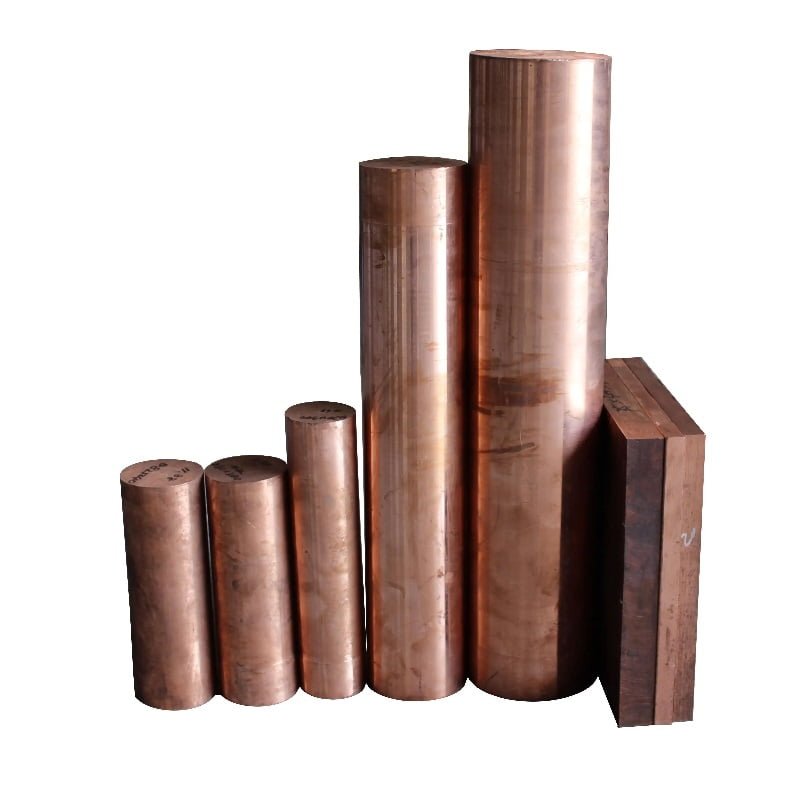
C18150 et C18200 sont tous deux des alliages de cuivre-chrome-zirconium, couramment utilisés dans les applications industrielles où la résistance élevée, la conductivité électrique et la résistance à la corrosion sont cruciales. Bien qu'ils partagent des similitudes en raison de leur composition en alliage, il existe des différences importantes entre C18150 et C18200 qui influencent leurs applications spécifiques et leurs caractéristiques de performance.
Composition de l'alliage
- Cuivre (avec): Environ 97,5% min
- Chrome (Cr) : 0.50-1,50%
- Zirconium (ZR): 0.10-0,50%
- Autres éléments: De petites quantités d'autres éléments comme le fer (Fe) et le phosphore (P) peuvent être présentes.
C18200:
- Cuivre (avec): Environ 96,0% min
- Chrome (Cr) : 1,20-2,00%
- Zirconium (ZR): 0.10-0,60%
- Autres éléments: De petites quantités d'autres éléments comme le fer (Fe) et le phosphore (P) peuvent être présentes.
Différences clés
1. Contenu du chrome:
- C18150: Contient 0,50 à 1,50% de chrome.
- C18200: Contient 1,20 à 2,00% de chrome.
La teneur en chrome plus élevée en C18200 (par rapport à C18150) offre généralement une résistance et une dureté accrues, ainsi qu'une amélioration de la résistance à la corrosion et à l'usure. Cela rend le C18200 adapté aux applications où des propriétés mécaniques plus élevées et une meilleure résistance à la corrosion sont nécessaires.
2. Conductivité électrique:
- C18150: Généralement, une conductivité électrique légèrement plus élevée par rapport au C18200 en raison de sa teneur en chrome plus faible. Cela rend le C18150 adapté aux applications où une conductivité électrique élevée est critique, comme dans les contacts électriques et les composants conducteurs.
3. Propriétés mécaniques:
- C18200: Avec sa teneur en chrome plus élevée, le C18200 a tendance à avoir une résistance et une dureté plus élevées par rapport au C18150. Cela rend le C18200 plus adapté aux applications nécessitant de bonnes propriétés mécaniques, comme dans les électrodes de soudage, les composants de soudage de résistance et les inserts de moisissure.
4. Conductivité thermique:
- Les deux alliages ont une bonne conductivité thermique, qui est une caractéristique typique des alliages de cuivre. L'ajout de chrome et de zirconium n'affecte pas significativement la conductivité thermique par rapport au cuivre pur, ce qui rend ces alliages adaptés aux applications nécessitant un transfert de chaleur efficace.
Applications
C18150:
- Contacts électriques: En raison de sa conductivité électrique élevée et de sa bonne résistance au ramollissement à des températures élevées, le C18150 est couramment utilisé dans les contacts électriques, les connecteurs et les bornes.
- Electrodes de soudage: Son excellente résistance à la chaleur et à l'usure rend le C18150 adapté aux électrodes de soudage et à d'autres composants de soudage de résistance.
- Inserts de moisissure: Dans les applications de moulage par injection, le C18150 est utilisé pour les inserts de moisissure où une bonne conductivité thermique et une résistance à l'usure sont nécessaires.
C18200:
- Composants de soudage de résistance: Sa résistance et sa dureté plus élevées rendent le C18200 idéal pour les composants, les électrodes et les conseils de soudage de résistance.
- Moulage en plastique: Le C18200 est utilisé dans les moules d'injection en plastique où sa dureté et sa résistance à l'usure sont bénéfiques.
- Plaques d'échangeur de chaleur: Sa résistance à la corrosion et sa conductivité thermique rendent C18200 adapté aux plaques d'échangeur de chaleur et aux ailerons.
Caractéristiques de performance
- Résistance à la corrosion: Le C18150 et le C18200 présentent une bonne résistance à la corrosion, ce qui est essentiel pour leur utilisation dans divers environnements industriels.
- Usinabilité : Les alliages de chrome-zirconium cuivre sont généralement machinables, permettant la fabrication de formes et de composants complexes.
- Soudabilité : Ces alliages peuvent être soudés à l'aide de techniques de soudage standard adaptées aux alliages de cuivre.
Conclusion
En conclusion, alors que C18150 et C18200 sont tous deux des alliages de cuivre-chrome-zirconium utilisés dans des applications industrielles similaires, leurs compositions et propriétés spécifiques les rendent adaptés à différents types d'applications. Le C18200, avec sa teneur en chrome plus élevée, offre une résistance et une dureté supérieures par rapport au C18150, qui a une conductivité électrique légèrement plus élevée. Le choix entre ces alliages dépend des exigences spécifiques de l'application, telles que la résistance mécanique, la conductivité électrique, la résistance à la corrosion et les propriétés thermiques. Comprendre ces différences permet aux ingénieurs et aux concepteurs de sélectionner l'alliage le plus approprié pour des performances et une longévité optimales dans leurs applications respectives.