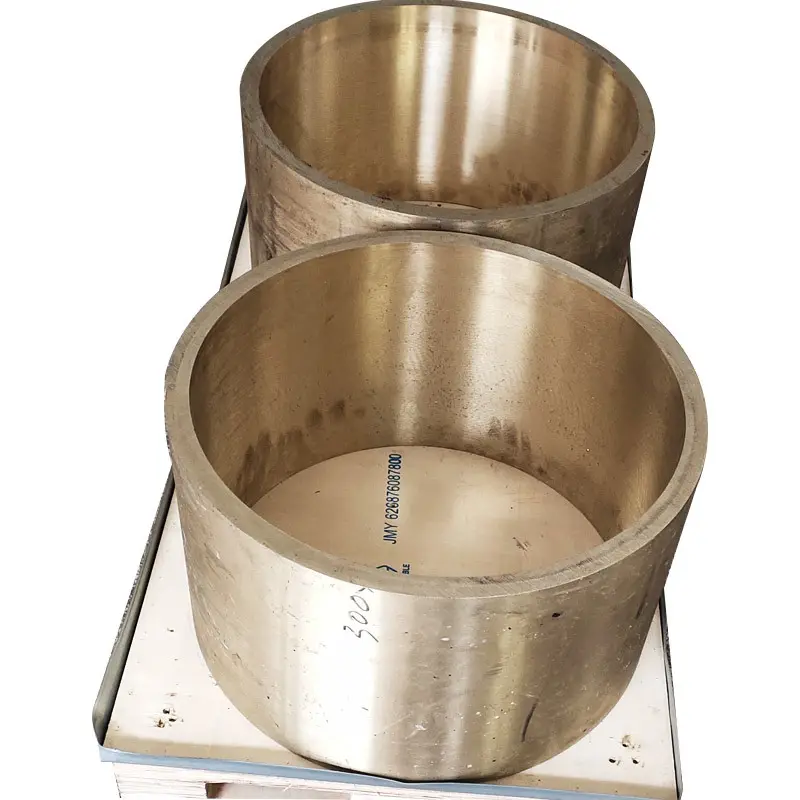
Introduction:
When selecting materials for engineering applications, particularly in demanding environments, the choice between different alloys can significantly impact performance, longevity, and cost-effectiveness. C63000 and C95400 are two copper-based alloys that often come under consideration for various industrial applications. Both belong to the aluminum bronze family but have distinct characteristics that make them suitable for different uses. This comprehensive analysis will delve into the composition, properties, applications, advantages, and limitations of each alloy to assist in making an informed decision.
- Composition:
- Copper (Cu): 78.0-82.0%
- Aluminum (Al): 9.0-11.0%
- Iron (Fe): 3.0-5.0%
- Nickel (Ni): 4.0-5.5%
- Copper (Cu): 83.0-88.0%
- Aluminum (Al): 10.0-11.5%
- Iron (Fe): 3.0-5.0%
- Nickel (Ni): 1.5% max
The primary difference in composition is the nickel content. C63000 has a higher nickel content, which contributes to its enhanced strength and corrosion resistance.
- Propriétés mécaniques:
C63000:
- Tensile Strength: 110-125 ksi (758-862 MPa)
- Yield Strength: 65-75 ksi (448-517 MPa)
- Elongation: 6-20%
- Hardness: 200-240 Brinell
C95400:
- Tensile Strength: 90-100 ksi (621-689 MPa)
- Yield Strength: 45-50 ksi (310-345 MPa)
- Elongation: 12-20%
- Hardness: 170-190 Brinell
C63000 generally exhibits higher strength and hardness due to its higher nickel content. This makes it more suitable for applications requiring greater mechanical performance.
- Résistance à la corrosion:
Both alloys offer excellent corrosion resistance, particularly in marine environments. However, there are some differences:
C63000:
- Superior resistance to seawater corrosion
- Excellent resistance to erosion-corrosion
- Bonne résistance à la fissuration par corrosion sous contrainte
C95400:
- Very good resistance to seawater corrosion
- Good resistance to erosion-corrosion
- Moderate resistance to stress corrosion cracking
The higher nickel content in C63000 contributes to its enhanced corrosion resistance, particularly in seawater and other aggressive environments.
- Wear Resistance:
Both alloys offer good wear resistance, but C63000 generally performs better in this aspect due to its higher hardness and strength.
C63000:
- Excellente résistance à l'usure
- Low coefficient of friction
- Good performance in galling-resistant applications
C95400:
- Very good wear resistance
- Moderate coefficient of friction
- Suitable for many wear-resistant applications
- Propriétés thermiques:
C63000:
- Thermal Conductivity: 26 BTU/ft hr °F (45 W/m·K)
- Coefficient of Thermal Expansion: 9.0 x 10^-6 in/in/°F (16.2 x 10^-6 m/m/°C)
C95400:
- Thermal Conductivity: 30 BTU/ft hr °F (52 W/m·K)
- Coefficient of Thermal Expansion: 9.5 x 10^-6 in/in/°F (17.1 x 10^-6 m/m/°C)
C95400 has slightly better thermal conductivity, which can be advantageous in heat transfer applications.
- Fabrication Characteristics:
C63000:
- Good machinability (30% of C36000 free-cutting brass)
- Excellent hot working properties
- Can be welded using standard techniques for copper alloys
- Not recommended for cold working
C95400:
- Good machinability (40% of C36000 free-cutting brass)
- Excellentes propriétés de coulée
- Can be welded using standard techniques for copper alloys
- Capacité de travail à froid limitée
C95400 has better castability, making it more suitable for complex cast components. C63000, while still castable, is often preferred for wrought products.
- Applications:
C63000:
- Marine propeller shafts and propellers
- Pump shafts and impellers
- Valve stems and seats
- Bearings and bushings in corrosive environments
- Composants pétroliers et gaziers offshore
- Aerospace and defense industry parts
C95400:
- Pump casings and impellers
- Valve bodies and trim
- Marine hardware and fittings
- Gears and worm wheels
- Équipement de traitement chimique
- mais il y a des limites
- Considérations relatives aux coûts :
Generally, C63000 is more expensive than C95400 due to its higher nickel content. The price difference can be significant, especially for large components or high-volume production.
- Availability:
Both alloys are widely available, but C95400 might be more readily available in cast forms due to its superior casting properties. C63000 is often preferred in wrought forms.
- Specific Advantages and Limitations:
C63000 Advantages:
- Higher strength and hardness
- Superior corrosion resistance, especially in seawater
- Excellente résistance à l'usure
- Better performance in high-stress applications
C63000 Limitations:
- Higher cost
- Less suitable for complex cast shapes
- Limited cold workability
C95400 Advantages:
- Excellentes propriétés de coulée
- Good balance of strength and ductility
- Lower cost compared to C63000
- Suitable for a wide range of applications
C95400 Limitations:
- Lower strength compared to C63000
- Slightly less corrosion resistant in extreme environments
- Environmental Considerations:
Both alloys are recyclable, which is an advantage from an environmental perspective. However, the higher nickel content in C63000 may require more careful handling during recycling processes.
- Regulatory Compliance:
Both alloys generally comply with various industry standards and regulations. However, specific applications may have particular requirements, so it’s essential to check relevant standards for your intended use.
- Long-term Performance:
C63000 typically offers better long-term performance in harsh environments due to its superior corrosion and wear resistance. This can lead to lower maintenance costs and longer service life in demanding applications.
- Galvanic Corrosion Considerations:
When used in conjunction with other metals, both alloys are relatively noble. However, care should be taken when coupling them with more anodic metals to prevent galvanic corrosion.
- Traitement thermique:
C63000 can be strengthened through heat treatment, offering the possibility of enhancing its mechanical properties for specific applications. C95400, while it can be heat-treated, is less commonly subjected to this process.
Conclusion and Recommendations:
The choice between C63000 and C95400 depends on the specific requirements of your application. Here are some guidelines to help you decide:
Choose C63000 if:
- Your application requires maximum strength and hardness.
- The component will be exposed to highly corrosive environments, especially seawater.
- Wear resistance is a critical factor.
- The application involves high-stress conditions.
- You need a wrought product rather than a cast one.
- Long-term performance in harsh environments is crucial.
- Cost is less of a concern compared to performance.
Choose C95400 if:
- You need to cast complex shapes.
- The application requires a good balance of strength and ductility.
- Corrosion resistance is important, but not to the extreme level provided by C63000.
- Cost-effectiveness is a significant factor.
- The component will be used in food processing or chemical industries.
- You need good thermal conductivity.
- The application doesn’t involve extreme stress or wear conditions.
Final Thoughts:
Both C63000 and C95400 are excellent aluminum bronze alloys with their own sets of strengths. C63000 excels in high-performance applications where strength, corrosion resistance, and wear resistance are paramount. It’s particularly well-suited for marine and offshore applications. C95400, on the other hand, offers a more cost-effective solution for a wide range of applications, especially where casting complex shapes is necessary.
To make the best choice, consider the following factors:
- Specific environmental conditions the component will face
- Mechanical stress and wear requirements
- Manufacturing process (casting vs. wrought products)
- Long-term performance expectations
- Budget constraints
- Availability and lead times
- Compatibility with other materials in the system
- Regulatory and industry-specific requirements
By carefully evaluating these factors against the properties of C63000 and C95400, you can select the alloy that best meets your needs, ensuring optimal performance, longevity, and cost-effectiveness for your specific application.