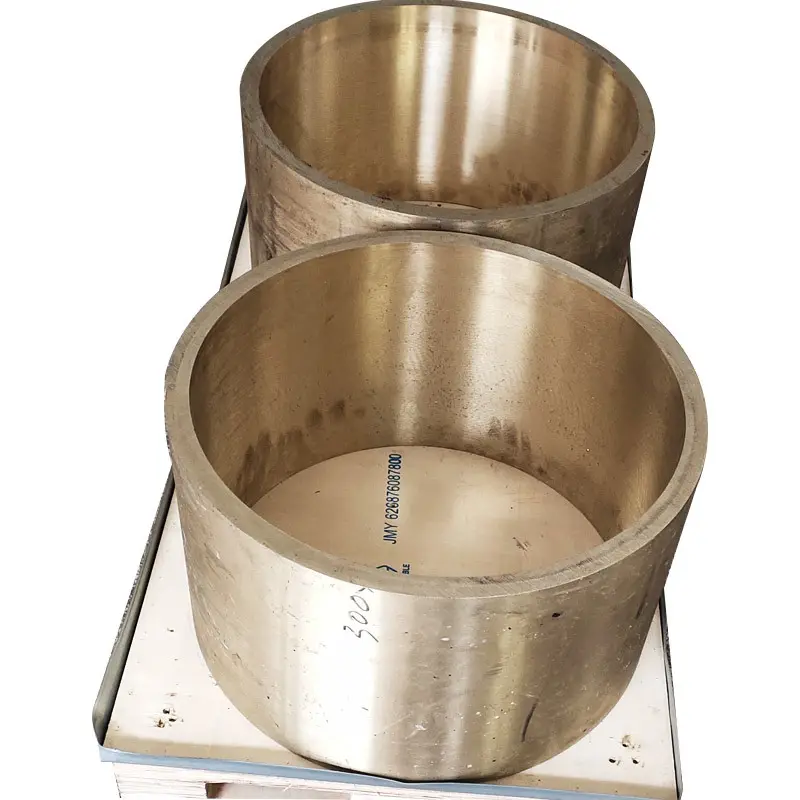
En la industria de la construcción naval, elegir el material adecuado para la fabricación de hélices es crucial para garantizar un rendimiento, durabilidad y eficiencia óptimas. Entre los diversos materiales disponibles, el bronce de aluminio ha surgido como una opción popular debido a su excelente combinación de resistencia, resistencia a la corrosión y maquinabilidad. Sin embargo, no todos los grados de bronce de aluminio se crean iguales cuando se trata de la fabricación de hélices. Este artículo tiene como objetivo explorar los diferentes grados de bronce de aluminio y determinar cuál es el más adecuado para las hélices marinas.
Comprender el bronce de aluminio
El bronce de aluminio es una familia de aleaciones a base de cobre que contienen aluminio como elemento de aleación primaria, a menudo con elementos adicionales como hierro, níquel y manganeso. Estas aleaciones son conocidas por su alta resistencia, excelente resistencia a la corrosión (especialmente en el agua de mar) y una buena resistencia al desgaste.
Propiedades clave para la fabricación de hélices
Al seleccionar un grado de bronce de aluminio para la fabricación de hélices, se deben considerar varias propiedades clave:
- Fuerza
- Resistencia a la corrosión
- Resistencia al desgaste
- Castabilidad
- Maquinabilidad
- Resistencia a la fatiga
- Resistencia a la cavitación
Grados comunes de bronce de aluminio para hélices marinas
Los grados de bronce de aluminio más utilizados para hélices marinos son:
Comparemos estos grados en función de su composición química y propiedades mecánicas.
Composición química
La siguiente tabla muestra la composición química típica de estos grados de bronce de aluminio:
Calificación | Cu (%) | Al (%) | Fe (%) | En (%) | Mn (%) | Otro (%) |
---|---|---|---|---|---|---|
C95200 | 88-92 | 8-9.5 | 2.5-4 | - | 1 Max | 0.5 máx. |
C95300 | 86-90 | 9-11 | 2.5-4 | - | 1 Max | 0.5 máx. |
C95400 | 83-87 | 10-11,5 | 3-5 | 1,5 máx. | 1 Max | 0.5 máx. |
C95500 | 78-82 | 10-11,5 | 3-5 | 3-5.5 | 3,5 máx. | 0.5 máx. |
C95800 | 79-82 | 8,5-9,5 | 3,5-4,5 | 4-5 | 0.8-1.5 | 0.5 máx. |
Propiedades mecánicas
Las propiedades mecánicas de estos grados son cruciales para determinar su idoneidad para la fabricación de hélices:
Calificación | Resistencia a la tracción (MPa) | Límite elástico (MPa) | Elongación (%) | Resistencia a la tracción de |
---|---|---|---|---|
C95200 | 585 | 275 | 20 | 150 |
C95300 | 620 | 285 | 18 | 160 |
C95400 | 690 | 345 | 12 | 190 |
C95500 | 760 | 380 | 10 | 210 |
C95800 | 690 | 275 | 15 | 170 |
Evaluación de calificaciones para la fabricación de hélices
Ahora, evaluemos cada calificación en función de las propiedades clave requeridas para la fabricación de hélices:
1. C95200 (AB1)
- Fuerza: moderado
- Resistencia a la corrosión: bien
- Resistencia al desgaste: moderada
- Castabilidad: Excelente
- Machinabilidad: muy buena
- Resistencia de fatiga: bien
- Resistencia a la cavitación: moderado
C95200 a menudo se usa para hélices pequeñas a medianas debido a su excelente capacidad y buena maquinabilidad. Sin embargo, su resistencia moderada y resistencia al desgaste pueden limitar su uso en aplicaciones más grandes o de alto rendimiento.
2. C95300 (AB2)
- Fuerza: bien
- Resistencia a la corrosión: muy buena
- Resistencia al desgaste: bueno
- Castabilidad: muy bien
- Machinabilidad: bueno
- Resistencia de fatiga: bien
- Resistencia a la cavitación: bien
C95300 ofrece un buen equilibrio de propiedades, lo que lo hace adecuado para una amplia gama de tamaños de hélice. Su resistencia mejorada y resistencia al desgaste en comparación con C95200 lo convierten en una opción popular para muchas aplicaciones marinas.
3. C95400 (AB3)
- Fuerza: muy buena
- Resistencia a la corrosión: excelente
- Resistencia al desgaste: muy buena
- Castabilidad: bien
- Machinabilidad: bueno
- Resistencia de fatiga: muy buena
- Resistencia a la cavitación: muy buena
C95400 se usa ampliamente para grandes hélices marinas debido a su excelente combinación de resistencia, resistencia a la corrosión y resistencia al desgaste. Sus propiedades mecánicas mejoradas lo hacen adecuado para aplicaciones de alto rendimiento.
4. C95500 (AB4)
- Fuerza: excelente
- Resistencia a la corrosión: excelente
- Resistencia al desgaste: excelente
- Castabilidad: bien
- Machinabilidad: moderado
- Resistencia de fatiga: excelente
- Resistencia a la cavitación: excelente
C95500 ofrece la mayor resistencia y resistencia al desgaste entre estos grados, lo que lo hace ideal para hélices grandes y de alto rendimiento. Sin embargo, su maquinabilidad reducida puede aumentar los costos de fabricación.
5. C95800 (AB5)
- Fuerza: muy buena
- Resistencia a la corrosión: excelente
- Resistencia al desgaste: muy buena
- Castabilidad: muy bien
- Machinabilidad: bueno
- Resistencia de fatiga: excelente
- Resistencia a la cavitación: excelente
C95800 se considera el grado premium para las hélices marinas debido a su excelente equilibrio de propiedades. Ofrece resistencia a la corrosión superior, buena capacidad de fundición y excelente resistencia a la fatiga y cavitación.
Seleccionar la mejor calificación para la fabricación de hélices
La elección del mejor grado de bronce de aluminio para la fabricación de hélices depende de varios factores, incluidos:
- Tamaño de la hélice
- Tipo de embarcación y requisitos de rendimiento
- Condiciones de funcionamiento (por ejemplo, temperatura del agua de mar, salinidad)
- Capacidades de fabricación
- Consideraciones de costos
Para ayudar con el proceso de selección, considere las siguientes pautas:
Tamaño de la hélice | Tipo de vaso | Grado recomendado |
---|---|---|
Pequeño | Barcos de recreo, yates | C95200, C95300 |
Medio | Barcos de pesca, remolcadores | C95300, C95400 |
Grande | Barcos de carga, petroleros | C95400, C95500 |
Muy grande | Barcos de contenedores, crucero | C95500, C95800 |
Conclusión
Si bien todos los grados de bronce de aluminio discutidos ofrecen excelentes propiedades para la fabricación de hélices marinas, C95800 (AB5) se destaca como la mejor opción general para la mayoría de las aplicaciones. Su combinación superior de resistencia, resistencia a la corrosión, capacidad de fundición y resistencia a la fatiga lo hace ideal para una amplia gama de tamaños de hélice y tipos de vasos.
Sin embargo, la selección final siempre debe basarse en requisitos y limitaciones específicos del proyecto. Para hélices más pequeñas o aplicaciones menos exigentes, C95300 o C95400 puede ofrecer una solución más rentable. Por el contrario, para las hélices muy grandes o de alto rendimiento, C95500 podría ser la mejor opción a pesar de su mayor costo y su maquinabilidad reducida.
Al seleccionar un grado de bronce de aluminio para la fabricación de hélices, es crucial consultar con expertos en materiales y diseñadores de hélices para garantizar que el grado elegido cumpla con todos los requisitos de rendimiento, durabilidad y fabricación. Al considerar cuidadosamente las propiedades de cada grado y igualarlas a las necesidades específicas del proyecto, los fabricantes pueden garantizar el rendimiento óptimo de la hélice y la longevidad en los entornos marinos.