Inconel X-750 und Inconel 625 sind beide Hochleistungs-Nickel-Chrom-Legierungen, die für bestimmte Anwendungen entwickelt wurden, aber sie haben unterschiedliche Zusammensetzungen und Eigenschaften, die sie für verschiedene Umgebungen und Bedingungen geeignet machen.
Inconel X-750
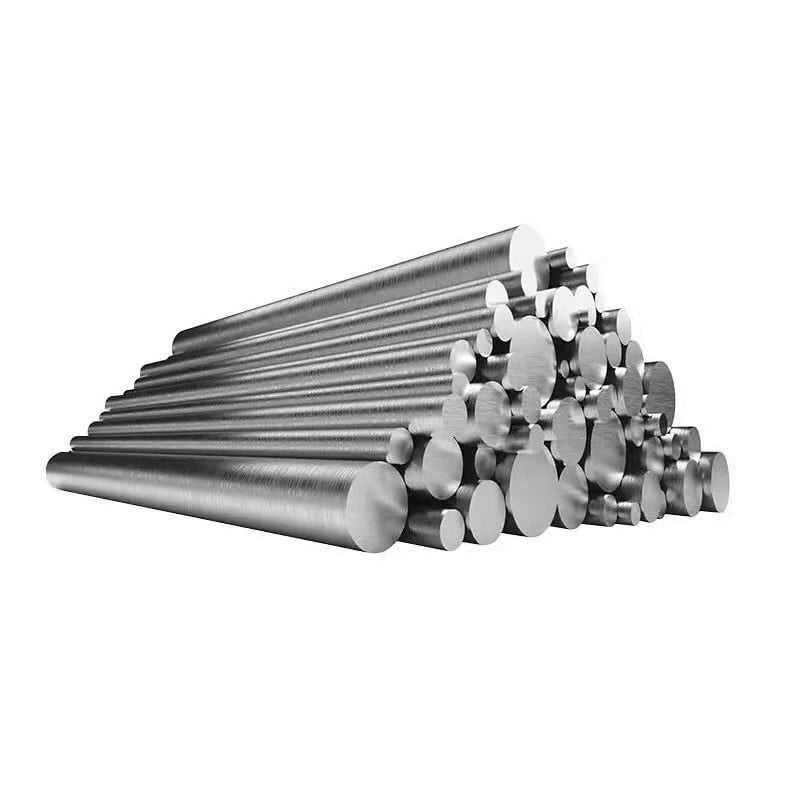
Komposition:
- Inconel X-750 ist eine mit Niederschlagsmenschen überzogene Nickelchrom-Legierung.
- Es enthält typischerweise 70% Nickel, 14-17% Chrom, 2,25-2,75% Titan, 0,7-1,2% Aluminium und kleine Mengen anderer Elemente wie Eisen, Niob und Mangan.
Eigenschaften:
- Stärke: Inconel X-750 ist für seine hervorragende Festigkeit bei hohen Temperaturen von bis zu 704 ° C bekannt.
- Wärmewiderstand: Es behält bei erhöhten Temperaturen seine Festigkeit und Oxidationsbeständigkeit bei.
- Anwendungen: In Gasturbinen, Raketenmotoren, Kernreaktoren, Druckbehältern und Federn, bei denen eine hohe Festigkeit bei erhöhten Temperaturen erforderlich ist, wird häufig eingesetzt.
Inconel 625
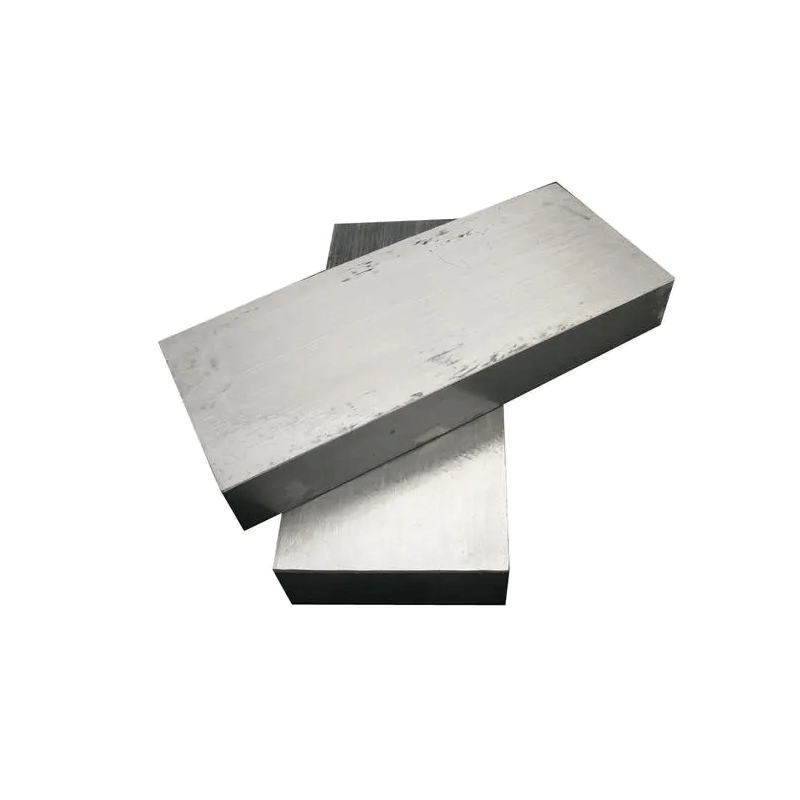
Komposition:
- Inconel 625 ist eine durch die Zugabe von Molybdän und Niob gestärkte Nickel-Chrom-Legierung mit fester Lösung.
- Es enthält typischerweise 58% Nickel, 20-23% Chrom, 8-10% Molybdän, 3,15-4,15% Niob (Columbium) und kleinere Mengen an Eisen, Tantal, Silizium und Aluminium.
Eigenschaften:
- Korrosionsbeständigkeit: Inconel 625 ist in einer Vielzahl schwerer Umgebungen, einschließlich Meerwasser und chemischer Verarbeitung, stark resistent gegen Korrosion und Oxidation.
- Stärke: Es bietet gute Kraft und Zähigkeit sowohl bei kryogenen als auch bei hohen Temperaturen (bis zu 1093 ° C oder 2000 ° F).
- Anwendungen: Wird in Meeresanwendungen, chemischen Verarbeitungsgeräten, Luft- und Raumfahrt- und Verteidigungskomponenten sowie Verschmutzungskontrollsystemen verwendet.
Vergleich
- Festigkeit und Temperaturwiderstand:
- Inconel X-750 hat im Vergleich zu Inconel 625 eine überlegene Festigkeit bei hohen Temperaturen. Es ist speziell für Anwendungen ausgelegt, bei denen eine hohe Festigkeit bei Temperaturen bis zu 704 ° C (1300 ° F) entscheidend ist.
- Korrosionsbeständigkeit:
- Inconel 625 hat eine bessere Korrosionsbeständigkeit im Vergleich zu Inconel X-750, insbesondere in harten Umgebungen mit Säuren, Meerwasser und Oxidation.
- Anwendungen:
- Inconel X-750 wird in Anwendungen verwendet, bei denen eine hohe Festigkeit bei erhöhten Temperaturen kritisch ist, wie Gasturbinen, Raketenmotoren und Kernreaktoren.
- Inconel 625 Findet Anwendungen, bei denen Korrosionswiderstand von größter Bedeutung ist, einschließlich Meeresumgebungen, chemischer Verarbeitung und Luft- und Raumfahrtkomponenten.
Fazit
Die Auswahl zwischen Inconel X-750 und Inconel 625 hängt weitgehend von den spezifischen Anforderungen der Anwendung ab. Wenn eine hohe Festigkeit bei erhöhten Temperaturen die primäre Überlegung ist, wird Inconel X-750 bevorzugt. In Inconel 625 ist Inconel 625 die bessere Wahl. Beide Legierungen repräsentieren fortgeschrittene Lösungen für die technische Technik für die anspruchsvollen Industrie- und Luft- und Raumfahrtanwendungen.