Inconel 718 und Inconel 725 sind beide Superlegierungen auf Nickelbasis, unterscheiden sich jedoch in Zusammensetzung und Eigenschaften, was zu unterschiedlichen Anwendungen führt:
Inconel 718:
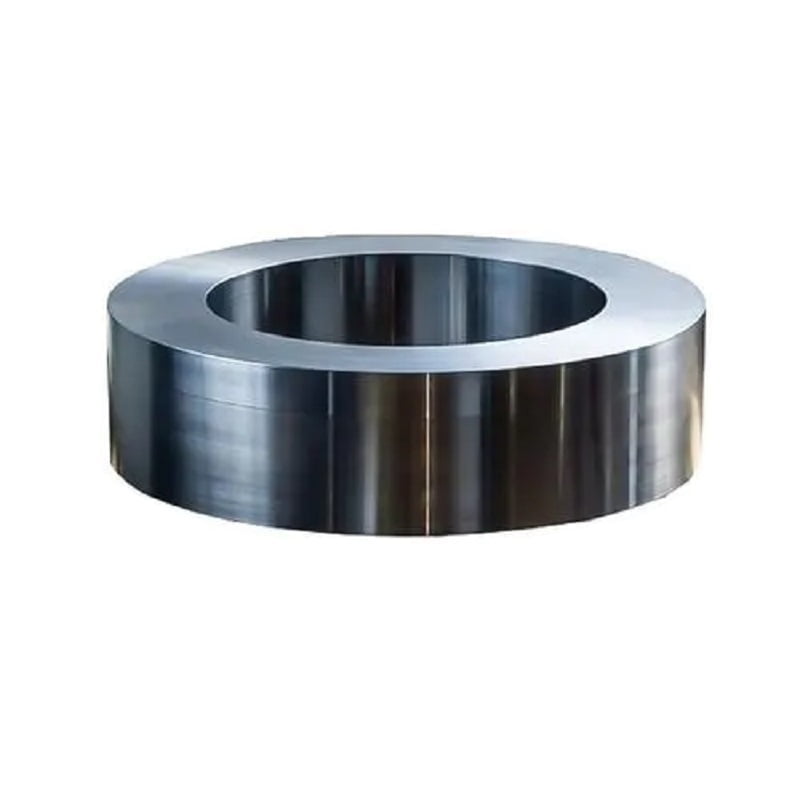
- Komposition: Inconel 718 enthält typischerweise etwa 50–55 % Nickel, mit erheblichen Mengen an Chrom (~17–21 %), Eisen (~18,5 %), Niob (~5 %) und kleineren Zusätzen von Molybdän, Titan, Aluminium usw Tantal.
- Eigenschaften:
- Stärke: Hervorragende Festigkeit, insbesondere bei erhöhten Temperaturen (bis zu etwa 1300 °F oder 704 °C).
- Korrosionsbeständigkeit: Gute Oxidations- und Korrosionsbeständigkeit.
- Anwendungen: Weit verbreitet in der Luft- und Raumfahrt, in Gasturbinen, Kernreaktoren und anderen Hochtemperaturanwendungen, bei denen Festigkeit und Korrosionsbeständigkeit von entscheidender Bedeutung sind. Es ist bekannt für seine Zuverlässigkeit in Umgebungen mit hoher Belastung und für die Beibehaltung seiner Eigenschaften bei hohen Temperaturen.
Inconel 725:
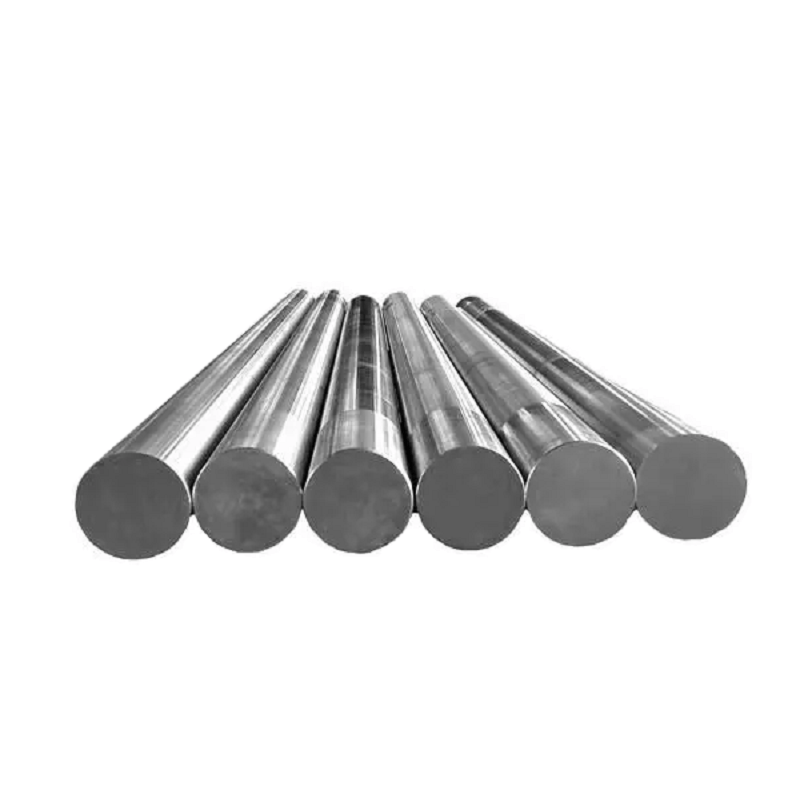
- Komposition: Inconel 725 ist eine Nickel-Chrom-Legierung mit Zusätzen von Niob, Titan und Molybdän. Es enthält typischerweise etwa 58 % Nickel, erhebliche Mengen Chrom (~19 %), Niob (~5,5 %), Titan (~1,75 %) und kleinere Mengen Molybdän (~3 %) und Aluminium (~0,4 %).
- Eigenschaften:
- Stärke: Höhere Festigkeit als Inconel 718, insbesondere im Temperaturbereich von 1200–1800 °F (649–982 °C).
- Korrosionsbeständigkeit: Gute Korrosions- und Oxidationsbeständigkeit, ähnlich wie Inconel 718.
- Anwendungen: Wird hauptsächlich in Umgebungen mit hoher Beanspruchung verwendet, die eine hohe Festigkeit bei erhöhten Temperaturen erfordern, wie z. B. Komponenten von Strahltriebwerken, hochfeste Befestigungselemente und Kernreaktoren.
Vergleich:
- Temperaturbeständigkeit: Inconel 725 weist im Vergleich zu Inconel 718 eine überlegene Festigkeit bei höheren Temperaturen (1200–1800 °F) auf, was für Anwendungen vorteilhaft ist, die Festigkeit unter extremen Hitzebedingungen erfordern.
- Stärke: Alloy 725 bietet im Allgemeinen eine höhere Festigkeit als Alloy 718, insbesondere bei erhöhten Temperaturen.
- Anwendungen:
- Inconel 718 ist aufgrund seiner ausgewogenen Kombination aus Festigkeit und Korrosionsbeständigkeit vielseitiger und in verschiedenen Branchen weit verbreitet und eignet sich für eine Vielzahl von Hochtemperaturanwendungen.
- Inconel 725 wird speziell für Anwendungen ausgewählt, die eine hohe Festigkeit bei Temperaturen erfordern, die über dem liegen, was Inconel 718 zuverlässig aushalten kann, wodurch es sich ideal für Anwendungen in der Luft- und Raumfahrt sowie für Hochleistungsanwendungen im Maschinenbau eignet.
Zusammenfassend lässt sich sagen, dass die Wahl zwischen Inconel 718 und Inconel 725 von spezifischen Anforderungen wie Temperaturbereich, Festigkeitsanforderungen und Umgebungsbedingungen abhängt. Inconel 718 ist universeller einsetzbar und weit verbreitet, während Inconel 725 aufgrund seiner überlegenen Festigkeit bei höheren Temperaturen ausgewählt wird, wodurch es für anspruchsvollere Anwendungen in extremen Umgebungen geeignet ist.