Beryllium copper C17200 is a high-performance alloy renowned for its exceptional mechanical properties, especially its yield strength. The yield strength of this alloy is influenced by several factors, including the specific size and shape of the components manufactured from it. This article delves into the yield strength characteristics of beryllium copper C17200 across various forms and applications, providing a comprehensive understanding of how these factors can affect performance.
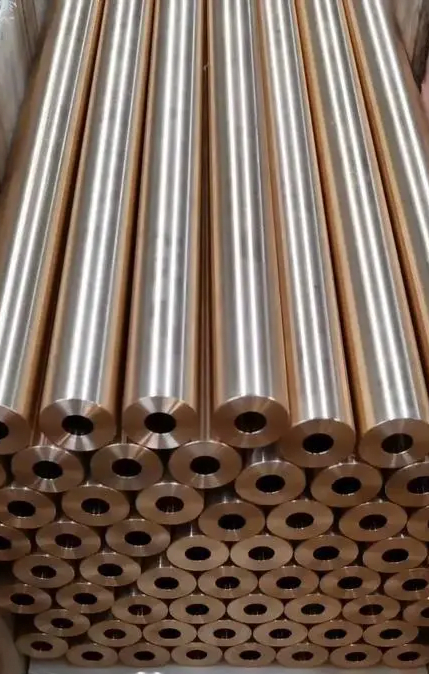
Understanding Yield Strength
Yield strength is defined as the amount of stress at which a material begins to deform plastically. Beyond this point, the material will not return to its original shape when the stress is removed. In the context of beryllium copper C17200, the yield strength can range from approximately 340 MPa to 600 MPa, depending on processing conditions and the specific shape of the component.
Factors Influencing Yield Strength
The yield strength of C17200 can vary based on:
- Heat Treatment: The alloy’s properties can be significantly altered by different heat treatment processes, including solution annealing and aging.
- Form of the Material: The shape and size of the component (e.g., rods, sheets, or precision machined parts) can influence mechanical properties due to variations in grain structure and orientation.
- Cold Work: The degree of cold working affects yield strength; more cold work generally leads to increased strength.
- Environmental Factors: Factors like temperature and exposure to corrosive environments can affect yield strength over time.
Yield Strength in Different Forms
1. Rod and Bar Stock
- Typical Yield Strength: 480 MPa to 600 MPa
- Applications: Commonly used for manufacturing fasteners, pins, and precision tools.
- Notes: The larger diameter bars tend to have slightly lower yield strength due to grain structure, while smaller diameters may exhibit higher yield strength due to finer grain size.
2. Sheet and Plate
- Typical Yield Strength: 340 MPa to 480 MPa
- Applications: Utilized in applications requiring complex shapes, such as housings and enclosures.
- Notes: Sheets and plates that undergo cold rolling processes often show increased yield strength due to strain hardening.
3. Extrusions
- Typical Yield Strength: 450 MPa to 550 MPa
- Applications: Often used in structural components and brackets.
- Notes: The yield strength can vary based on the extrusion process, temperature, and cooling rate, which can affect the alloy’s microstructure.
4. Forgings
- Typical Yield Strength: 500 MPa to 600 MPa
- Applications: Used for critical aerospace components and heavy machinery parts.
- Notes: Forged parts generally exhibit superior mechanical properties due to refined grain structure and improved homogeneity.
5. Precision Machined Parts
- Typical Yield Strength: 480 MPa to 590 MPa
- Applications: Components such as connectors and specialized fasteners.
- Notes: Machining can induce residual stresses that may enhance or reduce yield strength depending on the machining process and conditions.
Implications of Size and Shape on Yield Strength
Size Effects
- Smaller Sections: Smaller components often exhibit higher yield strength due to a finer grain structure achieved during processing.
- Larger Sections: Larger components may have lower yield strength due to grain growth, which can occur during manufacturing processes such as casting or slower cooling rates.
Shape Considerations
- Complex Shapes: Components with complex geometries can experience variations in yield strength across different regions due to differences in material flow during processing.
- Uniform Shapes: Components with simple, uniform shapes (like cylinders) generally maintain consistent yield strength across their length, making them more predictable in performance.
Summary of Yield Strength Variability
- Rods and Bars: 480 MPa – 600 MPa
- Sheets and Plates: 340 MPa – 480 MPa
- Extrusions: 450 MPa – 550 MPa
- Forgings: 500 MPa – 600 MPa
- Precision Machined Parts: 480 MPa – 590 MPa
Conclusion
The yield strength of beryllium copper C17200 is a crucial mechanical property that is influenced by various factors, including heat treatment, size, shape, and processing methods. Understanding these variations is vital for engineers and manufacturers as they design components for specific applications, ensuring optimal performance and reliability.
As industries continue to demand high-performance materials, the unique attributes of beryllium copper C17200—combined with its versatility in form—will ensure its continued relevance across various fields, including aerospace, automotive, and electronics. By carefully considering the yield strength characteristics of different shapes and sizes, manufacturers can leverage the full potential of this remarkable alloy.