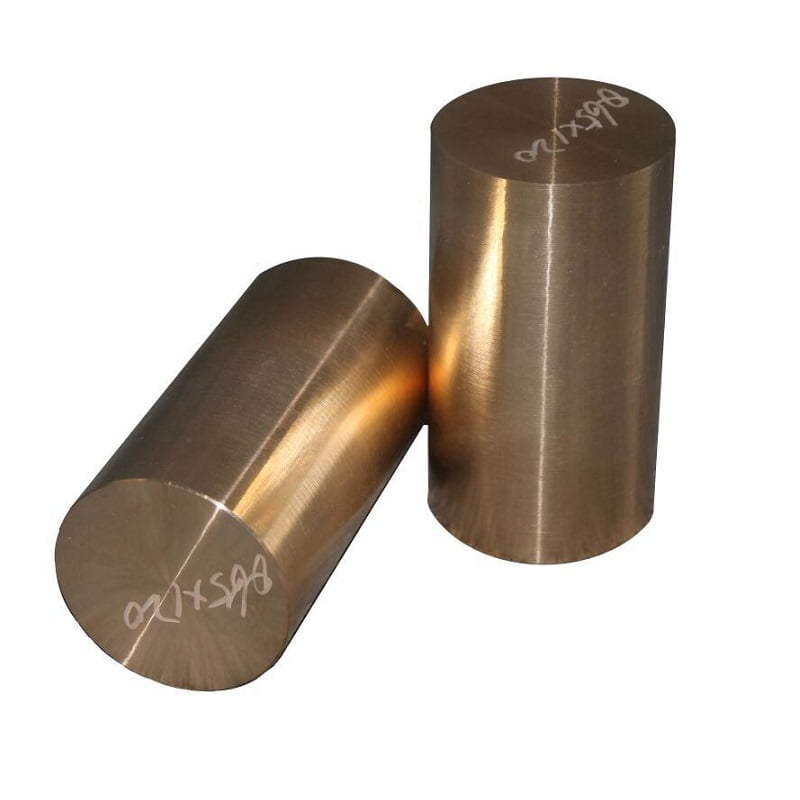
Beryllium copper C17200 is a high-performance alloy widely recognized for its exceptional mechanical properties, electrical conductivity, and corrosion resistance. This alloy is particularly important in various industrial applications, including aerospace, electronics, and precision tools. Understanding the role of each element in its chemical composition is crucial for optimizing its performance and ensuring it meets specific application requirements.
Chemical Composition of C17200
Beryllium copper C17200 is primarily composed of the following elements:
- Copper (Cu)
- Beryllium (Be)
- Cobalt (Co)
- Iron (Fe)
- Nickel (Ni)
- Other trace elements such as Silicon (Si) and Manganese (Mn)
Elemental Roles
1. Copper (Cu)
Copper is the dominant element in C17200, typically comprising about 97% of the alloy. Its primary roles include:
- Electrical Conductivity: Copper provides excellent electrical conductivity, making C17200 ideal for electrical connectors and components where efficient energy transfer is crucial.
- Thermal Conductivity: The thermal properties of copper ensure effective heat dissipation, important in high-temperature applications.
- Ductility: Copper imparts significant ductility to the alloy, allowing it to be easily formed into various shapes without cracking.
2. Beryllium (Be)
Beryllium is the key alloying element in C17200, typically present in concentrations between 1.8% and 2.0%. Its contributions include:
- Strength and Hardness: Beryllium significantly enhances the strength and hardness of the alloy. It allows C17200 to achieve high tensile and yield strength, often surpassing that of many steel grades.
- Fatigue Resistance: The presence of beryllium improves the fatigue resistance of the alloy, making it suitable for applications subjected to cyclic loading.
- Non-Sparking Properties: Beryllium copper is known for its non-sparking characteristics, making it safe for use in explosive or flammable environments.
3. Cobalt (Co)
Although cobalt is not a primary component, it is often included in trace amounts. Its roles can include:
- Increased Hardness: Cobalt can enhance the hardness of the alloy, particularly in high-stress applications.
- Improved Wear Resistance: The addition of cobalt can contribute to wear resistance, making C17200 suitable for tooling and machining applications.
4. Iron (Fe)
Iron is usually present in very small quantities, generally less than 0.5%. Its functions may involve:
- Slight Strength Enhancement: While not a major contributor, iron can provide a small increase in strength.
- Corrosion Effects: High iron content can adversely affect corrosion resistance; therefore, it is kept minimal.
5. Nickel (Ni)
Nickel may be included in minor amounts for specific enhancements, including:
- Corrosion Resistance: Nickel improves the alloy’s resistance to certain corrosive environments, especially those involving alkaline solutions.
- High-Temperature Strength: The presence of nickel can enhance the mechanical properties at elevated temperatures, further extending the application range of C17200.
6. Trace Elements (Silicon, Manganese, etc.)
Other trace elements such as silicon and manganese may be present, serving various roles:
- Microstructure Control: These elements can help refine the microstructure of the alloy, improving mechanical properties such as toughness and impact resistance.
- Enhancement of Fabrication Processes: Certain trace elements may also aid in the machinability of the alloy, making it easier to work with during manufacturing.
Summary Table of Elemental Roles
Here’s a summary of the roles of each key element in Beryllium copper C17200:
Element | Composition Range (%) | Primary Role |
---|---|---|
Copper | ~97% | Electrical and thermal conductivity, ductility |
Beryllium | 1.8 – 2.0 | Strength, hardness, fatigue resistance, non-sparking |
Cobalt | Trace | Increased hardness, wear resistance |
Iron | <0.5 | Slight strength enhancement, minimal corrosion impact |
Nickel | Trace | Corrosion resistance, high-temperature strength |
Others | Trace | Microstructure control, improved machinability |
Applications of Beryllium Copper C17200
The unique properties imparted by the elemental composition of C17200 make it highly suitable for various applications:
- Electrical Connectors and Contacts: The exceptional electrical conductivity and non-sparking nature make C17200 ideal for use in high-reliability electrical applications.
- Precision Tools: Its hardness and wear resistance render it perfect for manufacturing high-precision tools and dies.
- Aerospace Components: Beryllium copper C17200 is widely used in aerospace applications, including fasteners and structural components, where strength-to-weight ratios are crucial.
- Mining Equipment: The alloy’s toughness and durability make it a preferred choice for components that endure harsh conditions.
Conclusion
Beryllium copper C17200 is a remarkable alloy whose performance is directly influenced by its carefully balanced chemical composition. Each element contributes uniquely to the alloy’s overall properties, enhancing its suitability for a wide range of demanding applications. By understanding the specific roles of copper, beryllium, cobalt, iron, nickel, and other trace elements, manufacturers can optimize processing techniques and tailor C17200 for specific uses. As industries continue to seek materials that offer superior performance and safety, the significance of beryllium copper C17200 will undoubtedly grow, securing its place as a vital component in advanced manufacturing and engineering.