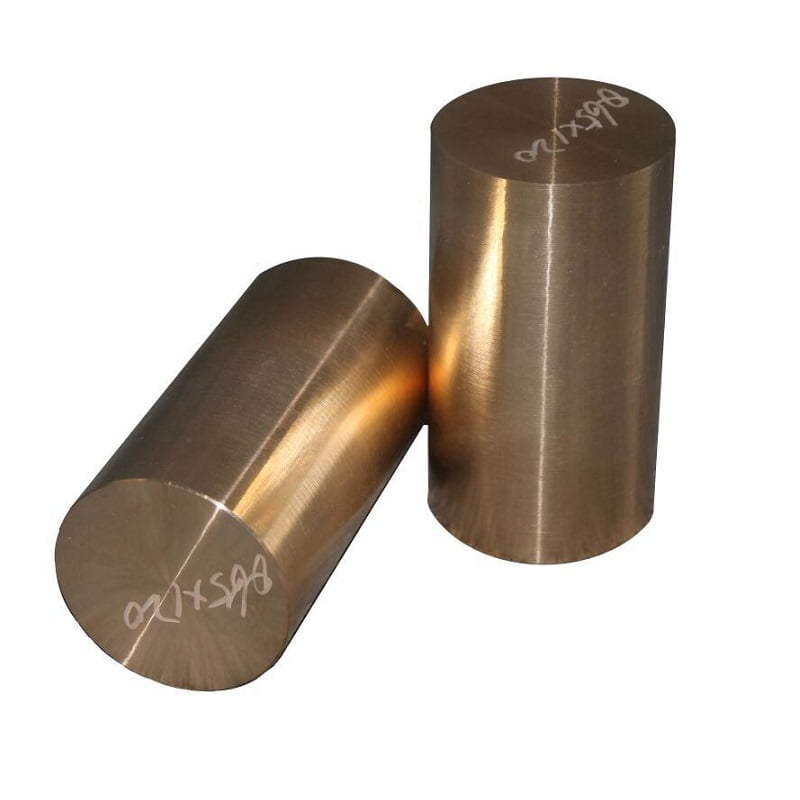
Introduction
C17510 and C17200 are both beryllium copper alloys, known for their excellent combination of high strength, conductivity, and corrosion resistance. These alloys are widely used in various industries, including aerospace, automotive, electronics, and oil & gas. While they share some similarities, they also have distinct characteristics that make them suitable for different applications.
Chemical Composition
The chemical composition of these alloys plays a crucial role in determining their properties and performance.
Element | C17510 (wt%) | C17200 (wt%) |
---|---|---|
Copper | 98.1 – 99.5 | 96.5 – 98.1 |
Beryllium | 0.2 – 0.6 | 1.8 – 2.0 |
Cobalt + Nickel | 0.2 – 1.4 | 0.2 – 0.6 |
Iron | 0.1 – 0.4 | Max 0.2 |
Aluminum | – | Max 0.2 |
Silicon | – | Max 0.2 |
Others | Max 0.5 | Max 0.5 |
The main difference in composition is the beryllium content, which is significantly higher in C17200. This difference affects various properties of the alloys.
Mechanical Properties
Mechanical properties are crucial for determining the suitability of these alloys for specific applications.
Property | C17510 | C17200 |
---|---|---|
Tensile Strength (MPa) | 655 – 795 | 1140 – 1310 |
Yield Strength (MPa) | 520 – 725 | 965 – 1140 |
Elongation (%) | 10 – 20 | 3 – 10 |
Hardness (HRB) | 90 – 100 | 97 – 105 |
Elastic Modulus (GPa) | 131 | 131 |
C17200 generally exhibits higher strength and hardness, while C17510 offers better ductility (elongation).
Physical Properties
Physical properties are important for applications involving thermal and electrical conductivity.
Property | C17510 | C17200 |
---|---|---|
Density (g/cm³) | 8.83 | 8.25 |
Electrical Conductivity (%IACS) | 45 – 65 | 22 – 28 |
Thermal Conductivity (W/m·K) | 208 – 300 | 105 – 130 |
Coefficient of Thermal Expansion (µm/m·°C) | 17.8 | 17.0 |
Melting Range (°C) | 870 – 980 | 870 – 980 |
C17510 demonstrates superior electrical and thermal conductivity compared to C17200.
Heat Treatment
Both alloys can be strengthened through heat treatment, but the processes and results differ:
Aspect | C17510 | C17200 |
---|---|---|
Solution Treatment | 900 – 925°C | 760 – 780°C |
Aging Temperature | 460 – 480°C | 315 – 345°C |
Aging Time | 2 – 3 hours | 2 – 3 hours |
Strength Increase | Moderate | Significant |
C17200 typically achieves a more significant increase in strength through heat treatment due to its higher beryllium content.
Corrosion Resistance
Both alloys exhibit excellent corrosion resistance, but there are some differences:
Environment | C17510 | C17200 |
---|---|---|
Atmospheric | Excellent | Excellent |
Seawater | Very Good | Very Good |
Acids | Good | Good |
Alkalis | Good | Good |
Stress Corrosion Cracking Resistance | Excellent | Very Good |
C17510 may have a slight edge in stress corrosion cracking resistance due to its lower beryllium content.
Fabrication Characteristics
The fabrication properties of these alloys are important for manufacturing processes:
Characteristic | C17510 | C17200 |
---|---|---|
Machinability | Good | Good |
Formability | Very Good | Good |
Weldability | Good | Fair |
Hot Working | Good | Good |
Cold Working | Excellent | Very Good |
C17510 generally offers better formability and weldability due to its lower beryllium content and higher ductility.
Applications
The unique properties of each alloy make them suitable for different applications:
C17510 Applications:
- Electrical connectors
- High-performance springs
- Resistance welding electrodes
- Heat sinks
- Integrated circuit lead frames
- Bearings and bushings
- Non-sparking tools
C17200 Applications:
- High-strength springs
- Diaphragms
- Bellows
- Precision instruments
- Molds for plastic injection
- Bearings in corrosive environments
- Surgical and dental instruments
Cost Considerations
The cost of these alloys can vary depending on market conditions and availability:
Factor | C17510 | C17200 |
---|---|---|
Raw Material Cost | Lower | Higher |
Processing Cost | Moderate | Moderate to High |
Overall Cost | Lower | Higher |
C17200 is generally more expensive due to its higher beryllium content.
Environmental and Safety Considerations
Both alloys contain beryllium, which requires careful handling:
Aspect | C17510 | C17200 |
---|---|---|
Beryllium Content | Lower (0.2 – 0.6%) | Higher (1.8 – 2.0%) |
Dust Hazard | Moderate | Higher |
PPE Requirements | Standard | Enhanced |
Recycling | Easier | More Complex |
The lower beryllium content in C17510 makes it somewhat easier to handle and recycle.
Comparison Summary
Characteristic | C17510 | C17200 |
---|---|---|
Strength | Good | Excellent |
Conductivity | Excellent | Good |
Ductility | Very Good | Good |
Corrosion Resistance | Excellent | Excellent |
Fabricability | Very Good | Good |
Cost | Lower | Higher |
Safety Considerations | Moderate | Higher |
Conclusion
Both C17510 and C17200 are high-performance copper-beryllium alloys with excellent combinations of strength, conductivity, and corrosion resistance. The choice between them depends on the specific requirements of the application:
- Choose C17510 when:
- Higher electrical and thermal conductivity is required
- Better formability and weldability are needed
- Cost is a significant factor
- Lower beryllium content is preferred for safety reasons
- Choose C17200 when:
- Maximum strength and hardness are crucial
- The application can tolerate lower conductivity
- The higher cost is justified by performance requirements
Understanding the similarities and differences between these alloys allows engineers and designers to make informed decisions, ensuring optimal performance and cost-effectiveness in their applications.