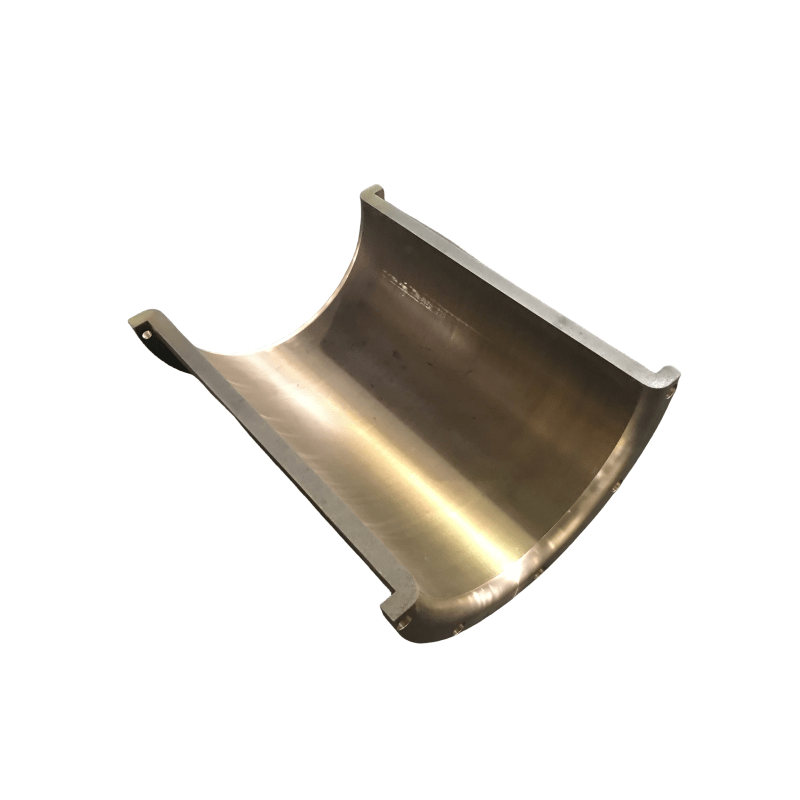
Copper alloy bearings are essential components in various industries, known for their excellent mechanical properties, corrosion resistance, and ability to withstand wear. These bearings find extensive applications in machinery, automotive systems, aerospace, and many other sectors. This article explores the diverse applications of copper alloy bearings and highlights some of the most common grades used in manufacturing.
Understanding Copper Alloy Bearings
Copper alloy bearings are typically made from copper combined with other metals, such as tin, aluminum, nickel, or zinc. This combination enhances the properties of pure copper, resulting in bearings that exhibit improved strength, wear resistance, and thermal conductivity. The unique characteristics of copper alloys make them ideal for specific applications where performance and longevity are critical.
Key Properties of Copper Alloy Bearings
- Corrosion Resistance: Copper alloys, especially those containing aluminum or nickel, offer excellent resistance to corrosion, making them suitable for use in harsh environments.
- Wear Resistance: The hardness and strength of copper alloys help reduce wear in applications where bearings are subjected to continuous motion and load.
- Thermal Conductivity: Copper alloys excel in thermal conductivity, allowing for efficient heat dissipation, which is crucial in high-performance applications.
- Machinability: Many copper alloys can be easily machined, enabling manufacturers to create precise and complex bearing designs.
- Low Friction: Copper alloy bearings often exhibit low friction coefficients, promoting smooth operation and reducing energy consumption in machinery.
Applications of Copper Alloy Bearings
1. Automotive Industry
In the automotive sector, copper alloy bearings are commonly used in various components due to their durability and resistance to wear. Applications include:
- Engine Bearings: Used in connecting rods and main bearings, copper alloy bearings provide reliable support under high loads and temperatures, contributing to overall engine performance.
- Transmission Bearings: Copper alloy bearings are utilized in automatic and manual transmission systems, ensuring smooth gear changes and longevity under constant stress.
2. Aerospace Industry
The aerospace industry demands components that can withstand extreme conditions. Copper alloy bearings are employed in:
- Landing Gear: Bearings in landing gear assemblies must endure significant stress and wear. Copper alloys provide the necessary strength and corrosion resistance.
- Engine Components: Bearings in jet engines often utilize copper alloys for their thermal and mechanical properties, ensuring reliable operation in demanding environments.
3. Industrial Machinery
In industrial machinery, copper alloy bearings play a crucial role in enhancing efficiency and reducing maintenance costs. Applications include:
- Pumps: Copper alloy bearings are commonly used in pumps, where resistance to corrosion and wear ensures reliability and extended service life.
- Compressors: Bearings in compressors benefit from the low friction and thermal conductivity of copper alloys, promoting efficient operation and longevity.
4. Marine Applications
Given their excellent corrosion resistance, copper alloy bearings are frequently used in marine applications:
- Propeller Shafts: Bearings in propeller shafts are exposed to seawater and other harsh conditions. Copper alloys help maintain functionality and reduce wear.
- Deck Machinery: Copper alloy bearings are utilized in various deck machinery, including winches and capstans, where durability is essential.
5. Construction Equipment
In construction machinery, where bearings must endure heavy loads and harsh conditions, copper alloy bearings are employed in:
- Excavators and Loaders: Copper alloy bearings provide the strength and wear resistance needed for moving parts in heavy equipment.
- Hydraulic Systems: Bearings in hydraulic pumps and actuators benefit from the corrosion resistance and thermal properties of copper alloys.
Common Grades of Copper Alloy Bearings
Several grades of copper alloys are commonly used in the manufacture of bearings, each with specific properties suited to different applications. Here are some of the most prevalent grades:
1. C93200 (SAE 660)
- Composition: Primarily composed of copper (around 83%), tin (6-7%), lead (7-8%), with trace amounts of other elements.
- Properties: Excellent wear resistance, good machinability, and good load-bearing capacity. This grade is often used in heavy-duty applications, including automotive and industrial machinery bearings.
- Applications: Commonly found in automotive engine and transmission bearings, as well as various industrial applications.
2. C93700 (SAE 841)
- Composition: Consists of copper (around 90%), tin (6-7%), and small amounts of lead and other elements.
- Properties: Offers high wear resistance and good strength, particularly suited for applications involving oscillating or rotating motion.
- Applications: Used in pump bearings, marine applications, and general-purpose industrial bearings.
3. C95400 (SAE 660)
- Composition: Contains copper (around 85%), tin (6-8%), and aluminum (5-7%).
- Properties: Excellent strength and wear resistance, along with good machinability. The addition of aluminum enhances its performance in high-load applications.
- Applications: Commonly used in heavy machinery and high-performance applications, including automotive and aerospace components.
4. C92500 (SAE 797)
- Composition: Mainly copper (around 90%), with small percentages of tin and nickel.
- Properties: High strength and good corrosion resistance, making it suitable for demanding environments.
- Applications: Found in applications where durability and resistance to harsh conditions are required, such as in marine and industrial machinery.
Conclusion
Copper alloy bearings are vital components in various industries, offering a combination of strength, corrosion resistance, and wear resistance. Their diverse applications range from automotive and aerospace to industrial machinery and marine systems, where performance and reliability are critical. The common grades of copper alloys, such as C93200, C93700, C95400, and C92500, provide tailored solutions for specific requirements, ensuring that manufacturers can meet the challenges of modern engineering.
As industries continue to innovate and evolve, the demand for high-performance bearings will only increase. Copper alloy bearings, with their proven track record and unique properties, will remain an essential choice for engineers and manufacturers seeking reliable and efficient solutions in their designs.