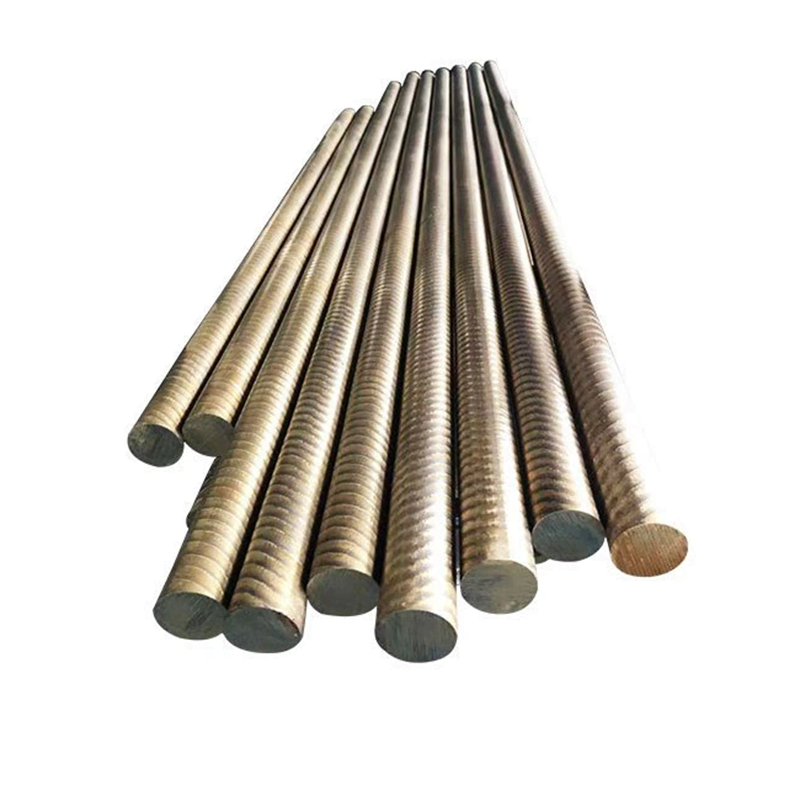
Introduction
In the world of metallurgy and materials science, certain alloys stand out for their exceptional properties and versatile applications. One such alloy is C63000, a high-strength aluminum bronze that has gained significant popularity in various industries. This article delves deep into the world of C63000, exploring its composition, properties, applications, and most importantly, its equivalents and alternatives. By understanding C63000 and its counterparts, engineers, designers, and industry professionals can make informed decisions about material selection for their specific needs.
Understanding C63000 Aluminum Bronze
Composition and Classification
C63000 is a copper-based alloy that belongs to the aluminum bronze family. Its unique composition gives it a combination of properties that make it highly desirable for many applications. The typical composition of C63000 is as follows:
- Copper: 78-82%
- Aluminum: 9-11%
- Iron: 3-5%
- Nickel: 4-6%
This specific blend of elements results in an alloy that offers an excellent balance of strength, corrosion resistance, and wear resistance. C63000 is often referred to as a “nickel-aluminum bronze” due to the significant presence of both nickel and aluminum in its composition.
Key Properties of C63000
- High Strength: C63000 exhibits exceptional strength, both at room temperature and at elevated temperatures. This makes it suitable for applications where mechanical stress is a significant factor.
- Excellent Corrosion Resistance: The alloy demonstrates superior resistance to various corrosive environments, including seawater, making it a preferred choice for marine applications.
- Wear Resistance: C63000 has good wear resistance properties, which is beneficial in applications involving friction and abrasion.
- Thermal Conductivity: While not as conductive as pure copper, C63000 still offers good thermal conductivity, making it useful in heat exchange applications.
- Non-Magnetic Properties: The alloy is non-magnetic, which is crucial for certain specialized applications.
- Machinability: C63000 can be machined with relative ease, allowing for the creation of complex parts and components.
Common Applications of C63000
Given its unique set of properties, C63000 finds applications in various industries:
- Marine Industry: Propeller shafts, pump components, valve stems, and other parts exposed to seawater.
- Oil and Gas: Drilling components, subsea equipment, and various offshore applications.
- Aerospace: Landing gear components and other high-stress parts.
- Chemical Processing: Pump components, valves, and fittings in corrosive environments.
- General Engineering: Bearings, gears, and other components requiring high strength and wear resistance.
Equivalents and Alternatives to C63000
While C63000 is an excellent alloy for many applications, there are several other alloys that can serve as equivalents or alternatives, depending on the specific requirements of the application. Understanding these alternatives is crucial for engineers and designers who may need to consider factors such as cost, availability, or slight variations in properties.
1. AMS 4640
AMS 4640 is essentially identical to C63000 but is designated under the Aerospace Material Specification (AMS) system. This designation is commonly used in the aerospace industry, where stringent material standards are crucial. AMS 4640 has the same composition and properties as C63000, making it a direct equivalent.
Key Points:
- Identical composition to C63000
- Used primarily in aerospace applications
- Meets specific aerospace industry standards
2. CuAl10Ni5Fe4 (EN Standard)
This is the European designation for an alloy very similar to C63000. The naming convention directly indicates its composition: approximately 10% aluminum, 5% nickel, and 4% iron, with the balance being copper.
Key Points:
- Very similar composition to C63000
- Commonly used in European markets
- May have slight variations in exact composition percentages
3. CA104 (CuAl10Fe5Ni5)
CA104 is another aluminum bronze alloy with a composition similar to C63000. The slight difference in iron and nickel content can result in minor variations in properties.
Key Points:
- Slightly higher iron content compared to C63000
- Similar strength and corrosion resistance
- May be more readily available in certain markets
4. C95800
C95800 is an aluminum bronze alloy with a slightly different composition compared to C63000. It typically has a lower nickel content but maintains excellent corrosion resistance and strength.
Composition:
- Copper: 79-82%
- Aluminum: 8.5-9.5%
- Iron: 3.5-4.5%
- Nickel: 4-5%
Key Points:
- Lower nickel content than C63000
- Excellent corrosion resistance, especially in seawater
- Often used in marine propellers and pump components
5. C95500
C95500 is another aluminum bronze alloy with lower nickel and iron content compared to C63000. It offers good corrosion resistance and strength, though not quite at the level of C63000.
Composition:
- Copper: 86-89%
- Aluminum: 10-11.5%
- Iron: 3-5%
- Nickel: 1-1.5%
Key Points:
- Lower nickel content results in reduced cost
- Good corrosion resistance, but not as high as C63000
- Often used in pump components and marine hardware
6. C95400
C95400 has even less nickel and iron than C63000 but is still considered an aluminum bronze with good strength and corrosion resistance.
Composition:
- Copper: 85-89%
- Aluminum: 10-11.5%
- Iron: 3-5%
- Nickel: 1% max
Key Points:
- More economical due to lower nickel content
- Good strength and corrosion resistance
- Commonly used in bearings and bushings
7. C95900
C95900 is another aluminum bronze alloy with properties similar to C63000, but with a slightly different composition.
Composition:
- Copper: 76-79%
- Aluminum: 11-13%
- Iron: 4-5.5%
- Nickel: 4.5-5.5%
Key Points:
- Higher aluminum content than C63000
- Excellent strength and corrosion resistance
- Often used in heavy-duty marine applications
Factors to Consider When Choosing an Equivalent
When selecting an equivalent or alternative to C63000, several factors should be taken into account:
- Corrosion Resistance: Different environments require different levels of corrosion resistance. While all aluminum bronzes offer good corrosion resistance, some excel in specific environments.
- Strength Requirements: The mechanical properties, including tensile strength, yield strength, and hardness, can vary among these alloys.
- Wear Resistance: If the application involves friction or abrasion, the wear resistance properties of the alloy become crucial.
- Operating Temperature: Some alloys perform better at elevated temperatures than others.
- Cost Considerations: The price of these alloys can vary significantly, primarily due to differences in nickel content.
- Availability: Depending on your location and supplier, some alloys may be more readily available than others.
- Specific Industry Standards: Certain industries, like aerospace or marine, may have specific requirements or preferred alloys.
- Machinability: If the part requires extensive machining, the ease of machining becomes an important factor.
- Weldability: For applications requiring welding, the weldability of the alloy should be considered.
- Environmental Impact: Some industries may have specific requirements regarding the environmental impact of materials used.
Conclusion
C63000 aluminum bronze is a remarkable alloy with a wide range of applications across various industries. Its unique combination of strength, corrosion resistance, and wear resistance makes it a popular choice for demanding environments, particularly in marine and aerospace applications.
However, the world of aluminum bronzes is diverse, offering several alternatives and equivalents to C63000. Alloys like AMS 4640, CuAl10Ni5Fe4, C95800, and others provide options for engineers and designers to fine-tune their material selection based on specific application requirements, cost considerations, and availability.
Understanding these alternatives allows for more flexibility in design and procurement processes. It’s crucial to carefully evaluate the specific needs of each application and consider factors such as corrosion resistance, strength, cost, and industry standards when selecting an equivalent to C63000.
As materials science continues to advance, we may see further developments in aluminum bronze alloys, potentially offering even more specialized options for various applications. Staying informed about these developments and understanding the nuances of different alloy compositions will remain crucial for professionals working with these materials.
In the end, while C63000 sets a high standard in the world of aluminum bronzes, the availability of equivalents and alternatives ensures that there’s likely an optimal solution for almost any engineering challenge requiring the unique properties of these versatile alloys.