Introduction
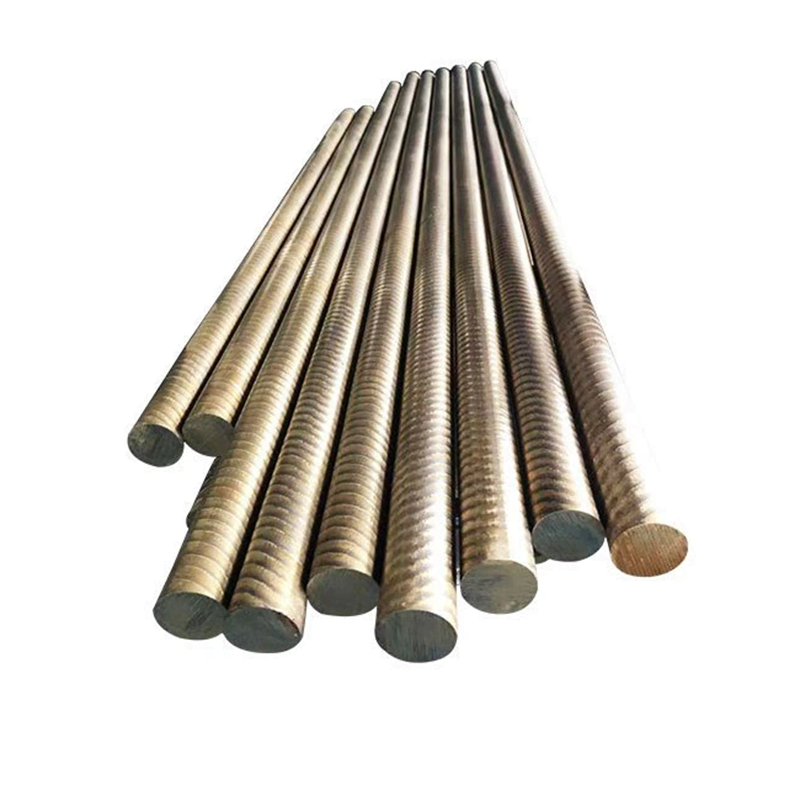
Key Points | Details |
---|---|
Material Overview | C63000 aluminum bronze is a high-strength copper alloy |
Composition | Primarily copper with aluminum, iron, and nickel |
Key Properties | High strength, excellent corrosion resistance, good wear resistance |
C63000 aluminum bronze has gained significant traction in the aerospace industry due to its unique combination of properties. This alloy offers a blend of high strength, excellent corrosion resistance, and good wear characteristics, making it an ideal choice for various aerospace applications.
Material Properties Relevant to Aerospace
Property | Relevance to Aerospace |
---|---|
High Strength-to-Weight Ratio | Critical for reducing overall aircraft weight |
Corrosion Resistance | Essential in harsh atmospheric conditions |
Fatigue Resistance | Important for components subject to cyclic loading |
Wear Resistance | Crucial for moving parts and high-friction applications |
Thermal Stability | Maintains properties across a wide temperature range |
The aerospace industry demands materials that can withstand extreme conditions while maintaining structural integrity. C63000 aluminum bronze meets these requirements, offering a balance of strength, durability, and reliability.
Specific Applications in Aerospace
- Landing Gear Components
Application | Benefits of C63000 |
---|---|
Bushings and Bearings | High wear resistance and load-bearing capacity |
Hydraulic Cylinder Parts | Corrosion resistance in hydraulic fluids |
Structural Components | High strength and fatigue resistance |
Landing gear systems experience high stress and cyclic loading during takeoff and landing. C63000’s high strength and excellent fatigue resistance make it an ideal material for critical components in these systems.
- Engine and Propulsion Systems
Component | Advantage of C63000 |
---|---|
Valve Guides | Wear resistance at high temperatures |
Thrust Washers | High load-bearing capacity |
Fuel System Components | Corrosion resistance to various fuels |
The alloy’s ability to maintain its properties at elevated temperatures makes it suitable for various engine components, particularly in areas where wear resistance is crucial.
- Fasteners and Fittings
Application | C63000 Benefit |
---|---|
Bolts and Nuts | High strength and corrosion resistance |
Hydraulic Fittings | Excellent sealing properties and durability |
Electrical Connectors | Good conductivity and corrosion resistance |
The corrosion resistance of C63000 is particularly valuable for fasteners and fittings exposed to various environmental conditions.
- Actuator Components
Part | Advantage |
---|---|
Gears | High wear resistance and strength |
Shafts | Excellent fatigue resistance |
Bushings | Low friction and good wear characteristics |
Actuators in aerospace applications often require materials that can withstand high loads and frequent movement. C63000’s properties make it well-suited for these demanding applications.
- Structural Support Elements
Application | C63000 Benefit |
---|---|
Brackets | High strength-to-weight ratio |
Mounting Plates | Good machinability for complex shapes |
Load-Bearing Joints | Excellent fatigue and corrosion resistance |
The alloy’s strength and corrosion resistance make it suitable for various structural support elements throughout aircraft and spacecraft.
Manufacturing Considerations
Process | Advantage for Aerospace |
---|---|
Precision Machining | Ability to create complex, high-tolerance parts |
Forging | Enhances strength and grain structure |
Heat Treatment | Allows tailoring of properties for specific applications |
Welding | Can be welded with proper techniques, enabling complex assemblies |
The manufacturing versatility of C63000 allows for the creation of complex aerospace components with high precision and consistency.
Comparative Advantages
Aspect | Advantage over Other Materials |
---|---|
Weight | Lighter than steel, heavier but stronger than aluminum |
Corrosion Resistance | Superior to many steels and aluminum alloys |
Thermal Properties | Better thermal conductivity than stainless steel |
Nonmagnetic Properties | Useful in sensitive electronic environments |
When compared to other materials commonly used in aerospace, C63000 offers a unique set of advantages that make it preferable for certain applications.
Challenges and Limitations
Challenge | Description |
---|---|
Cost | More expensive than some alternative materials |
Weight | Heavier than aluminum, limiting use in weight-critical applications |
Specialized Processing | Requires specific expertise for optimal manufacturing |
While C63000 offers numerous advantages, its higher cost and weight compared to some alternatives can limit its use in certain aerospace applications.
Future Trends and Research
Area of Focus | Potential Impact |
---|---|
Additive Manufacturing | Enabling more complex geometries and reducing waste |
Surface Treatments | Enhancing wear and corrosion resistance further |
Alloy Optimization | Tailoring compositions for specific aerospace needs |
Composite Integration | Exploring hybrid materials combining C63000 with composites |
Ongoing research aims to expand the capabilities and applications of C63000 in aerospace, focusing on overcoming current limitations and enhancing its properties.
Regulatory and Certification Aspects
Aspect | Importance |
---|---|
Material Certification | Ensuring consistency and reliability for aerospace use |
Quality Control | Rigorous testing and documentation for aerospace standards |
Environmental Compliance | Meeting regulations on material use and disposal |
The use of C63000 in aerospace applications requires adherence to strict regulatory standards and certification processes to ensure safety and reliability.
Conclusion
C63000 aluminum bronze has established itself as a valuable material in the aerospace industry due to its exceptional combination of properties. Its high strength, excellent corrosion resistance, and good wear characteristics make it suitable for a wide range of applications, from landing gear components to engine parts and structural elements. While challenges such as higher cost and weight compared to some alternatives exist, ongoing research and development continue to expand the potential of this alloy in aerospace applications. As the aerospace industry evolves, seeking materials that can meet increasingly demanding performance requirements, C63000 aluminum bronze is likely to play an increasingly important role in future aircraft and spacecraft designs.