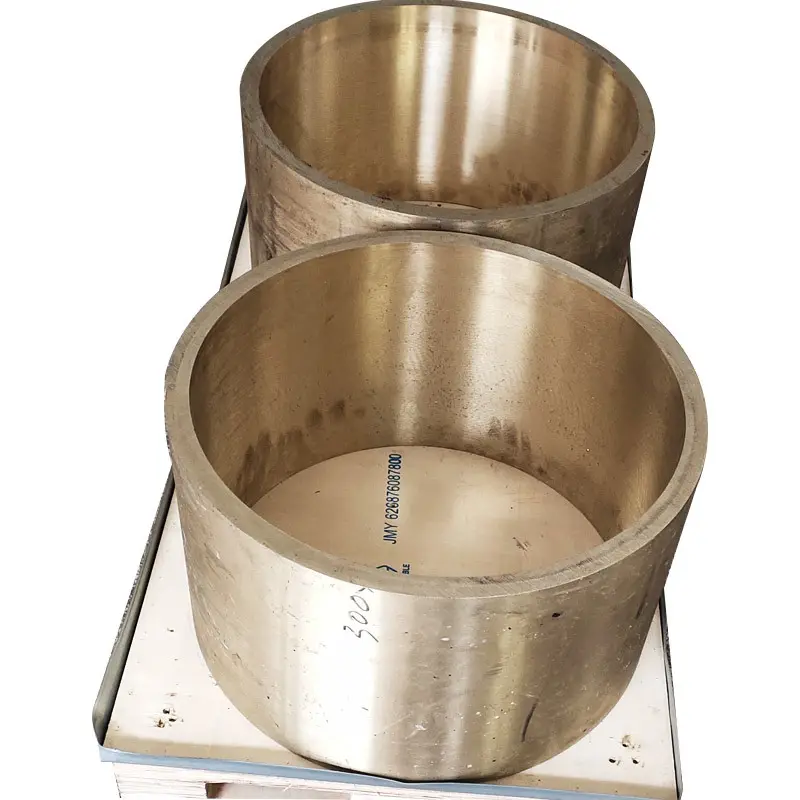
1. Introduction
In modern engineering, material selection often determines product performance and lifespan. Aluminum bronze bushings, as high-performance alloy materials, are widely used in various demanding environments due to their excellent overall performance. This article will comprehensively and deeply explore the characteristics, applications, production processes, and selection considerations of aluminum bronze bushings, providing a comprehensive reference for engineers and decision-makers.
2. Composition and Classification of Aluminum Bronze Bushings
2.1 Basic Composition
Aluminum bronze bushings are mainly composed of copper (Cu) and aluminum (Al), with aluminum content typically ranging from 5% to 11%. Other elements may be added to improve specific properties.
2.2 Common Aluminum Bronze Alloy Composition Table
Alloy Type | Copper (Cu) | Aluminum (Al) | Iron (Fe) | Nickel (Ni) | Manganese (Mn) | Others |
---|---|---|---|---|---|---|
C95200 | 88% | 9% | 3% | – | – | – |
C95400 | 85% | 11% | 4% | – | – | – |
C95500 | 81% | 10% | 4% | 5% | – | – |
C95800 | 82% | 9% | 4% | 4% | 1% | – |
2.3 Classification
Aluminum bronze bushings can be classified into the following categories based on their composition and performance characteristics:
- Single-phase aluminum bronze: Aluminum content below 8%
- Dual-phase aluminum bronze: Aluminum content between 8% and 11%
- Complex aluminum bronze: Addition of other elements such as iron, nickel, etc.
3. Main Characteristics of Aluminum Bronze Bushings
Aluminum bronze bushings exhibit a series of excellent performance characteristics due to their unique composition ratio:
Characteristic | Description | Advantage |
---|---|---|
Strength and Hardness | Higher than ordinary bronze | Suitable for high-load environments |
Wear Resistance | Excellent | Extends service life, reduces maintenance |
Corrosion Resistance | Particularly outstanding in seawater environments | Suitable for marine engineering and chemical industries |
Friction Coefficient | Low | Improves efficiency, reduces energy loss |
Thermal Conductivity | Good | Aids in heat dissipation, extends service life |
Magnetism | Some compositions are non-magnetic | Suitable for special application scenarios |
Fatigue Resistance | Excellent | Suitable for cyclic load conditions |
Impact Resistance | Good | Suitable for dynamic load environments |
4. Application Fields of Aluminum Bronze Bushings
Due to their excellent performance, aluminum bronze bushings are widely used in multiple industrial fields:
4.1 Overview of Application Fields
Industry | Applied Parts | Application Advantages |
---|---|---|
Shipbuilding | Propellers, bearings, valves | Seawater corrosion resistance, high strength |
Petrochemical | Pump bodies, valves, bearings | Corrosion resistance, high temperature and pressure resistance |
Aerospace | Precision bearings, high-performance gears | High strength, low weight ratio |
Mechanical Manufacturing | Sliding bearings, gears, worm gears | Wear-resistant, good self-lubrication |
Construction | High-end decorative parts, door and window fittings | Aesthetic, durable |
Water Conservancy | Water pumps, valves | Corrosion resistance, long lifespan |
Mining | Bearings, gears | Wear-resistant, impact-resistant |
4.2 Typical Application Cases
- Marine Engineering: In seawater desalination plants, aluminum bronze bushings are widely used in high-pressure pumps and valves, significantly extending equipment lifespan due to their excellent seawater corrosion resistance.
- Aerospace: Aluminum bronze bearings used in the landing gear system of certain aircraft models have significantly improved system reliability and service life.
- Heavy Machinery: Using aluminum bronze bushings in the slewing bearings of large excavators effectively solves the problem of wear in traditional materials under high-load and high-pollution environments.
5. Production Processes of Aluminum Bronze Bushings
The production process of aluminum bronze bushings directly affects their final performance, mainly including the following methods:
5.1 Comparison of Production Processes
Process | Advantages | Disadvantages | Suitable Scenarios |
---|---|---|---|
Casting | Can produce complex shapes, relatively low cost | May have air holes, relatively low strength | Large parts, complex shapes |
Forging | High density, good strength | Higher cost, shape limitations | High strength requirements, simple shapes |
Powder Metallurgy | Precise dimensions, high material utilization | Large equipment investment, high batch requirements | Small precision parts |
Centrifugal Casting | Good density, suitable for tubular parts | Strong equipment specificity, relatively high cost | Large bearing bushings, sleeves |
5.2 Heat Treatment
Heat treatment is an important step in optimizing the performance of aluminum bronze bushings, mainly including:
- Annealing: Improves material plasticity, reduces internal stress
- Quenching: Increases hardness and strength
- Aging: Further increases strength and hardness, improves dimensional stability
6. Performance Comparison of Aluminum Bronze Bushings
To better understand the advantages of aluminum bronze bushings, we compare them with other commonly used bearing materials:
Performance Indicator | Aluminum Bronze | Tin Bronze | Stainless Steel | Nylon |
---|---|---|---|---|
Wear Resistance | ★★★★☆ | ★★★☆☆ | ★★★★☆ | ★★☆☆☆ |
Corrosion Resistance | ★★★★★ | ★★★☆☆ | ★★★★☆ | ★★★★★ |
Strength | ★★★★☆ | ★★★☆☆ | ★★★★★ | ★★☆☆☆ |
Thermal Conductivity | ★★★★☆ | ★★★★☆ | ★★★☆☆ | ★☆☆☆☆ |
Self-lubrication | ★★★★☆ | ★★★☆☆ | ★☆☆☆☆ | ★★★★☆ |
Cost | ★★☆☆☆ | ★★★☆☆ | ★★☆☆☆ | ★★★★☆ |
7. Selection and Maintenance of Aluminum Bronze Bushings
7.1 Selection Considerations
When selecting aluminum bronze bushings, the following factors need to be considered:
- Application Environment: Temperature, humidity, corrosive media, etc.
- Load Conditions: Static load, dynamic load, impact load, etc.
- Operating Speed: Low speed, medium speed, high speed
- Lubrication Conditions: Dry running, oil lubrication, water lubrication, etc.
- Cost Budget: Initial cost vs. long-term usage cost
- Maintenance Requirements: Maintenance frequency, ease of maintenance
7.2 Maintenance Recommendations
To ensure optimal performance and longevity of aluminum bronze bushings, it is recommended to follow these maintenance principles:
- Regular Inspection: Check for wear conditions and signs of corrosion
- Keep Clean: Remove dirt and impurities to prevent accelerated wear
- Proper Lubrication: Choose appropriate lubrication methods based on the usage environment
- Avoid Overloading: Strictly adhere to design load limits
- Corrosion Protection: Apply anti-corrosion coatings on non-working surfaces
- Timely Replacement: Replace when wear exceeds allowable range
8. Future Development Trends of Aluminum Bronze Bushings
With the continuous advancement of industrial technology, the development of aluminum bronze bushings also shows new trends:
- Application of Nanotechnology: Further improve the performance of aluminum bronze bushings through nano-material modification
- Intelligent Monitoring: Integrate sensors to achieve real-time monitoring of bearing operating conditions
- Green Manufacturing: Develop more environmentally friendly production processes to reduce energy consumption and pollution emissions
- Customized Production: Utilize 3D printing technology to achieve rapid customized production
- Composite Materials: Develop aluminum bronze-based composite materials to further optimize performance
9. Conclusion
As a high-performance engineering material, aluminum bronze bushings demonstrate excellent overall performance in various harsh environments. Their superior wear resistance, corrosion resistance, and mechanical strength make them the material of choice for many high-demand application scenarios. Although the initial cost may be higher, considering their long-term performance and reliability, aluminum bronze bushings often bring higher returns on investment.
When selecting and using aluminum bronze bushings, it is necessary to comprehensively consider factors such as application environment, load conditions, and maintenance requirements. At the same time, with the continuous development of new technologies, the performance and application range of aluminum bronze bushings are expected to further expand, providing more reliable material support for industrial development.
For engineers and decision-makers, an in-depth understanding of the characteristics and applications of aluminum bronze bushings will help make optimal material choices in appropriate scenarios, thereby improving product performance, extending service life, and ultimately achieving higher economic benefits and technological advantages.