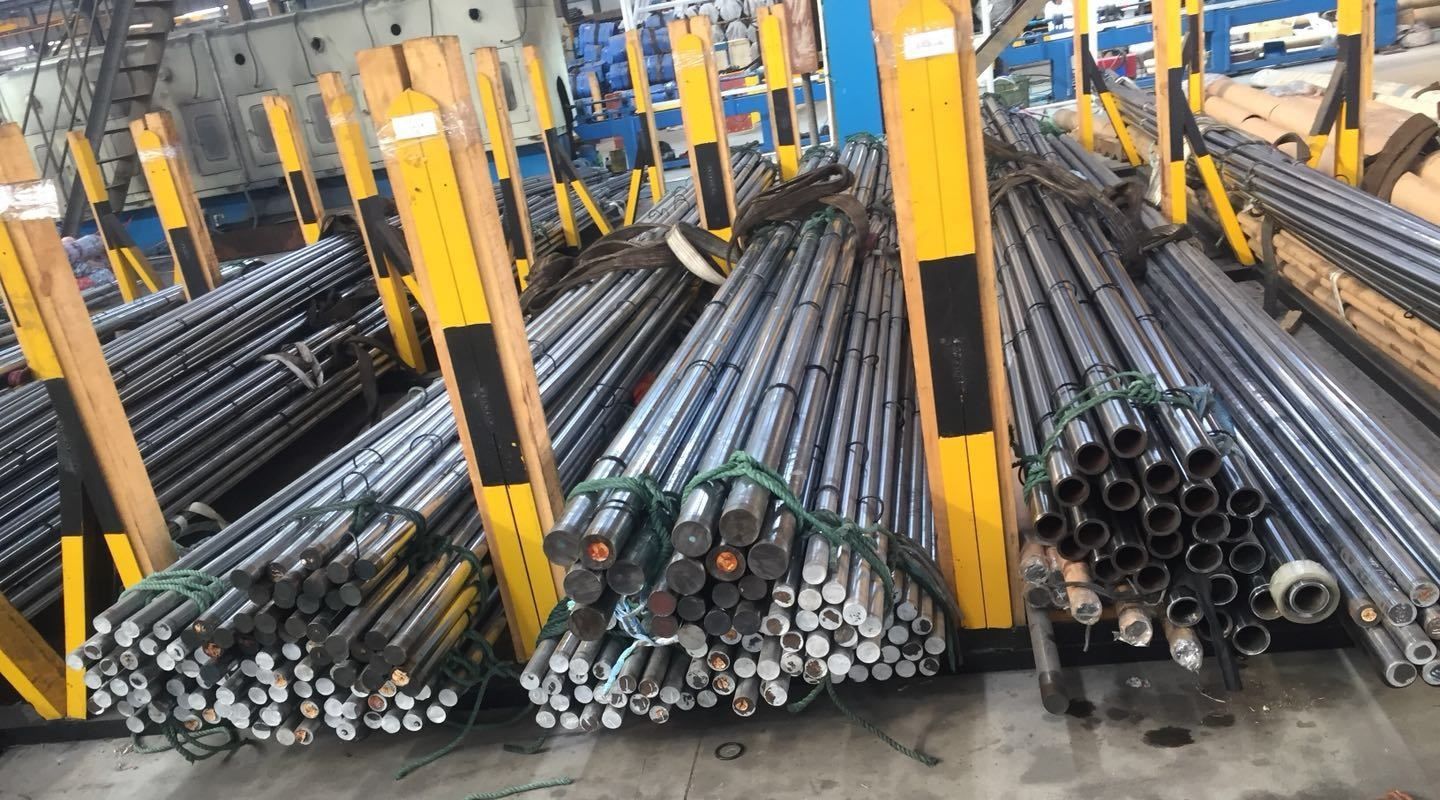
محتوى هذه الصفحة مستمد من Iqsdirectory.com
مقدمة
هذا هو الدليل الأكثر شمولاً للتزوير على البارد المتاح عبر الإنترنت.
تتناول هذه المقالة المواضيع التالية:
- ما هو التزوير البارد وكيف يعمل
- Cold forging benefits & disadvantages
- تزوير الساخنة مقابل تزوير الباردة
- المعادن والمعدات/الآلات المستخدمة
- تطبيقات تزوير الباردة
- وأكثر…
الفصل الأول – ما هو الحدادة على البارد وكيف تعمل؟
Cold forging is a metal shaping & manufacturing process in which bar stock is inserted into a die and squeezed into a second closed die. The process, completed is at room temperature or below the metal‘s recrystallization temperature to form a metal into a desired shape or configuration.
تعتبر عملية التشكيل على البارد عملية فعالة واقتصادية لتشويه المعادن لإنتاج كميات كبيرة من الأجزاء بتكلفة منخفضة. هناك ثلاث طرق للطرق تختلف وفقًا لدرجة الحرارة، والتي يمكن أن تكون باردة أو دافئة أو ساخنة وتتضمن استخدام المطارق أو القوالب أو المكابس لتشكيل المعادن أو ضغطها أو تشويهها أو دحرجتها. لا ينبغي الخلط بين التشكيل على البارد والتصنيع الآلي أو الصب لأن النتيجة النهائية هي منتج أقوى وأعلى جودة.
على عكس الطرق الدافئة أو الساخنة، فإن الطرق الباردة تعمل على تشكيل وتشوه مخزون القضبان في درجة حرارة الغرفة باستخدام قوة ضاغطة موضعية. اعتمادًا على متطلبات تصميم الأجزاء، قد تمر قطعة العمل عبر قوالب متعددة أو يتم ضربها عدة مرات متتالية لتحقيق الشكل المناسب.
الفصل الثاني – كيفية عمل الحدادة على البارد
ترجع التكلفة المنخفضة للتزوير على البارد إلى انخفاض تكاليف العمالة وإزالة المعالجة الثانوية. يتم إنتاج الأجزاء بسرعة وكفاءة بمعدلات تصل إلى 1000 قطعة في الساعة، مما يقلل من تكلفة الوحدة. الإنتاج هو ببساطة مسألة إدخال قطعة معدنية والسماح للآلات بالقيام بالعمل بسرعة وبتكلفة معقولة.
تتميز المنتجات النهائية من الطرق البارد بتشطيبات سطحية مثالية وثبات محسّن للأبعاد كما هو موضح في الصورة أدناه. تعمل العمليات المختلفة على تعزيز قوة ومتانة قطعة العمل لإنتاج منتجات أو أجزاء طويلة الأمد.
عملية تزوير الباردة
الخطوة 1: مواد التشحيم
– قبل الحدادة، تتم معالجة قطعة العمل بمادة تشحيم لمنعها من الالتصاق بالقالب وللحفاظ عليها باردة أثناء عملية التشكيل حيث أن التشوه يمكن أن ينتج درجات حرارة تتراوح من 250 درجة إلى 450 درجة.
الخطوة 2: إدخال القطعة المعدنية
– يتم وضع القطعة المعدنية على قالب يكون على شكل الجزء النهائي . قد يحتوي القالب على قسمين، أحدهما متصل بالمطرقة والآخر أسفل قطعة العمل. المطرقة هي الجزء العلوي وآلية الضرب التي تنتج القوة لتشويه القطعة المعدنية.
الخطوة 3: السكتة الدماغية
– يمكن أن يتم ضرب قطعة الشغل، أو السكتة الدماغية، بثلاث آليات – هيدروليكية، أو هوائية، أو ميكانيكية. تقوم كل تقنية بتحريك عمود، مع المطرقة عليه، لأسفل بقوة كبيرة على قطعة العمل لإنشاء الشكل المطلوب. يحدث هذا في نطاق ميلي ثانية. في بعض الحالات، قد يلزم إسقاط المطرقة عدة مرات متتالية للحصول على الشكل والشكل الدقيقين.
الخطوة 4: فلاش
- الفلاش عبارة عن معدن زائد موجود حول القالب أو مجموعة القوالب. ويمتد من جسم المطروق على شكل صفيحة رفيعة تلتقي فيها القوالب ويتم إزالتها أثناء التشذيب. يحد الفلاش من تدفق المعدن مما يضمن الحصول على انطباع مثالي. يعد وجود الفلاش أمرًا ضروريًا لإجبار المعدن على ملء القالب بالكامل.
الخطوة 5: إزالة الجزء
– تعتمد طريقة إزالة الجزء على نوع العملية. تستخدم معظم الشركات المصنعة الحديثة الأتمتة لإزالة الجزء بواسطة ناقل أو يد آلية. يعد هذا إجراءً آخر لتوفير التكلفة ويلغي الحاجة إلى معالجة المواد.
الخطوة 6: بعد التشكيل
– كما هو الحال مع الأجزاء الأخرى من العملية، يمكن أن يتخذ هذا أشكالاً عديدة. بالنسبة للأجزاء التي تتطلب قالبًا واحدًا وضربة واحدة، يتم قطع الجزء وإرساله للشحن. في حالة الأجزاء التي لها جوانب متعددة، يتم نقلها إلى عمليات قالب أخرى لإضافة ميزات. عادةً ما تكون حركة القالب من محطة إلى أخرى آلية. مع الأجزاء الأكبر حجمًا، يتم استخدام طرق ميكانيكية أخرى قد تتضمن رافعة شوكية أو رافعة شوكية.
الفصل الثالث – فوائد الحدادة على البارد
هناك ست مزايا رئيسية للحواف الباردة تمت مناقشتها بالتفصيل في هذا الفصل. وهي تشمل:
- فعالة من حيث التكلفة
- إنتاج أسرع
- صديقة للبيئة
- أداء متفوق للمنتج
- ارتفاع إنتاجية الإنتاج
- مجموعة واسعة من المعادن
توضح المعلومات الواردة أدناه بعض فوائد التشكيل على البارد وسبب استخدامه على نطاق واسع. الفصل الثالث عبارة عن مقارنة بين الحدادة على البارد والحدادة على الساخن ومزايا كل منهما.
فعالة من حيث التكلفة:
تعتبر عملية الطرق على البارد منخفضة التكلفة بسبب 3 عوامل - المعالجة المسبقة ودرجة الحرارة والتشطيب. في الطرق الأخرى لتشكيل المعادن، يجب أن تخضع قطعة العمل لشكل من أشكال المعالجة المسبقة مثل تسخينها. تُستخدم الأفران أو الأفران أو الكهرباء عادةً لرفع درجة حرارة المعدن فوق نقطة إعادة التبلور. فهي مكلفة للصيانة، وتنتج الملوثات، وتستغرق وقتا طويلا.
في عملية التشكيل على البارد، بمجرد معالجة قطعة العمل، تكون كاملة وتتطلب الحد الأدنى من التشطيب، مما يوفر تكلفة العمالة.
يوفر التشكيل على البارد ما يصل إلى 70% من تكاليف الإنتاج نظرًا لوجود القليل جدًا من النفايات والخردة.
إنتاج أسرع:
الحدادة على البارد هي عملية بسيطة حيث يتم وضع قطعة العمل مباشرة في آلة الحدادة لإنتاج الجزء النهائي على الفور. يستخدم المنتجون المعاصرون الأتمتة لتحميل قطعة العمل وإزالتها من المطبعة. كما ترون في هذا الرسم البياني، يتم إدخال المعدن إلى الآلة، ومعالجته، ثم نقله. مقدار الوقت بين الدخول والانتهاء أقل من ثانية.
صديقة للبيئة:
السبب الرئيسي وراء كونها صديقة للبيئة هو إزالة الحاجة إلى الحرارة لأن الأبخرة والدخان الناتج عن الأفران ينتج عنه انبعاثات كربونية كبيرة. وهذا يقلل أيضًا من التكلفة نظرًا لأن المنتجين لا يضطرون إلى تركيب معدات تنقية الهواء وتنظيفه.
أداء المنتج المتفوق:
تنتج عملية التشكيل على البارد منتجات ذات أداء فائق لأنها تعيد ترتيب البنية الحبيبية لقطعة العمل لتتبع تكوين الجزء النهائي.
يزيل ردود الفعل السلبية المحتملة:
يمكن أن يؤدي تشغيل المعدن إلى ظهور مجموعة متنوعة من المشكلات المحتملة. يزيل التشكيل على البارد بعض التأثيرات السلبية مثل إجهاد المسامية عن طريق زيادة القوة الإجمالية للمعدن وإزالة خطر فقدان سلامة المواد.
زيادة الجودة والعمر الطويل:
الأجزاء المطروقة على البارد قادرة على التعامل مع الضغط العالي. عندما يتم دفع قطعة العمل إلى ما هو أبعد من حدود إنتاجيتها أو مرونتها، فإنها لا تزال قادرة على الاحتفاظ بشكلها المتغير.
الاحتفاظ بالتسامح جزء:
يتم الحفاظ على التفاوتات الحرجة والوثيقة للأجزاء طوال فترة الإنتاج. لقد تم إعادة إنتاجها بأدق التفاصيل بحيث يكون كل جزء نسخة طبق الأصل من الجزء الأول.
حرية التصميم:
على عكس العمليات الأخرى، يتيح التشكيل على البارد حرية التصميم حيث يمكن إنتاج خطوط وأشكال معقدة تتطلب العديد من الطرق الثانوية المختلفة والمكلفة في العمليات الأخرى.
إنتاجية عالية:
على الرغم من أنه قد تكون هناك اختلافات بين طرق الإنتاج بالطرق على البارد، إلا أن سرعة التصنيع العالية للطرق على البارد يمكن أن تنتج ما يصل إلى 50 قطعة في الدقيقة وحتى أكثر من 400. الشيء الوحيد الذي يؤثر على سرعة العملية هو حجم الجزء.
مجموعة واسعة من المعادن:
يمكن تشكيل مجموعة واسعة من المعادن، والتي تشمل المعادن الصلبة مثل الفولاذ الكربوني وسبائك الفولاذ والفولاذ المقاوم للصدأ بالإضافة إلى المعادن الناعمة مثل الألومنيوم والنحاس والنحاس.
هذه الصورة عبارة عن عينة من البراغي التي تم إنتاجها عن طريق الطرق البارد. تم تصنيع كل من البراغي المختلفة من معدن مختلف. وتشمل تلك المصنوعة من النحاس والنحاس والألمنيوم والفولاذ.
الفصل الرابع - تزوير الساخنة مقابل الباردة
الفرق بين الطرق الساخن والطرق البارد هو درجة الحرارة: فالطرق على البارد يجهد ويجهد المعادن في درجة حرارة الغرفة، في حين أن الطرق على الساخن يسخن المعادن بالقرب من أو عند نقاط انصهارها.
إن مفتاح نطاق درجة الحرارة هو إعادة التبلور: يتم إجراء عملية التشكيل على البارد قبل إعادة التبلور بينما تقوم عملية التشكيل على الساخن بتسخين المعدن فوق نقطة إعادة التبلور.
يعتمد اختيار الطرق الباردة مقابل الطرق الساخنة على:
- معدات المصنعين والآلات: يتخصص المنتجون في عملية واحدة أو أخرى لتحقيق أقصى استفادة من معداتهم.
- طلب العميل: أثناء مرحلة تصميم تطوير الأجزاء، يتخذ المهندسون القرار بشأن أفضل عملية لإنتاج تصميماتهم نظرًا لأن الطرق الباردة والساخنة لها حدودها.
- أنواع الأجزاء المنتجة: في كثير من الأحيان، يتم تحديد القيود المتعلقة باختيار العملية الصحيحة من خلال تصميم الجزء، حيث لا يمكن تشكيل أجزاء معينة إلا على الساخن بينما تكون الأجزاء الأخرى مثالية للتزوير على البارد. تتميز تصميمات الأجزاء المطروقة على البارد بالبساطة دون تفاصيل معقدة، بينما يمكن للطرق الساخنة أن تنتج قطعًا ذات ميزات دقيقة للغاية ودقيقة للغاية.
- متطلبات تكلفة أقل: يختار المصنعون، كلما أمكن ذلك، التشكيل على البارد لأنه يتطلب معدات أقل ولا يشمل التدفئة، مما يقلل بشكل كبير من التكلفة الإجمالية للإنتاج.
تزوير ساخن
يتم تنفيذ الحدادة على الساخن عند درجات حرارة عالية بشكل استثنائي تتراوح بين 700 درجة مئوية أو 1292 درجة فهرنهايت إلى 1000 درجة مئوية أو 1832 درجة فهرنهايت. تساعد درجات الحرارة المتزايدة على تجنب الإجهاد والتصلب بالإضافة إلى تقليل تدفق الضغط وكمية الطاقة اللازمة للتشوه والتشكيل. تشكيل المعادن. وبمجرد أن تبرد المعادن، فإنها تحتفظ بشكلها المشوه. يتم استخدام المكابس الهيدروليكية والهوائية والميكانيكية في عملية التشكيل.
خصائص تزوير الساخنة:
يموت أو قوالب:
إحدى النفقات الرئيسية للطرق على الساخن هي التكلفة المطلوبة لإنتاج القوالب والقوالب المصنوعة من الفولاذ المقوى المصمم هندسيًا لتحمل درجات الحرارة القصوى، وقادر على مقاومة التعب، كما يتمتع بالليونة والمتانة وقوة الشد.
أشكال الحدادة الساخنة:
على الرغم من أن العديد من طرق الحدادة على الساخن تشبه طرق الحدادة على البارد، إلا أن الطرق الأخرى تشمل التشكيل بالغاز، والتبريد بالقالب، والتشكيل بالسحب، والتساوي الحراري.
درجة حرارة المعدن:
يحدد نوع العملية درجة حرارة المعدن عند تشكيله. في بعض العمليات، يتم صهر المعدن بالكامل وصبه في قالب أو دفعه خلال قالب. وفي حالات أخرى، يتم تلدينه وتشكيله بواسطة قالب أو قالب تحت الضغط والضغط.
العوامل البيئية الخطرة:
العيب الأكبر هو كمية الملوثات الناتجة عن عملية التسخين. لقد كانت هذه مشكلة رئيسية منذ بدايتها خلال الثورة الصناعية الأولى وكانت مشكلة واجهها المنتجون باستمرار على مر السنين.
تسخين المعادن:
يجب تسخين الأجزاء فوق نقطة إعادة التبلور، والتي تزيد عن 300 درجة فهرنهايت ويمكن أن تصل إلى آلاف الدرجات. مطلوب أفران أو أفران كبيرة للوصول إلى درجات الحرارة المناسبة.
الوقت المعني:
تتطلب الطبيعة المعقدة للطرق الساخن وقتًا لتسخين المعدن ومعالجته وتبريده. على الرغم من أن الختم أو التشوه أو التشكيل الفعلي يستغرق تقريبًا نفس الوقت الذي يستغرقه التشكيل على البارد، إلا أن عمليات التسخين والتبريد تتطلب رعاية وإدارة دقيقة لفترات طويلة.
نتائج تزوير الساخنة:
يؤدي تسخين وتبريد المعادن إلى زيادة قوتها وصلابتها وليونتها، ولكنه يقلل من صلابتها. أثناء عملية التبريد، يمكن للمعادن أن تتشوه وتفقد شكلها.
التحجيم:
يمكن أن يؤدي التشكيل الساخن إلى أكسدة تؤدي إلى تقشر، مما قد يؤدي إلى تغير لون سطح المعدن مما يجعل من الصعب صقله.
التشطيب:
يجب الانتهاء من الأجزاء لإزالة التشوهات والعيوب والأخطاء الناتجة عن عملية التسخين. تتطلب هذه العمليات الثانوية عمالة كثيفة وتتطلب عدة أنواع من المعدات المتخصصة.
تزوير الباردة
درجة الحرارة التي يتم فيها الحدادة هي ما يفصل الحدادة الباردة عن الحدادة الساخنة. لكي يتم تشكيل جزء ما على الساخن، يتم تسخينه إلى درجة حرارة أعلى من نقطة إعادة التبلور، مما يغير بنيته الدقيقة. عندما يتم تسخينه، يتم التخلص من الضغط الداخلي والقوة لجعله أكثر ليونة. لا يتطلب التشكيل على البارد تسخينًا، مما يسمح للمعدن بالاحتفاظ بقوته وبنيته الدقيقة.
خصائص المطروقات الباردة هي كما يلي:
درجة حرارة التشكيل:
يتم تشكيل المعادن في درجة حرارة الغرفة تحت نقطة إعادة بلورتها، الأمر الذي له فائدة خفض التكاليف وتجنب تكلفة الأفران.
سرعة:
تتراوح السرعات من سبع قطع في الدقيقة للآلات ذات الحجم المنخفض إلى 400 قطعة في الدقيقة للآلات ذات الحجم الكبير.
معدات:
يتم إجراء الحدادة على البارد باستخدام آلات مصممة لتشكيل المعدن وتشمل الضغط والثني والقص والسحب. تتوفر المعدات في مجموعة واسعة من الأسعار اعتمادًا على كمية التكنولوجيا وحجمها.
يكلف:
وفورات في التكاليف هي من المواد والسرعة. يأتي التوفير في المواد من الكمية الصغيرة من الخردة المنتجة، والتي تصل إلى 70%. وبما أن الأجزاء يتم إنتاجها بمعدل سريع للغاية، فإن تكلفة الوحدة منخفضة بشكل ملحوظ.
العوامل البيئية:
لا يتم إنتاج أي انبعاثات أو ملوثات كما يمكن رؤيته في هذه الآلة أدناه من Stalcop. كل شيء مكتفي بذاته ومغلق. يتم التخلص من الكربون والملوثات الأخرى لأنه لا توجد حاجة لتسخين المعدن.
نتائج تزوير الباردة:
كما هو موضح في الرسم البياني أدناه، يتم إعادة ترتيب البنية الحبيبية للمعادن لمتابعة تدفق الجزء النهائي، مما يؤدي إلى التخلص من إجهاد المسامية، وزيادة قوة القص، وتقليل أي خطر على سلامة المواد. من خلال إجهاد المعدن، يصبح أقوى وأكثر مرونة. العيب هو أنه بمجرد تشكيل المعدن على البارد فإنه يفقد ليونته ويصبح أكثر هشاشة.
التحجيم:
قبل تشكيل المعدن، من المهم إزالة أي قشور مثل الصدأ أو التآكل الذي قد ينشأ أثناء التخزين. إذا تركت دون إزالة، فإن الجزء سيكون له نفس التدهور كما هو موجود في الطرق الساخنة.
التشطيب:
هناك القليل من التشطيب المطلوب. بمجرد معالجة الجزء، يصبح جاهزًا للاستخدام أو الشحن.
عيوب تزوير الباردة
تزوير الباردة ليست مثالية. مثل كل طريقة إنتاج، هناك قيود وقيود على التشكيل على البارد والتي يجب عليك مراعاتها قبل اختيارها لمشروع الإنتاج التالي.
- يمكن إنتاج الأشكال والتصميمات البسيطة فقط بكميات كبيرة. لا يمكن تزوير الأنماط الفريدة أو غير العادية أو المعقدة. مستويات التشوه ودرجات التشكيل محدودة، والمعادن المطروقة على البارد أقل ليونة.
- إن تغيير البنية الحبيبية للمعدن يمنحه قوة إضافية ولكنه قد ينتج عنه إجهاد متبقي.
- تتطلب بعض طرق الحدادة على البارد معالجات حرارية لإزالة الشقوق المحتملة أو التصلب الزاحف.
- هناك قيود على أنواع المعادن التي يمكن تزويرها على البارد. لا ينبغي اختيار المواد ذات الليونة المنخفضة والحساسية للتصلب بالإجهاد لأنها تفقد ليونتها وسوف تنكسر تحت إجهاد الشد. يمكن استخدام المعادن ذات الصلابة HRC 44 على مقياس روكويل فقط.
- تتطلب عمليات الإنتاج قدرًا كبيرًا من القوة لإنتاج قوة الضغط والضغط اللازمين. على الرغم من أن إضافة المكونات الهيدروليكية والهوائية قد أدى إلى تقليل حجم المعدات، إلا أنها لم تقلل من كمية الطاقة التي تستهلكها الآلات.
- يجب أن تكون الأدوات والقوالب والقوالب مصممة خصيصًا وأن تكون متينة وقوية بما يكفي لتكون قادرة على تحمل القوة المتكررة المستمرة.
الفصل الخامس – عمليات الحدادة على البارد
أدى تطور التقنيات المختلفة والتطورات في معالجة المعادن إلى إنتاج العديد من طرق تشكيل المعادن الباردة وتشكيلها. يخدم كل منها تطبيقًا مختلفًا، ولكن جميعها مصممة لإنتاج المنتجات بكفاءة وسرعة دون الحاجة إلى تشطيب ثانوي.
العمليات الثمانية الأكثر شيوعًا للتزوير على البارد هي:
- الانحناء
- المتداول الباردة
- يموت مغلق
- رسم
- البثق
- فتح يموت
- تزوير الدائري
- التطريق
وكما سأناقش في نهاية هذا الفصل، هناك عمليات أكثر من تلك المذكورة فقط. توفر لك الأوصاف أدناه خطًا أساسيًا من البيانات لفهم أولي للطرق المختلفة.
أيضًا، أحد الجوانب المهمة جدًا في عملية الحدادة على البارد هو نوع مادة التشحيم المستخدمة. النوعان الأكثر شيوعًا هما فوسفات الزنك أو أحد أشكال طلاء البوليمر. على الرغم من أن الحدادة على البارد تتم في درجة حرارة الغرفة، إلا أن عملية الثني والتشكيل تزيد من درجة حرارة المعادن. يمكن أن يمنع زيت التشحيم الأخطاء ويمنع قطعة العمل من الالتصاق بالقالب ويطيل عمر الأدوات.
يقدم مصنعو مواد التشحيم مجموعة متنوعة من المنتجات لتناسب كل نوع من عمليات الحدادة على البارد. في الصورة مواد تشحيم من الجرافيت، ولكن تتوفر أنواع خالية من الجرافيت بالإضافة إلى ألومينات الكالسيوم وفلوريد الألومنيوم وطلاءات الفوسفات.
طرق تزوير الباردة الشائعة:
الانحناء –
يتم إجراء الثني باستخدام مكبس وقالب حيث يتم ضغط قطعة العمل على أداة التشكيل. ويشار إليها أيضًا باسم الدرفلة الهرمية وتستخدم أحيانًا لتحضير قطعة لعملية تزوير باردة أخرى. يتم توتر قطعة العمل على طول محور واحد لتكوين زاوية.
الدرفلة على البارد –
الدرفلة هي عملية تشكيل حيث يتم تمرير المعدن من خلال زوج من بكرات دوارة لتشوه البلاستيك الناتج عن قوة الضغط. تنتج ضغوط الضغط احتكاكًا بين اللفات وسطح المخزون المعدني. يستخدم عادة لمعالجة الفولاذ.
قالب مغلق –
في عملية التشكيل بالقالب المغلق، يتم تشكيل قطعة العمل عن طريق ضربات ميكانيكية متتالية بعد وضعها بين نصفي القالب. نظرًا لأن المطرقة تضرب قطعة الشغل عدة مرات، يشير بعض المنتجين إلى الطرق بالقالب المغلق على أنه طرق بالسقوط. عندما يتم ضرب المعدن، فإنه يتدفق إلى تجاويف القالب ويغيره إلى شكل القالب.
رسم -
الرسم هو سحب قطعة العمل من خلال القالب باستخدام قوة الشد المطبقة عند مخرج القالب. أثناء سحب قطعة العمل، يحدث انخفاض في مساحة المقطع العرضي مع زيادة في طولها. تتمتع المعادن المشكلة بتسامح أبعاد أقرب مما يتم إنتاجه عن طريق الدرفلة.
البثق –
يتم دفع البليت أو البزاقة من خلال قالب، تحت قوة ضغط، والتي لها شكل الجزء النهائي. بمجرد مرورها، يتم قطعها إلى الطول المطلوب، أو إعدادها للشحن، أو إرسالها لمزيد من المعالجة. يمكن أن تصل القوة المطبقة في البثق البارد إلى 20000 كيلو نيوتن أو 2007 طن. يمكن إجراء البثق للأمام أو للخلف أو في كلا الاتجاهين.
البثق الأمامي – يتم دفع المعدن للأمام من خلال القالب.
البثق للخلف – يدخل المعدن إلى القالب للخلف ليشكل ثقوبًا أو أكوابًا مما يجعل الجزء السفلي أكثر سمكًا من جوانبه.
البثق الجانبي - يتم تطبيق القوة بشكل جانبي، جانبيًا، في اتجاه البثق لإضافة ميزة ثانية إلى المظهر الجانبي.
قالب مفتوح:
يتضمن تزوير القالب المفتوح قالبين مسطحين بدون ملف تعريف مقطوع مسبقًا. يتم تشكيل قطعة العمل تدريجياً باستخدام عدة عمليات مما يسمح بإنتاج مجموعة واسعة من الأشكال والأحجام. يتم استخدامه في الغالب مع التصميمات التي تتضمن مكونات معدنية كبيرة تتطلب أعلى درجات السلامة الهيكلية. يتم تحقيق التشوه عن طريق إعادة وضع قطعة العمل.
الضغط، المعروف أيضًا باسم التحجيم، هو شكل من أشكال المعالجة بالقالب المفتوح حيث يتم تطبيق القوة على مسافة قصيرة لإنتاج لمسة نهائية دقيقة الأبعاد.
تزوير الدائري –
مع تشكيل الحلقة، يتم ثقب قطعة عمل دائرية في المنتصف لإنتاج شكل الدونات. أثناء تدوير القطعة المثقوبة، يتم طرقها وضغطها. تنتج العملية حلقات غير ملحومة بأقطار وقوة مثالية.
التطريق –
التأرجح، أو التزوير الشعاعي، هو تشويه لقطعة العمل بحيث يتناسب الجزءان معًا. إنها آلية وموثوقة للغاية. هناك نوعان من التأرجح هما الأنبوب والشعاعي. يشبه تأرجح الأنبوب عملية البثق حيث يتم دفع قطعة العمل عبر القالب. مع التطريق الشعاعي، تقوم المطرقة بدفع قطعة العمل من خلال قالبين أو أكثر.
عندما تبدأ بحثك عن شركة تصنيع الطرق على البارد، ستجد طرقًا أكثر من الطرق السبع الموصوفة هنا. سيساعدك الفهم الأساسي لعدد قليل من الأساليب الممكنة على التحدث بشكل موثوق وذكي إلى المنتجين بالإضافة إلى القدرة على تفسير لغتهم.
كما هو الحال مع أي طريقة إنتاج حديثة، ستجد أن الحدادة على البارد تنمو باستمرار مع تطور التقنيات والأساليب الجديدة. أحد العوامل المهمة والمتزايدة هو إضافة الأتمتة والروبوتات، والتي تغير وجه الصناعة بسرعة. يمكن لمتخصص الحدادة أن يوجهك في الاتجاه الصحيح للعثور على العملية التي تناسب احتياجاتك على أفضل وجه.
الفصل السادس – معدات وآلات الحدادة على البارد
تأتي معدات وآلات الحدادة على البارد في ثلاثة أنواع – هيدروليكية وهوائية وميكانيكية. في حين أن بعض الموردين يتخصصون في نوع واحد فقط، ستجد أن الأغلبية لديهم عدة خيارات حسب السعر ونوع العملية. التكنولوجيا والأتمتة شائعة كما ترون في الصورة أدناه، وهي عبارة عن مكبس حدادة مؤازر على البارد من شركة Marvel Machinery. يتم إنشاء عروض تصميم الأجزاء باستخدام برامج هندسية مثل CAD.
هناك متطلبات يجب أن تستوفيها الآلات حتى يتم استخدامها للتزوير على البارد.
- القوة - تعتمد عمليات التشكيل على البارد على قدر هائل من القوة. ويجب أن تكون المعدات المرتبطة بها قادرة على امتصاص تلك القوة وتبديدها.
- التوازن - يجب أن تكون الآلات متوازنة بشكل ثابت وديناميكي لتقليل الاهتزازات وتحسين الأداء.
- القدرة على التحمل مع مرور الوقت – بغض النظر عن طريقة التشكيل على البارد، فإن كل منها يتطلب قوة متكررة قوية. لكي تستمر الآلة، يجب أن تكون قادرة على تحمل تلك القوة.
- عمليات متعددة – تقوم آلات التشكيل أو التشكيل على البارد الحديثة، والتي تسمى الرؤوس، بإكمال عملية واحدة إلى عدة عمليات خلال عملية واحدة. يعد ذلك ضروريًا نظرًا لوجود قدر محدود من التشوه الذي يمكن إجراؤه بضربة واحدة.
أنواع معدات الحدادة على البارد:
مطرقة تزوير القالب الهيدروليكي –
تم تصميم مطرقة الطرق الهيدروليكية لتوفير أقصى قدر من القوة بأقل استثمار. يمكن أن تنتج مجموعة واسعة من الانطباعات من مجموعة متنوعة من القوالب. إنه يعمل باستخدام المفاهيم الهندسية للمكونات الهيدروليكية حيث يوجد سائل غير قابل للضغط في الأسطوانة. عندما يتم ضغط السائل بواسطة مكبس، يتم دفع العمود، مع القالب المرفق، إلى أسفل على قطعة العمل.
الصحافة المسمار –
يتم استخدام المكبس اللولبي للتشوه الكبير بسبب سرعة الضغط البطيئة. يمكن استخدامه للقوالب الخالية من الفلاش والمطروقات الطويلة للقضبان. يسمح تكوين المكبس اللولبي باستخدامه في قوالب الفتحة المفردة التي تشمل الثني والمطروقات النهائية. يوفر المحرك الكهربائي القدرة على تشغيل المسمار الذي يدفع القالب إلى قطعة العمل.
مكبس عالي السرعة للإطار C –
تصميم الإطار C مناسب لعمليات التشكيل، واللكم، والثني، والضغط المتعدد. إنها تأتي بتصميمات كرنك فردية أو مزدوجة بقوة ثقب تتراوح من 110 إلى 400 طن وشوط انزلاقي يتراوح من 110 إلى 280 ملم. يمكنها قبول ارتفاعات القالب من 435 إلى 600 ملم ويمكن استخدامها لإنتاج أجزاء صغيرة.
الصحافة السلطة الهوائية –
يمكن للضغط الذي يعمل بالهواء المضغوط أن يغطي النطاق الكامل لوظائف الضغط بالقالب. إنها تأتي مع قابض احتكاك وفرامل يعملان بالهواء المضغوط. يتم إنتاج طاقة المكبس بواسطة ضاغط هواء يدفع مطرقة الحدادة إلى الأسفل على قطعة العمل عن طريق ضغط الهواء في أسطوانة بمكبس.
الصحافة الباردة الميكانيكية –
من بين أنواع آلات الحدادة على البارد، أصبحت النسخة الميكانيكية هي الأقل استخدامًا لأنها تحتاج إلى أن تكون كبيرة جدًا لتوفير القوة اللازمة. لديهم دولاب الموازنة الذي يخزن الطاقة من المحرك. عندما يتم تنشيط دولاب الموازنة، فإنه يدفع المطرقة أو يضغط على القالب. يمكنه توفير الطاقة على مدار عدة دورات ولكن يجب أن يظل في وضع الخمول لاستعادة الطاقة من محركه قبل أن يتمكن من مواصلة دوراته.
من بين العديد من أنواع معدات الحدادة على البارد، فإن الأنواع الأكثر شيوعًا هي الهيدروليكية والهوائية، لأنها تشغل مساحة أقل، ويمكن أن توفر كميات متنوعة من القوة، وقابلة للبرمجة. عندما تقوم بفحص اختياراتك للإنتاج، فمن الأفضل معرفة أنواع المعدات التي يمتلكها المنتج نظرًا لأن المعدات الحديثة من المرجح أن تنتج أجزاء ذات جودة أفضل.
الفصل السابع – أنواع المعادن المطروقة
يقدم التشكيل على البارد مجموعة واسعة من الخيارات عندما تختار معدنًا لمشروع ما. تشمل الأصناف المختلفة معادن صلبة مثل الفولاذ الكربوني وسبائك الفولاذ والفولاذ المقاوم للصدأ. الألومنيوم والنحاس والنحاس والسيليكون والمغنيسيوم هي معادن ناعمة يمكن استخدامها. الشرط الوحيد لأي معدن هو أن تكون صلابته 44 HRC أو أقل على مقياس روكويل.
نحاس -
يعد النحاس معدنًا ممتازًا للتزوير على البارد نظرًا لأنه شديد المرونة والمرونة. يمكن تشكيلها أو ثنيها أو سحبها بقوة قليلة وتنتج أجزاء مقاومة للتآكل والصدأ.
الألومنيوم –
الألومنيوم معدن غير حديدي خفيف للغاية وذو كثافة منخفضة. تبلغ درجة حرارة ذوبانه 1220 درجة فهرنهايت وهو مرن ومقاوم للصدأ والتآكل.
الصلب الكربوني –
الصلب الكربوني عبارة عن سبيكة من الحديد والكربون. وتعتمد الدرجات المختلفة على كمية الكربون الممزوجة بالحديد. لديها قوة استثنائية والليونة.
الفولاذ المقاوم للصدأ –
أصبح الفولاذ المقاوم للصدأ أحد أكثر المعادن استخدامًا لمقاومته للتآكل ومظهره وقوته. على الرغم من أن مصطلح الفولاذ المقاوم للصدأ يستخدم بشكل عام لوصف أي فولاذ له خصائصه، إلا أن الفولاذ المقاوم للصدأ يأتي في مجموعة متنوعة من الدرجات اعتمادًا على محتوى السبائك.
الفولاذ المستخدم للتزوير على البارد
فولاذ منخفض الكربون بمحتوى كربون يتراوح من 0.1% إلى 0.25%. يعمل التشكيل على البارد على تحسين تصلب الفولاذ في الفولاذ مما يزيل الحاجة إلى الأوستنة أو التبريد أو التلدين.
معادن مناسبة للتزوير على البارد
سبيكة مناسبة | خاصية التشكيل على البارد |
---|---|
نحاس | ممتاز |
الذهب والفضة ومعظم سبائكهما | ممتاز |
النحاس - خرطوشة النحاس | جيد |
البلاتين والبلاديوم والتنتالوم وسبائكها | معظمها قابلة للتشكيل على البارد. |
التيتانيوم وسبائكه | نعم، Ti نقي وسبائك ذات ليونة عالية، لكن السبائك مثل 6-4 هي فقط قادرة على التسخين بالرأس. |
النيكل وسبائكه | ني نقي نعم، سبائك ذات استطالة في درجة حرارة الغرفة بنسبة 20٪ أو أكثر، نعم. |
الحديد والفولاذ | الحديد النقي، نعم. الفولاذ، يعتمد على الفولاذ. العديد منها قابلة للتشكيل على البارد. |
اعتبارات عند اختيار المعدن:
الشيء الأكثر منطقية وأهمية الذي يمكنك القيام به عندما تتخذ قرارًا بشأن المعدن لمشروع ما هو إجراء بحث. يتفاعل كل نوع من المعدن مع التلدين والتشوه بطرق مختلفة. يجب أن يتناسب المعدن الذي تختاره مع استخدامه النهائي والقوة التي تحتاجها. إذا استشرت أحد خبراء الحدادة، يمكنك الحصول على معلومات قيمة يمكن أن ترشدك إلى اتخاذ القرار الصحيح.
الفصل الثامن – تطبيقات الحدادة على البارد
ينتج التشكيل على البارد أشكالًا من أي حجم بدرجة عالية من دقة الأبعاد والدقة الهيكلية. إن الكفاءة الاقتصادية وسرعة التشكيل على البارد جعلته بديل الإنتاج الأكثر شعبية.
يلبي التشكيل على البارد متطلبات الصناعات الحديثة لأنه:
- تعظيم استخدام المواد الخام: الاستثمار الرئيسي لأي عملية هو المواد الخام. عملية الحدادة على البارد لها نفايات محدودة للغاية. يمكن إعادة الفلاش والقطع إلى عملية التصنيع.
- تقليل التكاليف: بما أن الأجزاء يتم إنتاجها بسرعة، فإن تكلفة الوحدة منخفضة جدًا مما يجعل المنتجات النهائية أكثر ربحية وأقل تكلفة في الإنتاج.
- تنتج أجزاء عالية الجودة: يعمل التشكيل على البارد على زيادة قوة ومتانة الأجزاء والمنتجات مما يضمن استمرارها لفترة أطول. لا يتغير هيكل وخصائص القطعة المشكلة مما يوفر دقة أبعاد ممتازة.
التطبيقات التي يتم فيها استخدام الأجزاء المزورة على البارد:
السيارات –
إن القوة العالية والموثوقية والجودة والأسعار المعقولة للطرق على البارد جعلتها جذابة للغاية لتصنيع السيارات. يتم تركيب الأجزاء المطروقة على البارد عند نقاط ضغط عالية بسبب مقاومتها الممتازة للصدمات. المكونات مثل قطارات القيادة، وأعمدة القيادة، والدعامات أو الصدمات يتم تشكيلها على البارد. الرسم البياني أدناه هو عرض لبعض أجزاء الهيكل السفلي للسيارة التي يتم إنتاجها عن طريق الطرق البارد.
الأدوات اليدوية والأجهزة –
تم إنتاج الموصلات مثل المسامير والمسامير والمسامير والصواميل عن طريق الطرق البارد لسنوات. إن التفاوتات المنخفضة ودقة الأبعاد الممتازة هي السبب وراء تفضيل منتجي الأدوات اليدوية للطرق البارد على الطرق الأخرى مثل التصنيع.
جيش -
لدى الجيش شروط صارمة للغاية فيما يتعلق بالمعدات العسكرية ويختار التطريق على البارد لتصنيع أغلفة القذائف والرصاص وغيرها من المعدات العسكرية. تتمتع الأجزاء بموثوقية وأداء عاليين في أوقات الأزمات. إن التفاوتات المنخفضة وقوة الأجزاء تجعلها مثالية للأسلحة العسكرية.
إنتاج العتاد –
يتم استخدام الطرق البارد لإنتاج التروس لأنه يلغي الحاجة إلى القطع في تشكيل التروس. يمكن إنتاج التروس من قطع معدنية يقل حجمها عن 50 مم أو يتم تشكيلها باستخدام سلك ملفوف. قد يكون بعض التلدين ضروريًا لإزالة الإجهاد المتبقي وتصلب العمل. من المزايا المهمة للتروس المسبوكة على البارد مدى سلاسة وهدوء تداخلها.
خاتمة
- يؤدي التشكيل على البارد إلى إنتاج معادن ذات تفاوتات منخفضة ودقة أبعاد عالية بتكلفة منخفضة جدًا وكميات كبيرة.
- يؤدي التزوير على البارد بسرعة وبسرعة إلى إنشاء الأجزاء النهائية المتوفرة والكاملة على الفور.
- سيقدم لك المصنعون مجموعة واسعة من العمليات لإنتاج الجزء الذي تحتاجه بدقة ودقة باستخدام أحدث المعدات وأكثرها تقدمًا تقنيًا.
- سيكون لديك مجموعة واسعة من المعادن للاختيار من بينها لإنجاز مشروعك بدءًا من الفولاذ المقسى والفولاذ المقاوم للصدأ وحتى النحاس والألومنيوم.
- ستجد قيودًا قليلة جدًا على عدد المنتجات التي يمكنك إنتاجها بدءًا من المكونات التي تتحمل الضغط لسيارتك وحتى المسامير والتروس وأدوات العمل.
- عند مقارنة الحدادة الباردة والساخنة، ستجد أن الحدادة الباردة تستغرق وقتًا أقل وتنتج أجزاء ومنتجات أقوى وأطول أمدًا.