The main differences between 5083 and 5052 aluminum alloys lie in their chemical compositions and properties, particularly in terms of their strength, corrosion resistance, and applications:
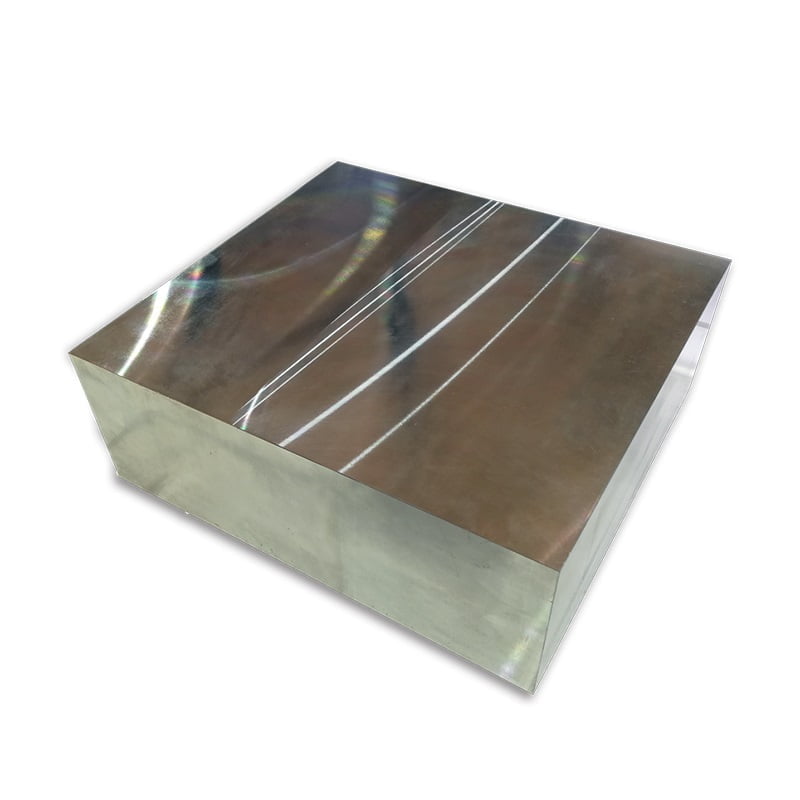
- درجة حرارة التقسية:
- 5083 Aluminum Alloy: Primarily alloyed with magnesium (4.0% to 4.9%) and traces of manganese, chromium, and titanium. This alloy is known for its exceptional performance in extreme environments and excellent resistance to seawater and industrial chemicals.
- 5052 Aluminum Alloy: Contains magnesium (2.2% to 2.8%) and chromium, but less magnesium compared to 5083. It is generally softer and more formable than 5083, making it suitable for less demanding applications where strength and corrosion resistance are still important.
- قوة:
- 5083: Offers higher strength than 5052, especially in thicker sections. It is commonly used in marine applications where high strength and resistance to corrosion are critical.
- 5052: While not as strong as 5083, it is still a relatively strong alloy and is preferred in applications requiring good formability and corrosion resistance without the need for high strength.
- المقاومة للتآكل:
- 5083: Has excellent corrosion resistance, particularly in marine environments. It is highly resistant to seawater and industrial chemicals, making it ideal for shipbuilding and offshore structures.
- 5052: Also has good corrosion resistance, though not as high as 5083. It is suitable for general sheet metal work where moderate strength and good corrosion resistance are required.
- التطبيقات:
- 5083: Mainly used in industries requiring high strength and excellent corrosion resistance, such as marine applications (shipbuilding, offshore platforms), transportation (automotive, railcars), and industrial applications (chemical processing equipment).
- 5052: Commonly used for sheet metal work, including panels for vehicles, trailers, and appliances, as well as in marine environments where moderate strength and good corrosion resistance are sufficient.
In summary, while both 5083 and 5052 aluminum alloys offer good corrosion resistance and are suitable for various applications, 5083 excels in environments requiring high strength and exceptional corrosion resistance, such as marine and offshore applications. 5052 is softer and more formable, making it suitable for less demanding applications where strength requirements are lower but corrosion resistance is still important.